Festo Электромотор MTR-DCI User Manual
Page 169
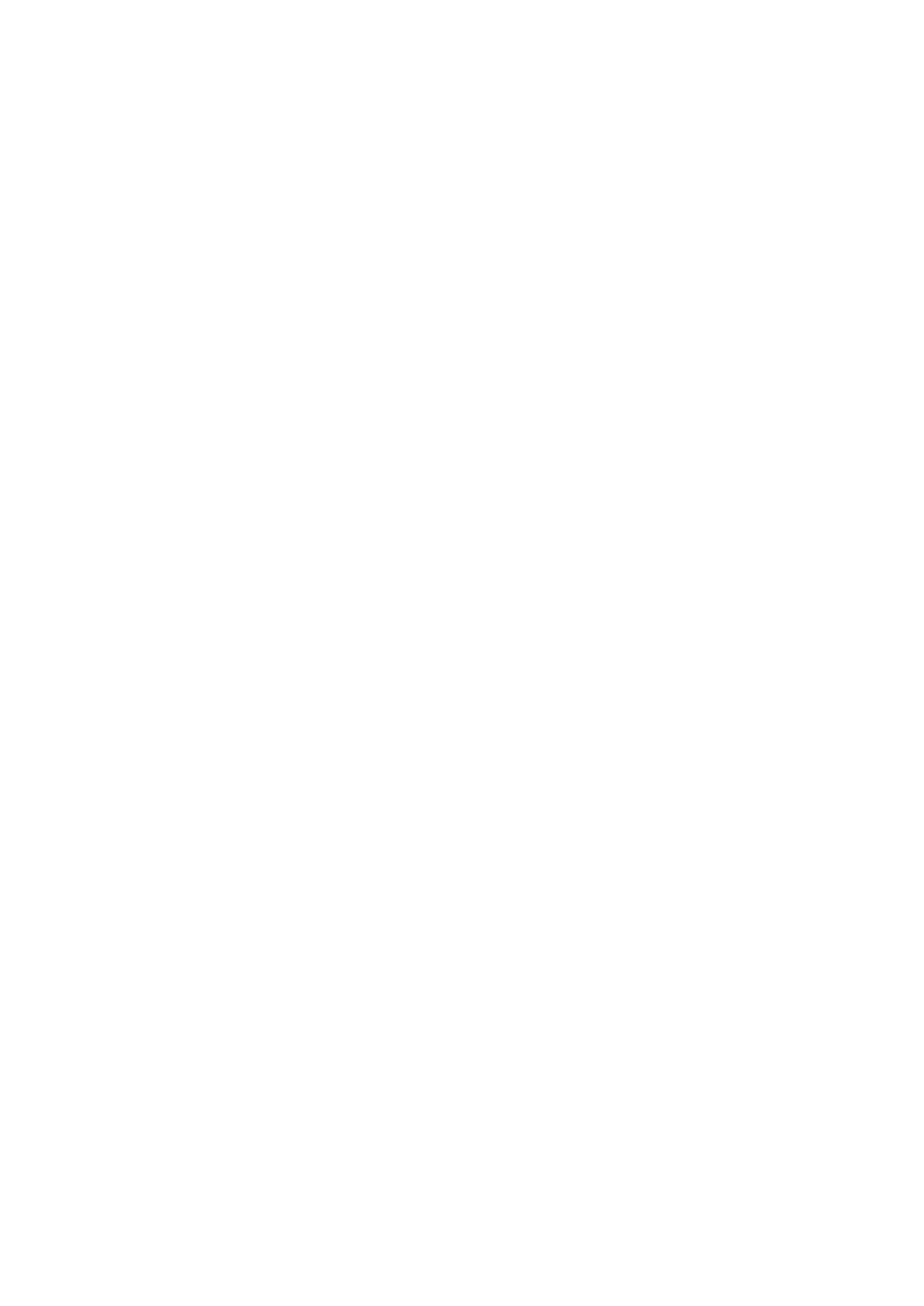
5. Commissioning
5-71
Festo P.BE-MTR-DCI-DN-EN en 1209a
Sequence
1. The user specifies the desired nominal value (in % of the
rated motor torque) and the speed limit in his/her output
data.
2. With a rising edge on Start (CPOS.B1) the controller
accepts the nominal torque and begins applying force/
torque in the direction indicated by the nominal value's
sign.
–
Once this speed has been reached, the “Speed limit
reached” bit is set in the (status byte SDIR).
–
Once the nominal value has been reached, taking into
account the target window and the time window, the
“MC” signal is set. The motor current continues to be
controlled.
–
In the case of resistance, e.g. from a workpiece in the
traversing range, the drive pushes against the
obstruction with a defined force (see Fig. 5/8).
–
If the distance set in path/stroke monitoring (relative
to the start position) is exceeded, the bit “Stroke limit
reached” is set in the status byte SDIR. The drive is
braked with the emergency-stop ramp, is then held in
a controlled position (the current position), and the
MC signal is set.
Possible causes of faults:
–
Homing not carried out.
–
Axis is at the SW end position when the positioning task
starts.