Routing high and low voltage cables – Rockwell Automation 1326 Digital AC Multi-Axis Motion Control System User Manual User Manual
Page 49
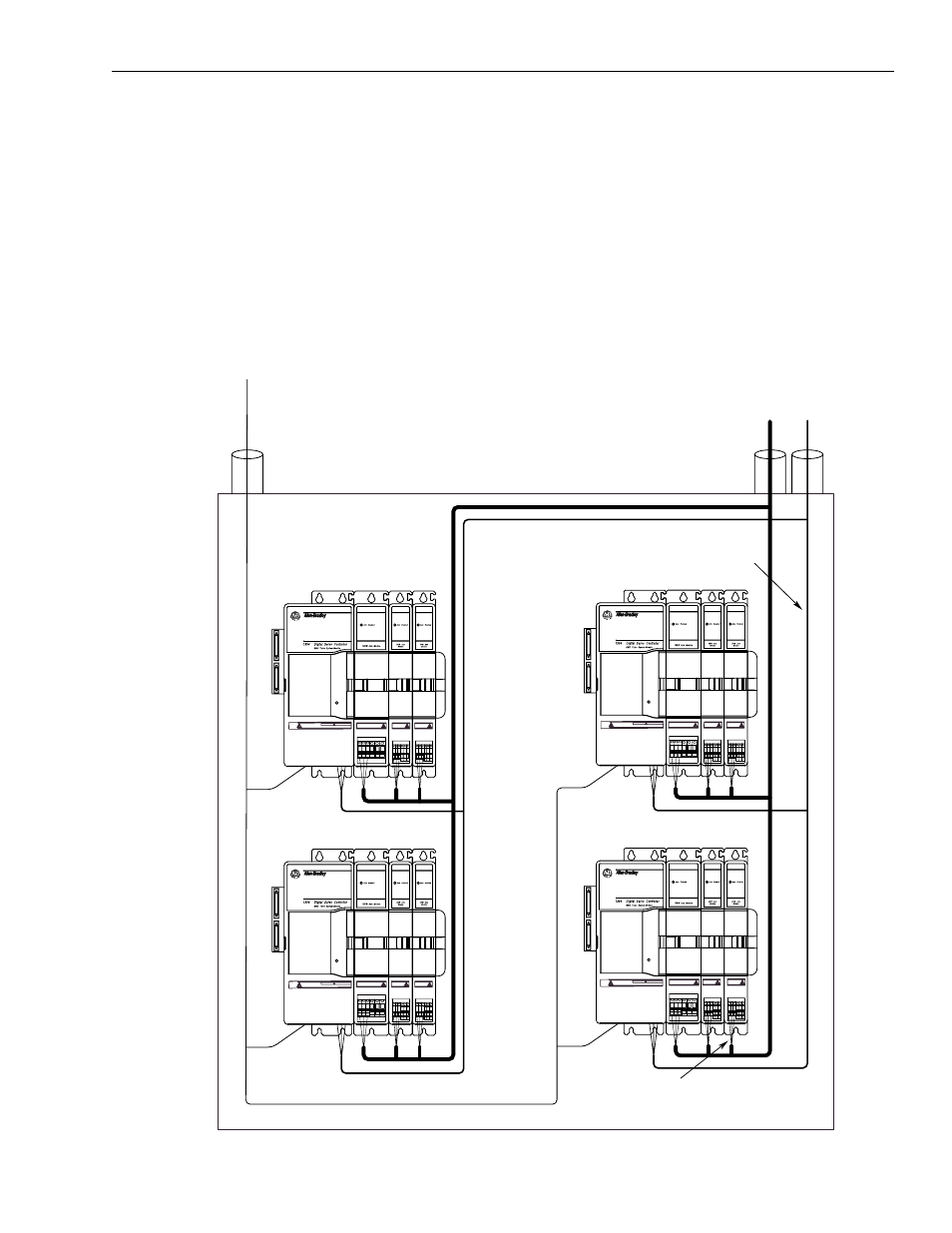
Publication 1394-5.0 — May 2000
Wiring System, Axis, and Shunt Modules, and Motors (for all systems)
3-3
Routing High and Low Voltage Cables
Be aware that when you connect and route power and signal wiring
on a machine or system, radiated noise from nearby relays (relay coils
should have surge suppressors), transformers, and other electronic
drives can be induced into motor or encoder feedback,
communications, or other sensitive, low voltage signals. This can
cause system faults and communication problems. To minimize the
levels of radiated noise, route machine power and signal lines
separately.
Figure 3.1
Routing Cables Inside Your Cabinet
Low voltage
Communications
Control I/O wiring
Motor feedback cables
460/380V
AC power
Always separate all low voltage signal wiring
from high voltage power wiring to reduce affects
of EMI and RFI.
Status
Status
Status
Status
Motor power
cables
Unshielded
conductors
Unshielded lead length
less than or equal to
76.2 mm (3.0 in.)
Always cross high and low voltage
conductors at 90 degree angles.
Maximize
distance
between high
and low voltage
cables on
parallel runs
Do not run low
and high voltage
wires in the
same wire way
DANGER
RISK OF ELECTRICAL SHOCK. HIGH VOLTAGE MAY
EXIST UP TO FIVE MINUTES AFTER REMOVING POWER.
DANGER
RISK OF ELECTRICAL SHOCK. HIGH VOLTAGE MAY
EXIST UP TO FIVE MINUTES AFTER REMOVING POWER.
DANGER
RISK OF ELECTRICAL SHOCK. HIGH VOLTAGE MAY
EXIST UP TO FIVE MINUTES AFTER REMOVING POWER.
DANGER
RISK OF ELECTRICAL SHOCK. HIGH VOLTAGE MAY
EXIST UP TO FIVE MINUTES AFTER REMOVING POWER.