Modbus - using programmable memory blocks, Cip - communications capabilities – Watlow EZ-ZONE PM Integrated Controller User Manual
Page 145
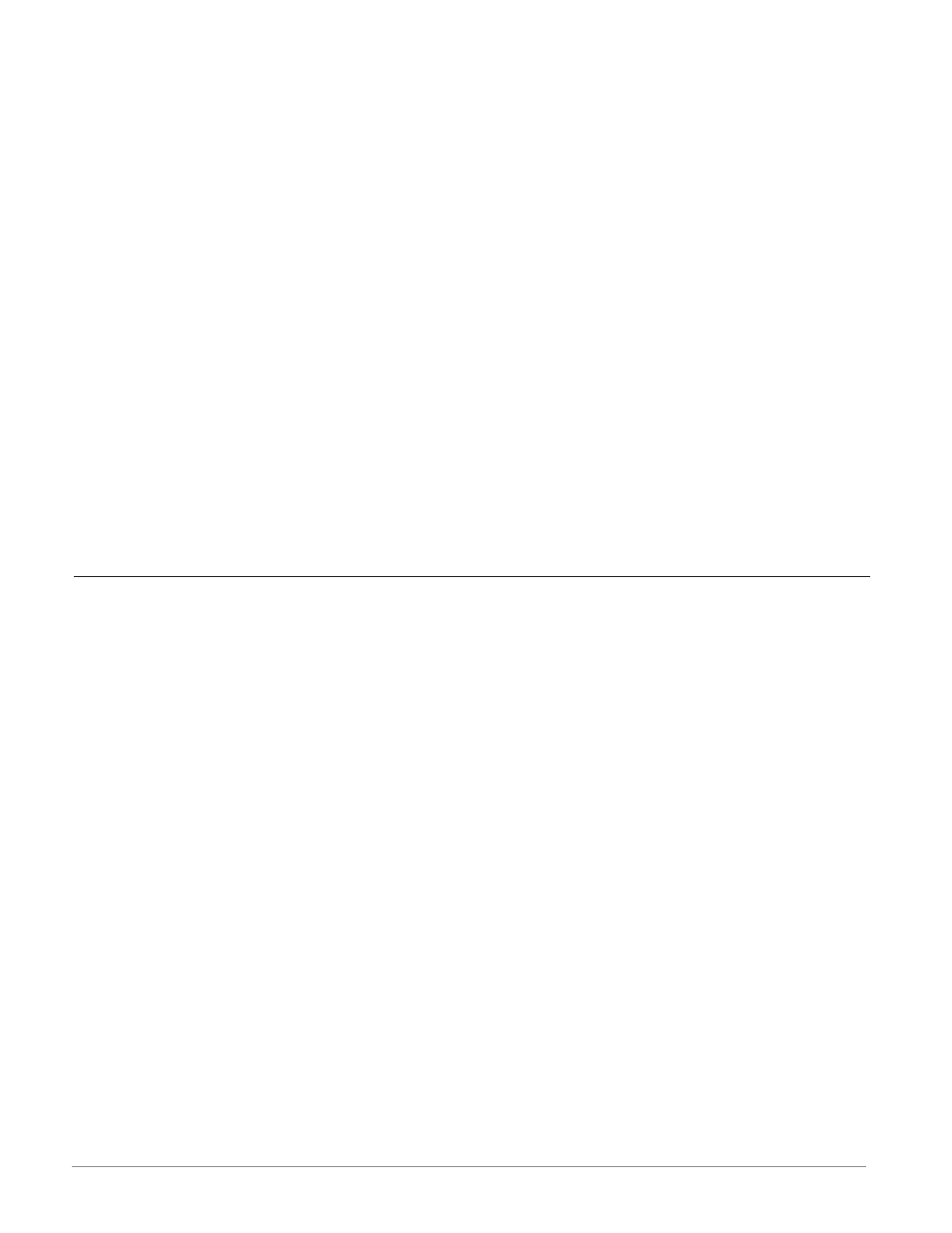
Watlow EZ-ZONE
®
PM Integrated Controller
•
142
•
Chapter 9 Features
Modbus - Using Programmable Memory Blocks
When using the Modbus RTU or Modbus TCP protocols, the PM control features a block of addresses that
can be configured by the user to provide direct access to a list of 40 user configured parameters. This allows
the user easy access to this customized list by reading from or writing to a contiguous block of registers.
