No-arc relay, Retransmitting a process value or set point, Retransmit – Watlow EZ-ZONE PM Integrated Controller User Manual
Page 132
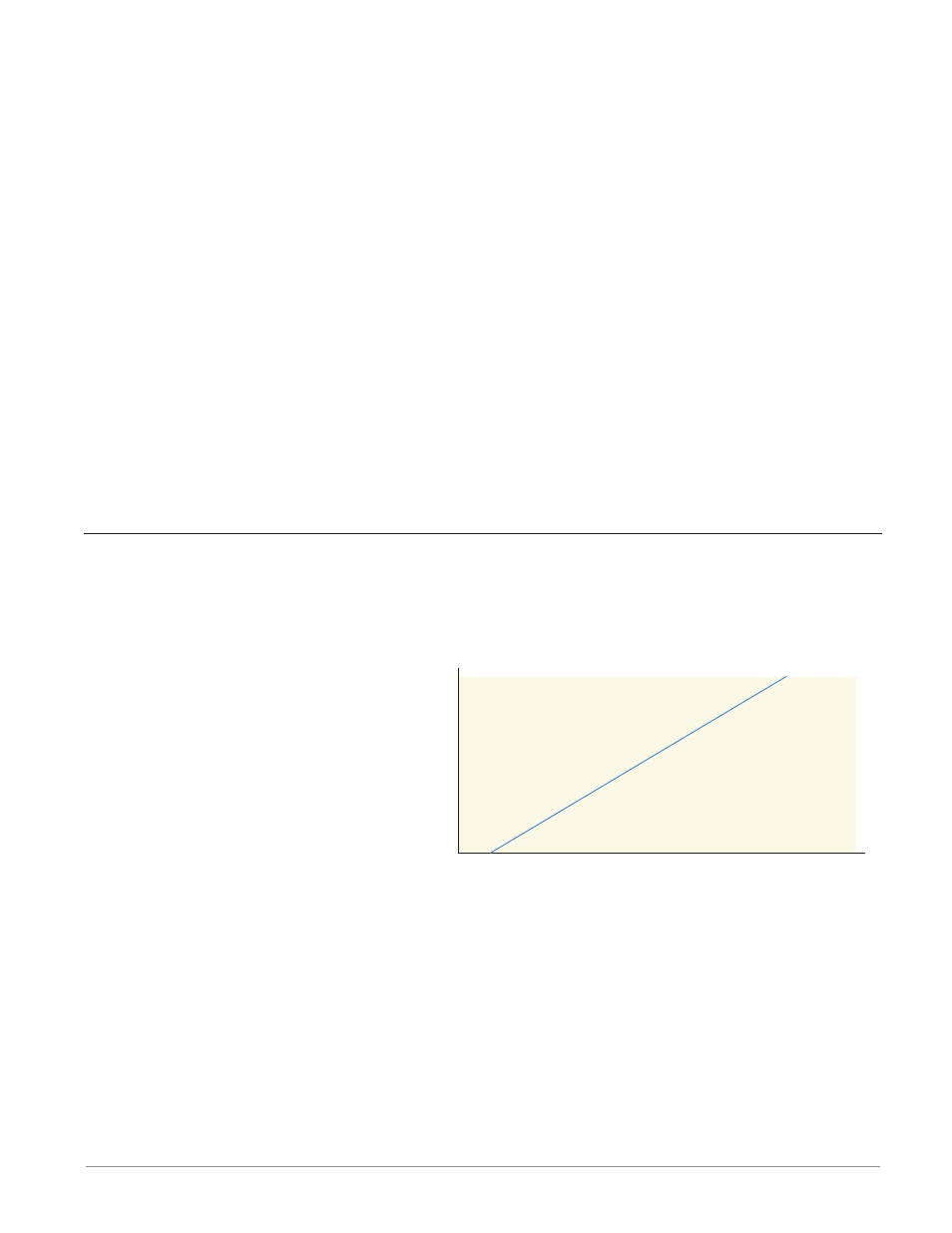
Watlow EZ-ZONE
®
PM Integrated Controller
•
129
•
Chapter 9 Features
NO-ARC Relay
A NO-ARC relay provides a significant improvement in the life of the output relay over conventional relays.
Conventional mechanical relays have an expected life of 100,000 cycles at the rated full-load current. The
shorter life for conventional relays is due to the fact that when contacts open while current is flowing metal
degradation occurs. This action produces unavoidable electrical arcing causing metal to transfer from one
contact to the other. The arcing conditions continue on each subsequent contact opening until over time the
resistance through the contacts increases causing the contacts to increase in temperature. Eventually, the
contacts will weld together and the relay remains in the on state.
The Watlow NO-ARC relay is a hybrid relay. It uses a mechanical relay for the current load and a triac
(solid-state switch) to carry the turn-on and turn-off currents. NO-ARC relays extend the life of the relay
more than two million cycles at the rated full-load current.
Although a NO-ARC relay has significant life advantages, a few precautions must be followed for accept-
able usage:
Do not use:
• hybrid relays for limit contactors. A limit or safety device must provide a positive mechanical break on all
hot legs simultaneously;
• dc loads with hybrid relays. The triacs used for arc suppression will turn off only with ac line voltage;
• hybrid switches to drive any inductive loads, such as relay coils, transformers or solenoids;
• cycle times less than five seconds on hybrid switches;
• on loads that exceed 264V ac through relay;
• on loads that exceed 15 amperes load;
• on loads less than 100 mA;
• NO-ARC relays in series with other NO-ARC relays.
Retransmitting a Process Value or Set Point
The retransmit feature allows a process output to provide an analog signal that represents the set point or
process value. The signal may serve as a remote set point for another controller or as an input for a chart re-
corder documenting system performance over time.
In choosing the type of retransmit signal the operator must take into account the input impedance of the
device to be retransmitted to and the re-
quired signal type, either voltage or mil-
liamps.
Typically applications might use the
retransmit option to record one of the
variables with a chart recorder or to gen-
erate a set point for other controls in a
multi-zone application.
Outputs 1 and 3 can be ordered as pro-
cess outputs. Select retransmit [rMt] as
the Output Function [``Fn] (Setup Page,
Output Menu). Set the output to volts
[uoLt]
or milliamps [`MA] with Output
Type [`o;ty]. Select the signal to retrans-
mit with Retransmit Source [`r;Sr].
Set the range of the process output
with Scale Low [`S;Lo] and Scale High [`S;hi]. Scale the retransmit source to the process output with Range
Low [`r;Lo] and Range High [`r;hi].
When the retransmit source is at the Range Low value, the retransmit output will be at its Scale Low val-
ue. When the retransmit source is at the Range High value, the retransmit output will be at its Scale High
value.
Retransmit
Retransmit Source
Output Scale
Range High
Range Low
Scale High
Scale Low