NORD Drivesystems BU0180 User Manual
Page 126
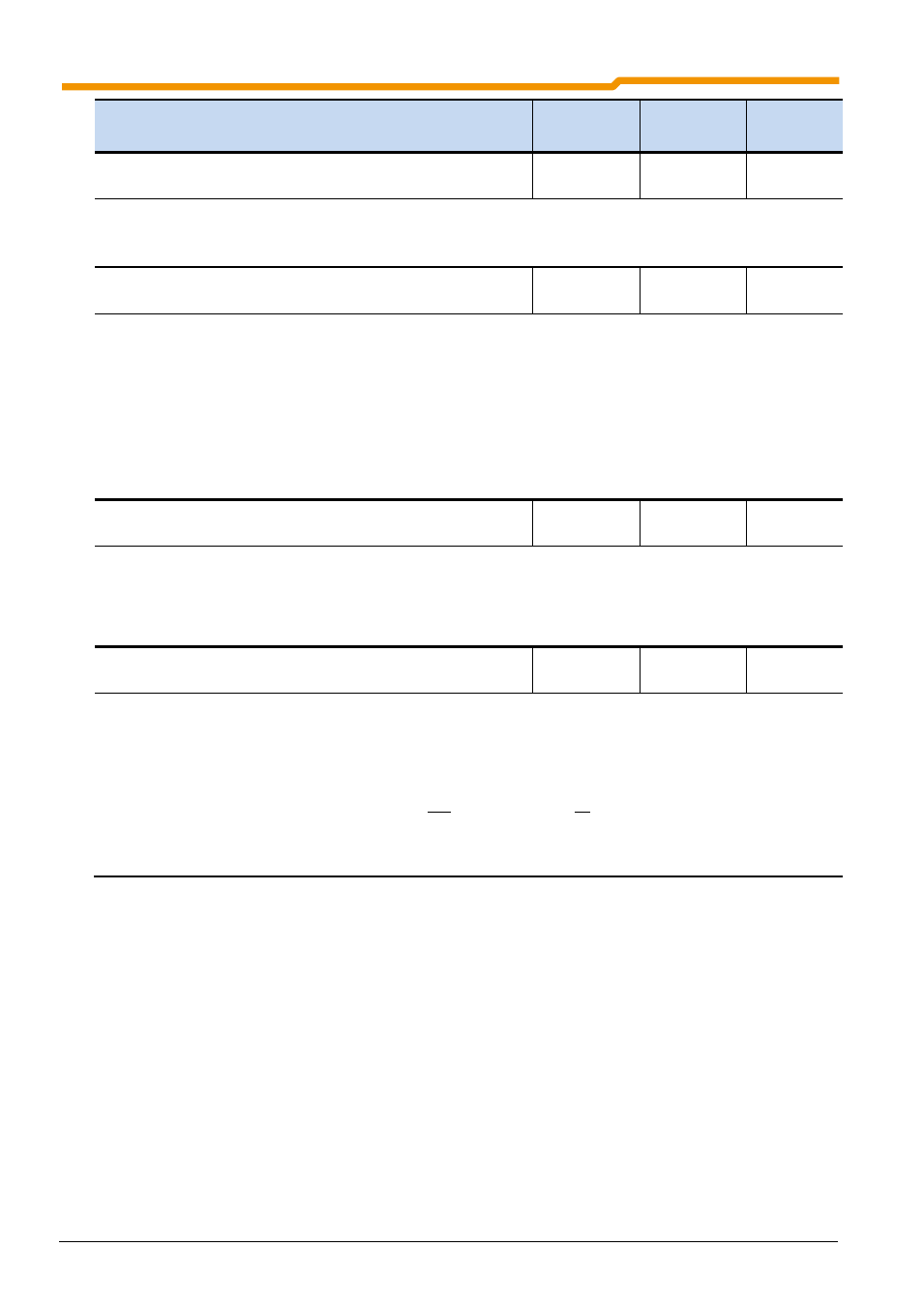
SK 180E Manual for frequency inverters
126
Pre-series version
BU 0180 GB-0914
Parameter
{Factory setting}
Setting value / Description / Note
Device
Supervisor
Parameter
set
P557
Brake resistor power
(Brake resistor power)
Only relevant
for size 2
S
0.00 ... 20.00 kW
{ 0.00 }
Continuous power (nominal power) of the resistor, to display the actual utilisation in P737. For a
correctly calculated value, the correct value must be entered into P556 and P557.
0.00 = Off, monitoring disabled
P558
Magnetisation time
(Magnetisation time)
S
P
0 / 1 / 2 ... 500 ms
{ 1 }
The ISD control can only function correctly if there is a magnetic field in the motor. For this
reason, a DC current is applied before starting the motor. The duration depends on the size of
the motor and is automatically set in the factory setting of the FI.
For time-critical applications, the magnetizing time can be set or deactivated.
0 =
Switched off
1 =
Automatic calculation
2 ... 500 = Time set in [ms]
NOTE: Setting values that are too low can reduce the dynamics and starting torque.
P559
DC run-on time
(DC run-on time)
S
P
0.00 ... 30.00 sec
{ 0.50 }
Following a stop signal and the braking ramp, a direct current is briefly applied to the motor to
fully bring the drive to a stop. Depending on the inertia, the time for which the current is applied
can be set in this parameter.
The current level depends on the previous braking procedure (current vector control) or the
static boost (linear characteristic).
P560
Param. saving mode
(Parameter saving mode)
S
0 ... 2
{ 1 }
0 = Only in RAM, changes to the parameter settings are no longer saved on the EEPROM.
All previously saved settings are retained, even if the FI is disconnected from the
mains.
1 = RAM and EEPROM, all parameter changes are automatically written to the EEPROM
and remain stored there even if the FI is disconnected from the mains supply.
2 = Off, no saving in RAM and EEPROM possible no parameter changes are accepted)
NOTE:
If BUS communication is used to implement parameter changes, it must be
ensured that the maximum number of write cycles to the (memory module)
EEPROM (100,000 x) is not exceeded.