NORD Drivesystems BU0180 User Manual
Page 142
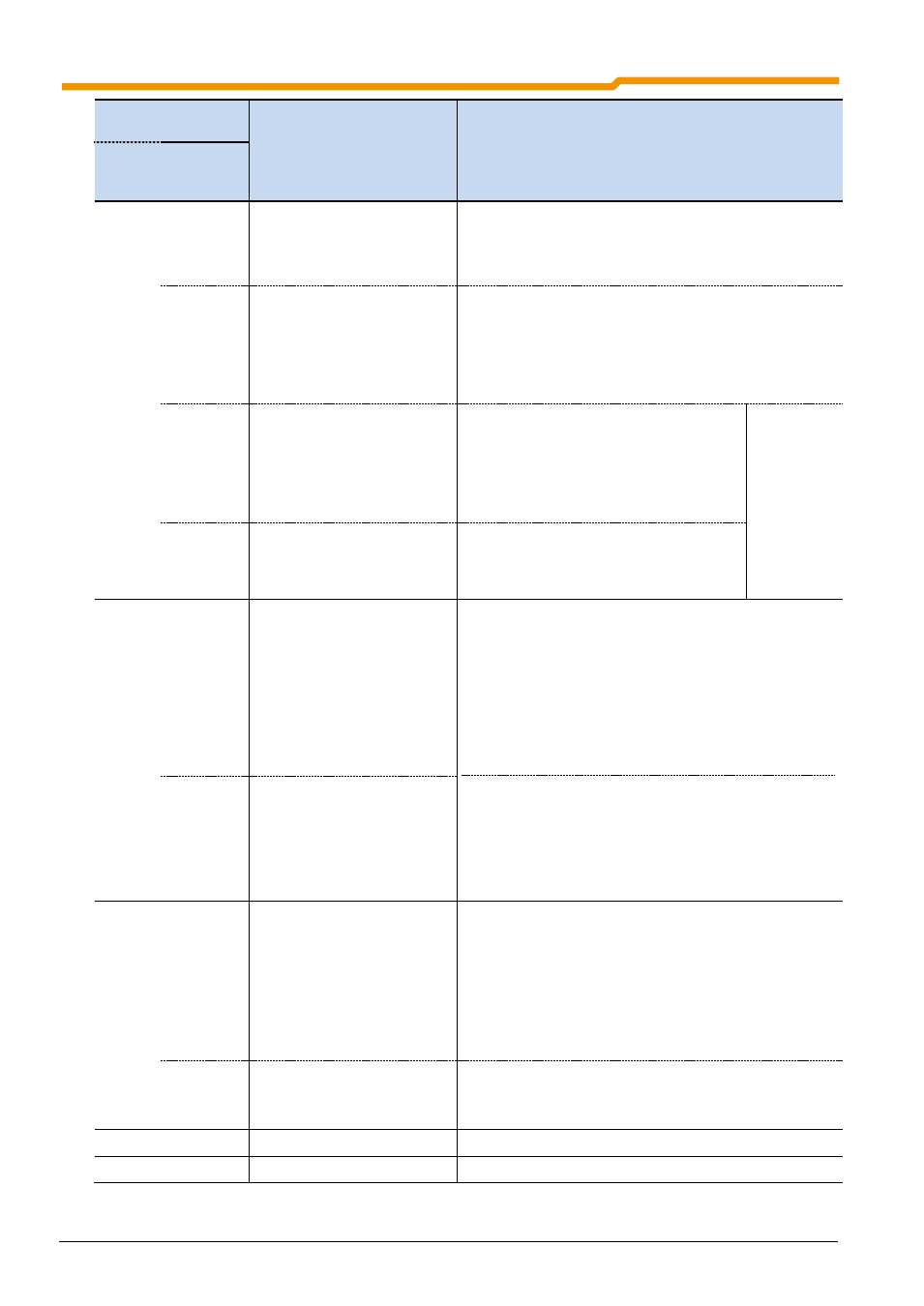
SK 180E Manual for frequency inverters
142
Pre-series version
BU 0180 GB-0914
Display in the
SimpleBox
Fault
Text in the ParameterBox
Cause
Remedy
Group
Details in
P700[-01] /
P701
E003
3.0
I
2
t overcurrent limit
Rectifier I
2
t limit has triggered,
e.g. > 1,5 x I
n
for 60s
(Please also note P504)
Continuous overload at inverter output
3.1
Chopper overtemperature I
2
t
I
2
t limit for brake chopper triggered
(Only Size II)
(1.5 times the value has been reached for a period of 60s)
(please also note P555, P556, P557)
Avoid overcurrent in brake resistance
3.2
Overcurrent IGBT
monitoring 125%
De-rating (power reduction)
125% overcurrent for 50ms
Brake chopper current too high
for fan drives: enable flying start circuit
(P520)
See also
Section 9.4
3.3
Overcurrent IGBT
monitoring 150%
De-rating (power reduction)
150% overcurrent
Brake chopper current too high
E004
4.0
Overcurrent module
Error signal from module (short duration)
Short-circuit or earthing fault at FI output
Motor cable is too long
Use external output choke
Brake resistor faulty or resistance too low (Section 8)
The occurrence of this fault can cause a
considerable reduction of the service life, including
the destruction of the device.
4.1
Overcurrent current
measurement
"Overcurrent from overcurrent
measurement"
P537 (pulse current switch-off) was reached 3x within 50ms
(only possible if P112 and P536 are disabled)
FI is overloaded
(Drive unit sluggish, too small,
Ramps (P102/P103) to steep
→ Increase ramp time)
Check motor data (P201 … P209)
E005
5.0
Overvoltage DC link voltage
DC link voltage is too high
Reduce energy return by means of a braking resistance
(only size 2)
Extend deceleration time (P103)
If necessary, set switch-off mode (P108) with delay (not for
lifting equipment)
Extend emergency stop time (P426)
5.1
Mains overvoltage
Mains voltage is too high
Please check 380 V -
20% … 480 V +10%
or 200 … 240 V
10%
E006
---
Reserved
E007
---
Reserved