To acquire a better understanding of the tables found in the back of this manual (
See Appendix:
(
) please read through the text below which defines the column headers used.
Assembly Definition Addresses
- Fixed addresses used to define the parameter that will be stored in the "Working Addresses", which may
also be referred to as a pointer. The value stored in these addresses will reflect (point to) the Modbus ad-
dress of a parameter within the ST control.
Assembly Working Addresses
- Fixed addresses directly related to their associated "Assembly Definition Addresses" (i.e., Assembly
Working Addresses 200 & 201 will assume the parameter pointed to by Assembly Definition Addresses
40 & 41).
When the Modbus address of a target parameter is stored in an "Assembly Definition Address" its corre-
sponding working address will return that parameter’s actual value. If it’s a writable parameter, writing to
its working register will change the parameter’s actual value. As an example, Modbus register 360 repre-
sents the Analog Input 1 Process Value (See Operations Page, Analog Input Menu). If the value 360 is loaded
into Assembly Definition Address 90 and value 361 is loaded into Assembly Definition Address 91, the pro-
cess value sensed by analog input 1 will also be stored in Modbus registers 250 and 251. Notice that by de-
fault this parameter is also stored in working registers 240 and 241 as well.
Note:
When modifying the Modbus Assembly registers, single register writes (function 06) are not allowed. Mul-
tiple register writes (function 16) must be used to modify the assembly.
The table identified as "Assembly Definition Addresses and Assembly Working Addresses" (see Appendix:
Modbus Programmable Memory Blocks) reflects the assemblies and their associated addresses.
CIP - Communications Capabilities
With the introduction of CIP a user can now collect data, configure a device and control industrial devices.
CIP is an open protocol at the application layer fully managed by the Open DeviceNet Vendors Association
). Being that this is an open protocol there are many independent vendors offer-
ing a wide array of devices to the end user. CIP provides the ability to communicate utilizing both implicit
messaging (real-time I/O messaging), and explicit messaging (information/configuration messaging). For im-
plicit communications using a PLC, simply configure the PM assembly size into the I/O structure of the PLC
CIP Implicit Assemblie Structures
). The assembly structures can also be changed by the user. Explicit
communications requires the use of specific addressing information. DeviceNet requires that the node ad-
dress be specified where EtherNet/IP requires just the Class, Instance and Attribute.
• Node address or MAC ID (0 - 63, DeviceNet only)
• Class ID (1 to 255)
• Instance ID (0 to 255)
• Attribute ID (1 to 255)
EtherNet/IP and DeviceNet are both based on CIP and use the same addressing scheme. In the following
menu pages notice the column header identified as CIP. There you will find the Class, Instance and Attri-
bute in hexadecimal, (decimal in parenthesis) which makes up the addressing for both protocols. The Watlow
implementation of CIP does not support connected explicit messages but fully supports unconnected explicit
messaging.
Rockwell Automation (RA) developed the DF1 serial protocol within the framework of the PCCC applica-
tion protocol. With the introduction of CIP, the PCCC protocol was encapsulated within it to enable continued
communication over Ethernet to the legacy RA programmable controllers, e.g., SLC, Micrologic and PLC-5
controllers equipped with Ethernet capabilities. The Watlow implementation of CIP also supports the PCCC
protocol.
EtherNet/IP (Industrial Protocol) is a network communication standard capable of handling large
amounts of data at speeds of 10 Mbps or 100 Mbps, and at up to 1,500 bytes per packet. It makes use of stan-
dard off-the-shelf Ethernet chip sets and the currently installed physical media (hardware connections). De-
viceNet was the first field bus offering of the ODVA group and has been around for many years. DeviceNet
can communicate at 125, 250 and 500 kilobytes per second with a maximum limitation of 64 nodes (0 to 63)
on the network.