Force mode – Festo Электромотор MTR-DCI User Manual
Page 167
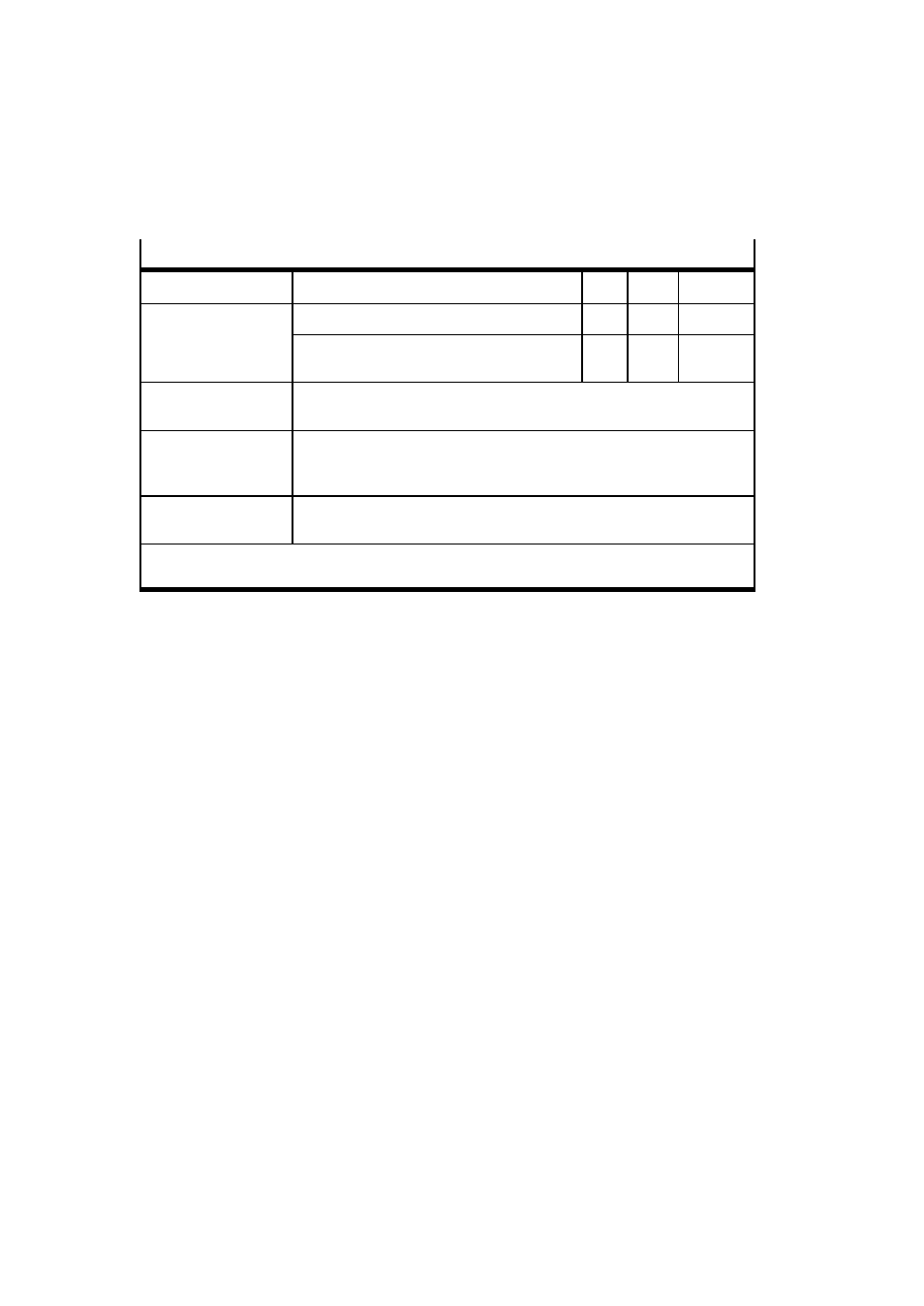
5. Commissioning
5-69
Festo P.BE-MTR-DCI-DN-EN en 1209a
Overview of parameters involved (see section B.2.9)
Parameters involved
Description
FCT
PNU
CI
Nominal value for
positioning mode
Max. permissible speed
1)
x
502
21F6/00h
Direct mode acceleration in acceleration unit
(inc/s
2
)
x
541
20EE/22h
Start
(FHPP control byte)
CPOS.B1 = positive edge: Start
(CDIR.B0 = nominal position absolute/relative)
Feedback
(FHPP status byte)
SPOS.B2 = 0: Motion complete
SPOS.B1 = positive edge: Acknowledge start
SPOS.B4 = 1: Drive is moving
Requirement
Device control by PLC/Fieldbus
Controller must be in status “Operation enabled”
1)
The master transmits a percentage value in the output data, which is multiplied by the maximum
permissible speed in order to obtain the final nominal speed.
Tab. 5/22: Parameters involved in a direct task (positioning mode)
Force mode
The force mode is used in the following situations:
–
For clamping and holding workpieces, as well as for pro-
cesses where workpieces must be aligned (e.g. to a fixed
stop).
–
Pressing and joining processes.
–
Special functions where (e.g.) workpieces must be probed
in order to obtain position values.