2 control connection details – NORD Drivesystems BU0180 User Manual
Page 36
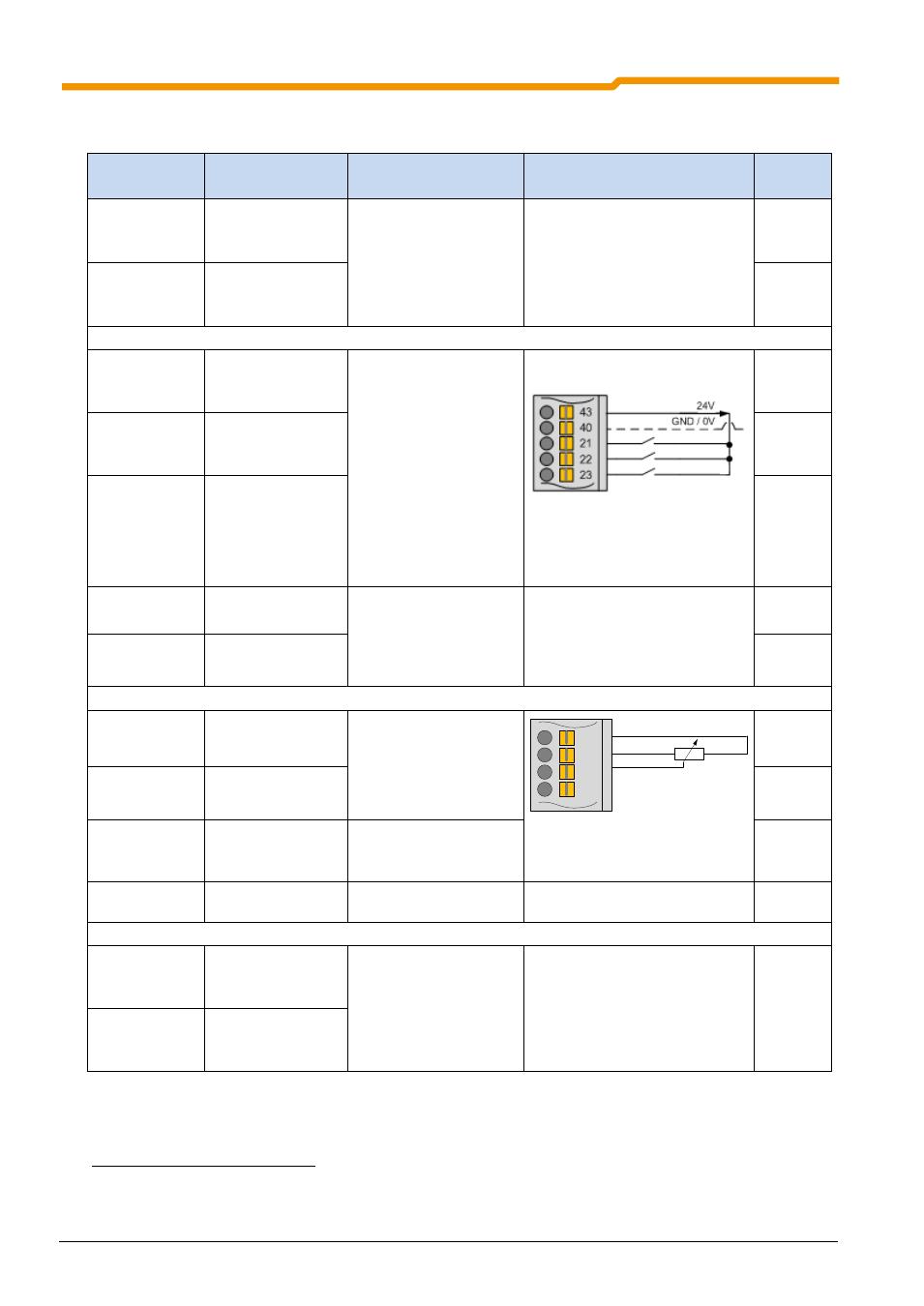
SK 180E Manual for frequency inverters
36
Pre-series version
BU 0180 GB-0914
2.8.2
Control connection details
The frequency inverter generates its own control voltage and provides this to Terminal 43.
Terminal/
Designation
Function
{Factory setting}
Data
Description / wiring suggestion
Parameter
43
VO/24V
24V supply
Output
24V DC ±25%
max. 150 mA
1
(output)
Voltage supply provided by the FI
for control of the digital inputs
-
40 GND / 0V
Reference potential
for digital signals
-
21
DIN1
Digital input 1
{ON right}
Digital input as per
EN 61131-2 Type 1
Low: 0
-5 V
(~ 9.5 k
Ω)
High: 15-30 V
(~ 2.5-3.5 k
Ω)
Input capacitance:
Input 1…3 = 10 nF
Scan time: 1 ms
Reaction time:
≥ 4 ms
Input 1 reacts slowly
Inputs 2 + 3 react quickly
P420 [01]
22
DIN2
Digital input 2
{ON left}
P420 [02]
23
DIN3
Digital input 3
{fixed frequency 1,
(P465[-01])}
P420 [03]
1
DOUT1
Output 1
{Fault}
Digital output
24V DC, max. 20 mA
For inductive loads:
provide protection with a
free-wheeling diode.
For evaluation in a control system.
P434 [01]
3
DOUT2
Output 2
{Fault}
P434 [02]
14
AIN1 +
Analog input 1
{Setpoint frequency}
U=0…10 V, R
i
=30
kΩ
Resolution 12Bit
I=0/4
…20 mA,
burden resistor (250
Ω)
via DIP switch S1 can be
switched to AIN1/2
11
12
14
16
R=10k
Matching of the analog signals is
performed via P402 and P403.
P400 [01]
16
AIN2 +
Analog input 2
{No function}
P400 [02]
12 AGND / 0V
Reference potential
for analog signals
0 V analog
11
10V REF
+10 V
Reference voltage
+10 V, 5 mA
38
TF+
PTC resistor input
-
For monitoring motor temperature
with PTC
A shielded cable must be used for
separate mounting of the motor
and the FI (note the cable length).
-
39
TF-
PTC resistor input
1
The current which is drawn from the digital outputs must also be covered by this. Any control modules which are
connected to the RJ12 socket also place a load on the 24V supply. (150mA = I
DIG1
+ I
DIG2
+ I
OUT
+ I
CONTROL
)