4 control terminals – NORD Drivesystems BU0180 User Manual
Page 92
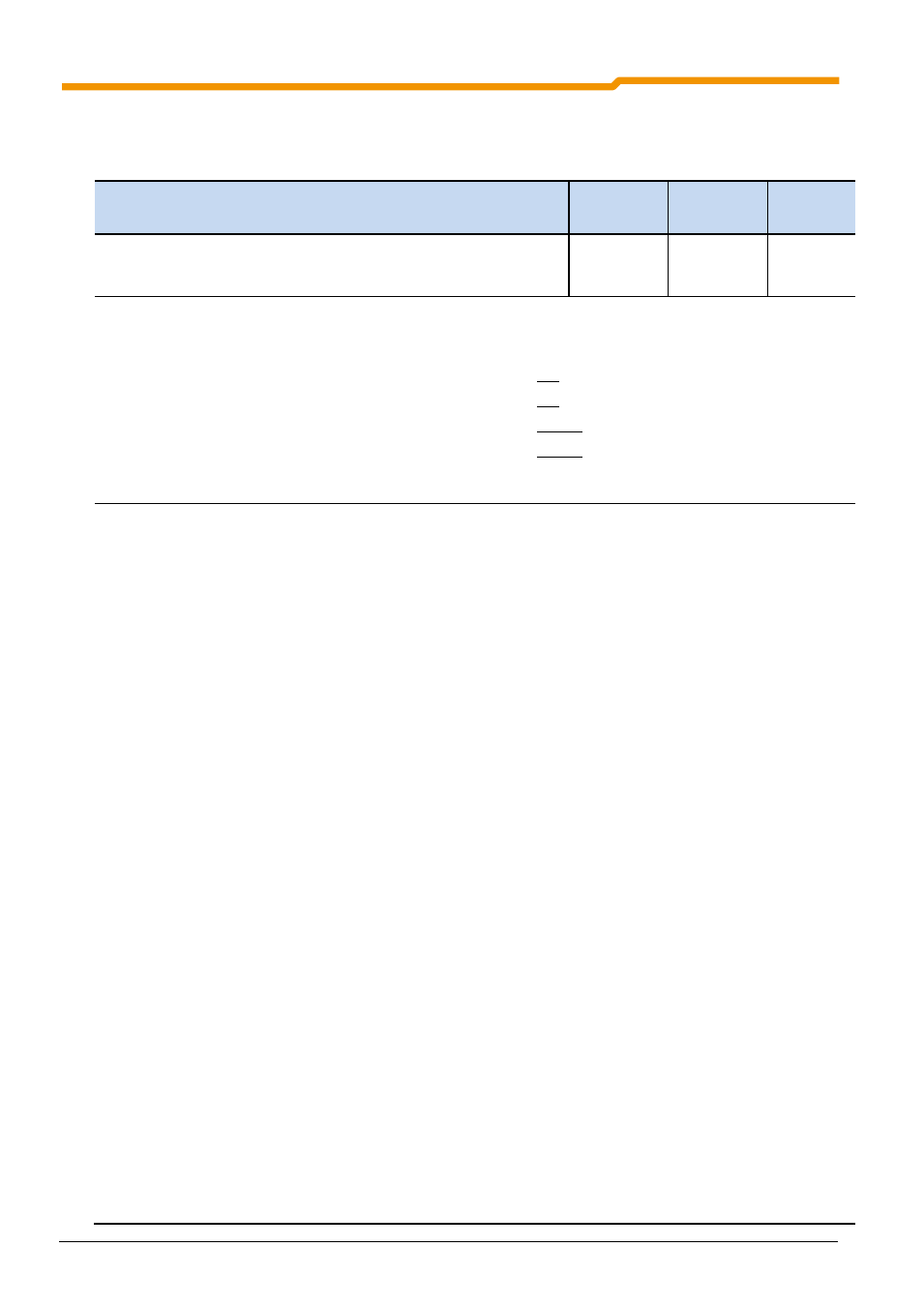
SK 180E Manual for frequency inverters
92
Pre-series version
BU 0180 GB-0914
6.1.4
Control terminals
Parameter
{Factory setting}
Setting value / Description / Note
Device
Supervisor
Parameter
set
P400
[-01]
...
