Elecraft K2 Owner's Manual User Manual
Page 13
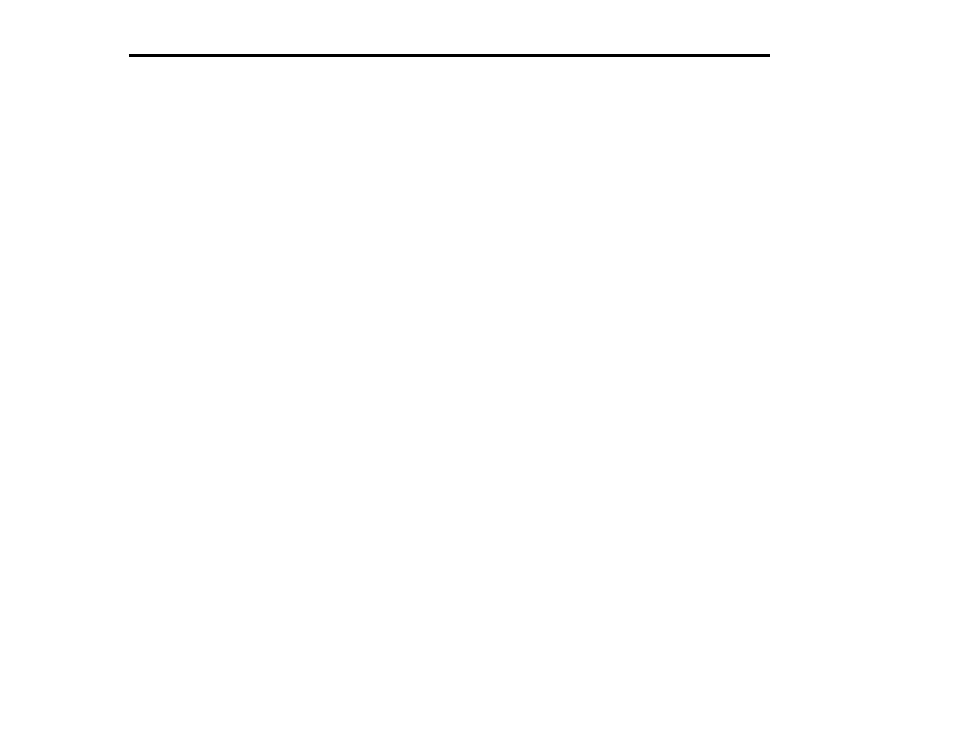
12
E
LECRAFT
®
Integrated Circuits and ESD
The K2 transceiver uses integrated circuits and transistors that can be
damaged by electrostatic discharge (ESD). Problems caused by ESD
can often be difficult to troubleshoot because components may only be
degraded, at first, rather than fail completely.
To avoid such problems, simply touch an unpainted, grounded metal
surface before handling any components, and occasionally as you
build. We also recommend that you take the following anti-static
precautions (in order of importance):
Leave ESD-sensitive parts in their anti-static packaging until you
install them
Ground yourself using a wrist strap with a series 1 megohm
resistor (do NOT ground yourself directly, as this poses a shock
hazard)
Make sure your soldering iron has a grounded tip
Use an anti-static mat on your work bench
IC Sockets
Sockets are used for only the largest ICs. You should not use sockets
for the other ICs because they tend to be unreliable and can cause
problems due to added lead length. Since sockets are not used in most
cases, you must double-check the part number and orientation of each
IC before soldering.
Soldering, Desoldering, and Plated-Through Holes
CAUTION: Solder contains lead, and its residue can be toxic.
Always wash your hands after handling solder.
The printed circuit boards used in the K2 have circuitry on both sides
("double-sided"). Boards of this type require plated-through holes to
complete electrical connections between the two sides.
When you solder components on these boards, the solder fills the
plated holes, making excellent contact. This means that you do not
need to leave a large "fillet" or build-up of solder on top of the pads
themselves. A small amount of solder will do for all connections.
Unfortunately, removing components from double-sided PC boards
can be difficult, since you must get all of the solder back out of the
hole before a lead can be removed. To do this, you'll need solder wick
and a vacuum desoldering tool (see techniques below).
The best strategy for avoiding de-soldering is to place all components
properly the first time. Double-check values and orientations, and
avoid damaging parts via ESD.
When removing components:
Don't pull a lead or pin out of a hole unless the solder has been
removed, or you are applying heat. Otherwise, you can literally
pull out the plating on the plated-through hole.
Limit soldering iron contact to a few seconds at a time.
Use small-size solder-wick, about 0.1" or 2.5 mm wide. Use the
wick on both the top and bottom pads when possible. This helps
get all of the solder out of the hole.
Buy and learn how to use a large hand-operated vacuum
desoldering tool, such as the "Soldapullt," model DS017LS. Small
solder suckers are not effective.
With ICs and connectors, clip all of the pins at the body first, then
remove all of the pins slowly, one at a time. You may damage
pads and traces by trying to remove a component intact, possibly
leaving a PC board very difficult to repair.
Invest in a PC board vice with a heavy base if possible. This
makes parts removal easier because it frees up both hands.
If in doubt about a particular repair, ask for advice from Elecraft
or from a someone else with PCB repair experience. Our e-mail
reflector is also an excellent source for help.