NORD Drivesystems BU0180 User Manual
Page 99
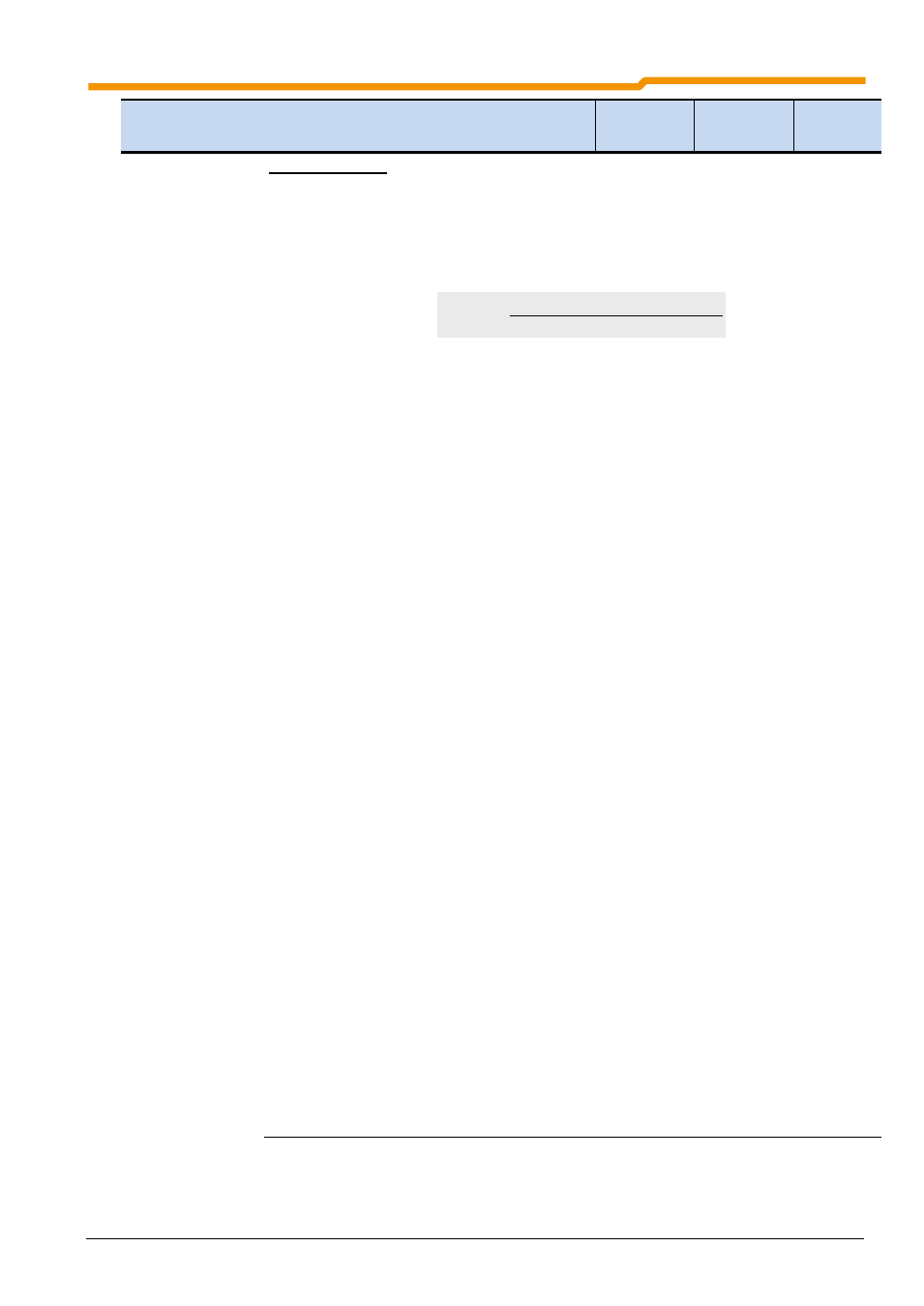
6 Parameterisation
BU 0180 GB-0914
Pre-series version
99
Parameter
{Factory setting}
Setting value / Description / Note
Device
Supervisor
Parameter
set
... only with
SK CU4-IOE or
SK TU4-IOE
Analog functions (max. load: 5mA analog):
An analog voltage (0 ... +10 Volt) can be taken from the control terminals (max. 5mA). Various
functions are available, whereby:
0 Volt analog voltage always corresponds to 0% of the selected value.
10 V always corresponds to the motor nominal values (unless otherwise stated) multiplied by the
P419 standardisation factor, e.g.:
100%
P419
value
nominal
Motor
10Volt
For standardisation of actual values: See also (Section 9.9 ).
0 = No function, no output signal at the terminals.
1 = Actual frequency *, the analog voltage is proportional to the FI output frequency.
(100%=(P201))
2 = Actual speed *, this is the synchronous speed calculated by the FI based on the existing
setpoint. Load-dependent speed fluctuations are not taken into account.
3 = Current *, the effective value of the output current supplied by the FI. (100%=(P203))
4 = Torque current *, displays the motor load torque calculated by the FI. (100% = (P112))
5 = Voltage *, the output voltage supplied by the FI. (100%=(P204))
6 = Link voltage, "Link circuit voltage", is the DC voltage in the FI. This is not based on the
motor rated data. 10V Volt, standardised at 100%, is equivalent to 450V DC (230V
mains) or 850 Volt DC (480V mains)!
7 = Value from P542, the analog output can be set using parameter P542 independently of
the actual operating status of the FI. For example, with Bus switching (parameter
command) this function can supply an analog value from the FI, which is triggered by the
control unit.
8 = Apparent power *, the actual apparent power of the motor as calculated by the FI.
(100%=(P203)*(P204) or = (P203)*(P204)*
√3)
9 = Effective power *, the actual effective power calculated by the FI.
(100%=(P203)*(P204)*(P206) bzw = (P203)*(P204)*(P206)*
√3)
10 = Torque [%]: the actual torque calculated by the FI (100%=Nominal motor torque).
11 = Field [%] *, the actual field in the motor calculated by the FI.
12 = Actual frequency ±*, the analog voltage is proportional to the output frequency of the FI,
whereby the zero point is shifted to 5V. For rotation to the right, values between 5V and
10V are output, and for rotation to the left values between 5V and 0V.
13 = Actual speed ± *, is the synchronic rotation speed calculated by the FI, based on the
current setpoint, where the null point has been shifted to 5V. For rotation to the right,
values from 5V to 10V are output and for rotation to the left, values from 5V to 0V.
The measured speed is output via this function if servo mode is used.
14 = Torque [%] ± *, is the actual torque calculated by the FI, whereby the zero point is shifted
to 5 V. For drive torques, values between 5V and 10V are output, and for generator
torque, values between 5V and 0V.
29 = Reserved
30 = Set freq befor ramp, "Setpoint frequency before frequency ramp", displays the frequency
produced by any upstream controllers (ISD, PID, etc.). This is then the setpoint frequency
for the power stage after it has been adjusted by the start-up or braking ramp (P102,
P103).
31 = Output via BUS PZD, the analog output is controlled via a bus system. The process data
is directly transferred (P546, P547, P548).
33 = Setpoint freq.
Motor pot, "Setpoint frequency of motor potentiometer"
*) Values based on the motor data (P201…), or which are calculated from this.