[-07]
Fnct. setpoint inputs
(Function of setpoint inputs)
P
0 ... 36
{ [-01] = 1 }
{ [-02] = 0 }
{ [-03] = 0 }
{ [-04] = 0 }
{ [-05] = 0 }
{ [-06] = 0 }
{ [-07] = 0 }
[-01] = Analog input 1, Function of analog input 1 integrated into the FI
[-02] = Analog input 2, Function of analog input 2 integrated into the FI
[-03] = Ext. Analog input 1,
AIN1 of the first I/O extension (SK xU4-IOE)
[-04] = Ext. Analog input 2,
AIN2 of the first I/O extension (SK xU4-IOE)
[-05] = Ext.
A.in
1 2nd IOE,
AIN1 of the second I/O extension (SK xU4-IOE)
[-06] = Ext.
A.in
2 2nd IOE,
AIN2 of the second I/O extension (SK xU4-IOE)
[-07] = Setpoint module,
in preparation ... setting values below.
For standardisation of actual values: See also (Section 9.9 ).
0 = Off, the analog input has no function. After the FI has been enabled via the control
terminals, it will supply the set minimum frequency (P104).
1 = Setpoint frequency, the given analog range (P402/P403) varies the output frequency
between the set minimum and maximum frequencies (P104/P105).
2 = Frequency addition **, the supplied frequency value is added to the setpoint.
3 = Frequency subtraction **, the supplied frequency value is subtracted from the setpoint.
4 = Minimum frequency, setting of the minimum frequency of the inverter
(= 0
– 100% from P104)
5 = Maximum frequency, setting of the maximum frequency of the inverter
(= 0
– 100% from P105)
6 = Actual value process controller *, activates the process controller, analog input is
connected to the actual value encoder (compensator, air can, flow volume meter, etc.).
The mode is set via the DIP switches of the I/O extension or in (P401).
7 = Setpoint process controller *, as for Function 14, however, the setpoint is specified (e.g.
by a potentiometer). The actual value must be specified using another input.
8 = Actual PI frequency *, is required to set up a control loop. The analog input (actual value)
is compared with the setpoint (e.g. fixed frequency). The output frequency is adjusted as
far as possible until the actual value equals the setpoint. (see control variables
P413...P414)
9 = Actual freq. PI limited *,
"Actual frequency PI limited“, as for function 8 "Actual frequency
PI", however the output frequency cannot fall below the programmed minimum frequency
value in Parameter P104. (no change to rotation direction)
10 = Actual freq. PID monitored *, "Actual frequency PID monitored", as for function 8 Actual
frequency PI", however the FI switches the output frequency off when the minimum
frequency P104 is reached
11 = Torque current limit, "Torque current limited" depends on parameter (P112). This value
corresponds to 100% of the setpoint value. When the set limit value is reached, there is a
reduction of the output frequency at the torque current limit.
12 = Torque current limit switch-off, "Torque current limit switch-off" depends on parameter
(P112). This value corresponds to 100% of the setpoint value. When the set limit value is
reached, the device switches off with error code E12.3.
13 = Current limit, "Current limited" depends on parameter (P536). This value corresponds to
100% of the setpoint value. When the set limit value is reached, the output voltage is
reduced in order to limit the output current.
14 = Current switch-off, "Current limit switch-off", depends on parameter (P536), this value
corresponds to 100% of the setpoint value. When the set limit value is reached, the
device switches off with error code E12.4.
15 = Ramp time, "Ramp time" is normally only used in combination with a potentiometer.
Standardisation: T_Ramp time= 10s * U[V] / 10V (U=Potentiometer voltage).