Rockwell Automation 1326 Digital AC Multi-Axis Motion Control System User Manual User Manual
Page 234
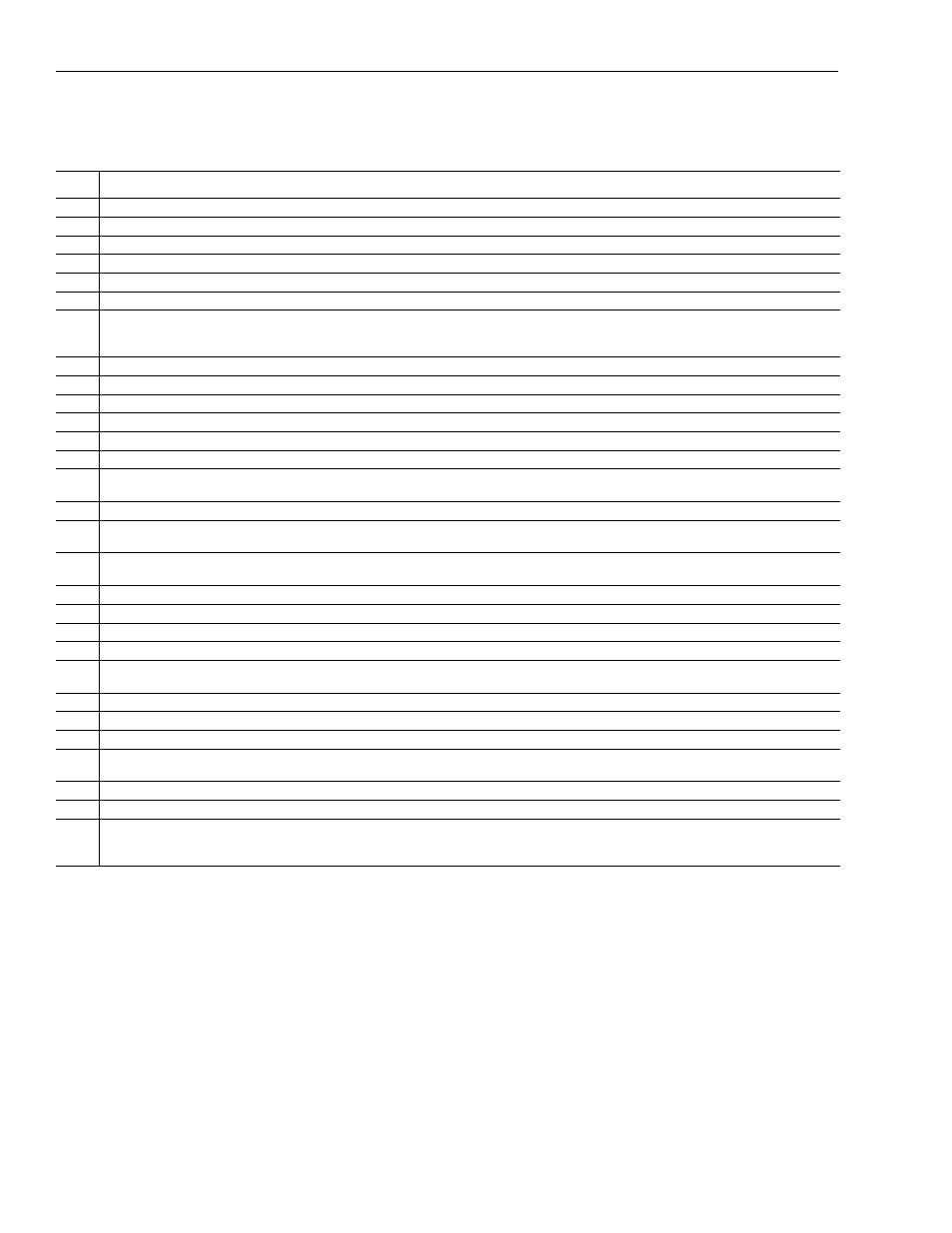
Publication 1394-5.0 — May 2000
B-2
Interconnect and CE Diagrams
GMC, Analog Servo, and CNC
Interface Interconnect Diagrams
The following notes apply to the interconnect diagrams on the following
pages.
