NORD Drivesystems BU0180 User Manual
Page 101
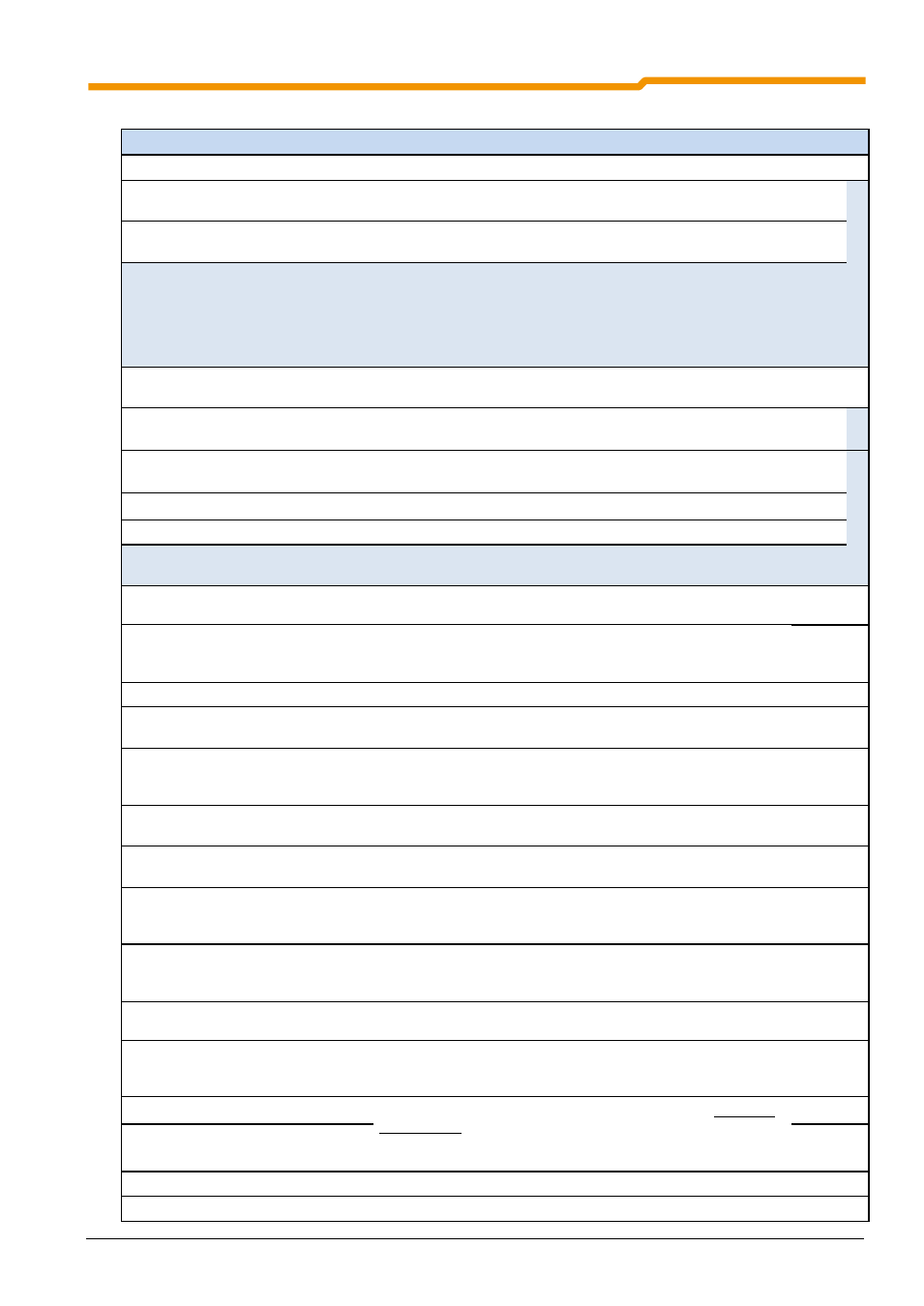
6 Parameterisation
BU 0180 GB-0914
Pre-series version
101
List of the possible functions of the digital inputs P420 [01]... [-04]
Value Function
Description
Signal
00
No function
Input switched off.
---
01
Enable right
The FI delivers an output signal with the rotation field right if a
positive setpoint is present: 0 → 1 Flank (P428 = 0)
High
02
Enable left
The FI delivers an output signal with the rotation field left if a
positive setpoint is present: 0 → 1 Flank (P428 = 0)
High
If the drive is to start up automatically when the mains is switched on (P428 = 1) a permanent High level for
enabling must be provided (supply terminal 21 with 24V).
If the functions "Enable right" and "Enable left" are actuated simultaneously, the FI is blocked.
If the frequency inverter is in fault status but the cause of the fault no longer exists, the error message is
acknowledged with a 1
→ 0 flank.
03
Change of rotation direction
Causes the rotation field to change direction in combination with
Enable right or left.
High
04
1
Fixed frequency 1
The frequency from P465 [01] is added to the actual setpoint
value.
High
05
1
Fixed frequency 2
The frequency from P465 [02] is added to the actual setpoint
value.
High
06
1
Fixed frequency 3
The frequency from P465 [03] is added to the actual setpoint value.
High
07
1
Fixed frequency 4
The frequency from P465 [04] is added to the actual setpoint value.
High
If several fixed frequencies are actuated at the same time, then they are added with the correct sign. In
addition, the analog setpoint (P400) and possibly the minimum frequency (P104) are added.
08
Param set switching
"Parameter set switchover 1"
Selection of the active parameter set 1…4 (P100)
High
09
Hold frequency
During the acceleration or deceleration phase, a Low level will
cause the actual output frequency to be "held". A High level
allows the ramp to proceed.
Low
10
2
Disable voltage
The FI output voltage is switched off; the motor runs down freely.
Low
11
2
Emergency stop
The FI reduces the frequency according to the programmed fast
stop time P426.
Low
12
2
Fault acknowledgement
Fault acknowledgement with an external signal. If this function is
not programmed, a fault can also be acknowledged by a low
enable setting (P506).
0
1
Flank
13
2
PTC resistor input
Only with the use of a temperature monitor (bimetal switching
contact). Switch-off delay = 2 sec, warning after 1 sec.
High
14
2, 3
Remote control
With bus system control, Low level switches the control unit to
control via the control terminals.
High
15
Jog frequency
1
The fixed frequency value can be adjusted using the
HIGHER/LOWER and OK keys (P113), if control is via the
SimpleBox or ParameterBox.
High
16
Motor potentiometer
As in setting 09, however, the frequency is not maintained below
the minimum frequency P104 and above the maximum frequency
P105.
Low
17
ParaSetSwitching
2
"Parameter set switchover 2"
Selec
tion of the active parameter set 1…4 (P100)
High
18
2
Watchdog
Input must see a High flank cyclically (P460), otherwise error
E012 will cause a shutdown. Function starts with the 1st high
flank.
0
1
Flank
19
Setpoint 1 on/off
Analog input switch-on and switch-off 1/2 (high = ON) of the first
I/O extension. The Low signal sets the analog input to 0% which
does not lead to shutdown when the minimum frequency (P104)
> than the absolute minimum frequency (P505).
High
20
Setpoint 2 on/off
High
21
... 28 reserved
29
Enable SetpointBox
-