Troubleshooting guide – ACU-RITE MILLPWR 3 Axes User Manual
Page 240
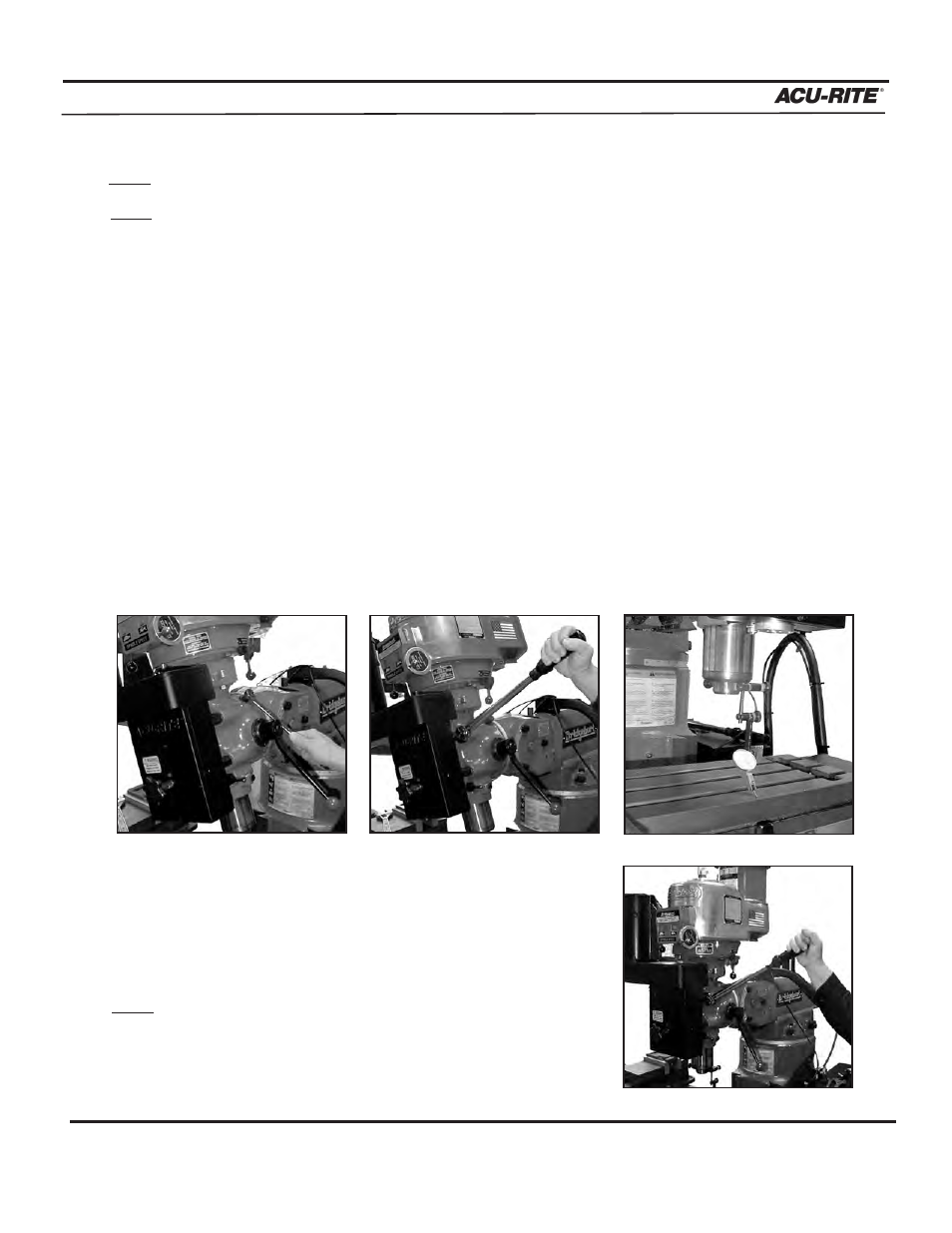
TROUBLESHOOTING GUIDE
MILLPWR
®
Operation Manual
1. When the head is re-positioned to mill certain angles (see
Figure 1
) torque the four (4)
coupling nuts that secure the Z-axis casting to the head to 50 ft/lbs while the head is in that
position (see
Figure 2
).
2. When the milling head is repositioned to “0” degrees, use a dial indicator to fine-tune the accu-
racy of the head’s position (see
Figure 3
).
3. Ensure the knee lock clamps on the machine saddle are tight.
4. Follow the machine manufacturer’s procedure for proper milling head calibration and alignment.
5. Once the dial indicator shows a “0” reading in several locations
of the table and the head is trammed in, re-torque the four (4)
coupling nuts to 50 ft/lbs (see
Figure 4
). As you tighten, make
sure the dial indicator maintains its “0” reading.
9-15
Re-aligning (Tramming) the Spindle
You will need the following components:
• Box or open-ended wrench
• Crow’s foot torque wrench 7/8”
When the head has been re-angled the following procedure should be performed so the original accura-
cy can be re-established. Do not loosen casting bolts or hex nuts; loosen the tramming hex stand-offs
only.
• Dial indicator
• Dial holder
Note: This does not require re-aligning the quill casting.
Fig. 1
Fig. 2
Fig. 3
Fig. 4
Note: If the 50 ft/lbs torque specification is not applied, the
engage/disengage mechanism may not engage the
Z-axis ballscrew nut correctly. This may also create a
binding and/or undue wear to the spindle within the
mill head.
Note: The Z-axis is still fully functional in a tilted position.