Note: To determine the series of your module, refer to Figure P.1 in
the Preface.
Note:
Information:
1
Power wiring is 3.3 mm
2
(12 AWG), 75
°
C (167
°
F) minimum, copper wire.
2
Input fuse to be Bussmann. Refer to
Appendix A for sizes
3
Control Wiring: 0.82 mm
2
(18 AWG) minimum, 15A maximum.
4
Allen-Bradley motor cables. Refer to 1326 Cables for 460V AC Servo Motors (publication 1326A-2.11).
5
Terminate shield on one end only.
6
Contactor coil (M1) needs an integrated surge suppressors for AC coil operation.
7
TB1 pins 24, 25, 26 (16, 17, 18 on Analog Servo) are used for speed and current output commands.
±
1.2V DC/1000 rpm (velocity) and
±
3V DC =
100% (current),
±
6V DC = 200%
±
9V DC = 300% (current command). Use the parameter link function to read the outputs for Axis 0, 1, 2 or 3 (analog
servo only).
8
The RIO/AxisLink option (-RL) must be ordered with the system module and is installed at the factory. You cannot order these individually.
9
AxisLink and RIO board connections use Allen-Bradley 1770-CD (Belden 9463 or equivalent).
10
Use 4100-CCFl or -CCF3 Flex I/O cables. Cable length must not exceed 0.91 m (36 in.).
11
User-supplied 5V DC power source is required for encoder board regardless if encoder supply voltage is 5V or not.
12
Resolver inputs for Axis 0 (J5/FB0) are shown. Axis 1, 2 and 3 are identical - use J6/FB1 for Axis 1, J7/FB2 for Axis 2 and J10/FB3 for Axis 3.
13
Jumper is factory set for grounded system at user site. Ungrounded sites must jumper the bleeder resistor to prevent high electrostatic buildup.
14
For multiple axis systems requiring all axes to fault when one motor therm sensor trips - interconnect TB2, pin 3 of each axis to TB2 pin 4 of the
adjacent axis. For single-axis control, wire each axis separately.
15
Either TB1-1, 2 or TB2-1, 2 system enable needs to be energized to enable (hardware) up to four axes. You do not need both TB1-1, 2 and TB2-1, 2.
16
System enable can be: 1) always tied to 24V DC, use GML software to enable each axis, 2) inserted in the ESTOP string to pull in/out with the M1
contactor, or 3) used in a secondary stop string (for example, photoeye work area).
17
You must jumper P1 for the optional external shunt resistor (5 and 10 kW Series A and B only). P1 is located behind the Status LED. The P1 jumper
is available with the external shunt kit (1394-SR10A) and used on 1394-SJT05 and -SJT10 series A and B systems only.
18
You must supply source power for Flex I/O (for example, 1794-IB16-24V DC and 1794-IA8-115V AC).
19
This input is monitored by the CPU and is not intended to be a safety circuit.
20
The motor thermal switches should be wired in series to the customer stop circuit to prevent damage to the motor.
21
Ground bar is user-supplied item for (Series A and B) system modules. Ground bar is included on (Series C) system modules.
22
Brake control can be accomplished using the Flex I/O outputs and adding the appropriate logic to the GML application program. In this case, connect
the leads from the axis module TB2 to the appropriate Flex I/O output.
23
Brake control must be provided by the user-supplied controller.
24
The brake circuit must be routed to the CNC output module. The brake control logic must be configured in PAL.
25
There is no internal shunt resistor in the 22 kW smart system module. An external shunt resistor module (1394-SR
xAx) must be used.
26
The axis
x VREF and TREF are analog reference inputs to the drive. They are parallel to the VREF and TREF inputs on the input wiring board. You
can not use both set of inputs at the same time.
27
A user-supplied 5V DC power supply provides logic power to the 1394 Analog Servo. Applying 5V DC to one axis powers all four axes.
28
Grounding of the 24V DC common or the 24V AC neutral is recommended but not required. Grounding improves noise immunity to the logic supply.
29
The thermal switch and brake circuits are a source of conducted noise. Isolation from customer control devices may be required. A separate 24V
DC supply or relay can be used. Axis modules (Series C or later) include a thermal switch and motor brake filter to eliminate the need for a separate
24V DC supply.