IAI America XSEL-KET User Manual
Page 394
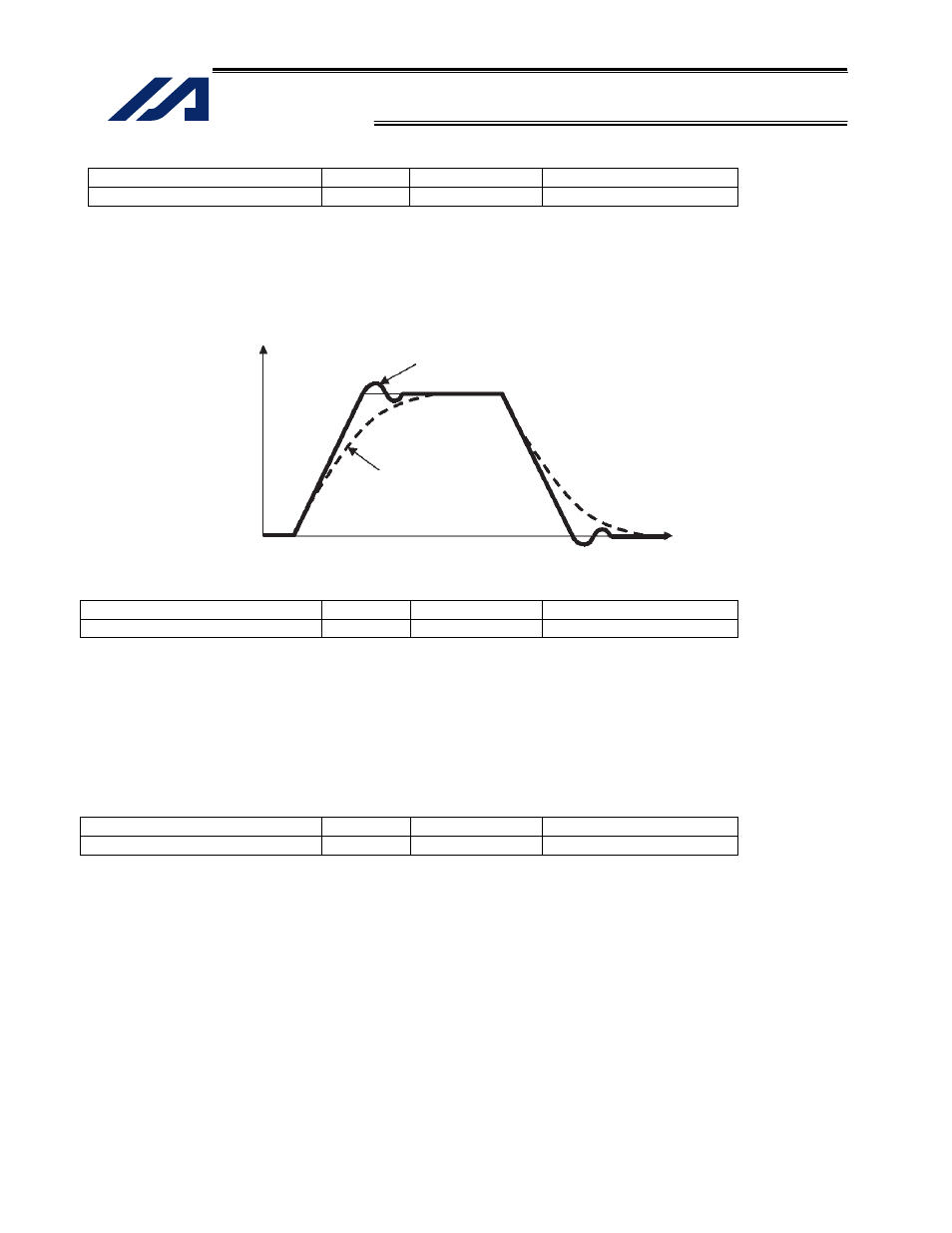
375
INTELLIGENT ACTUATOR
Speed-loop integral time constant
Driver card parameter number
Unit
Input range
Default value (reference)
39
-
0 to 1000
30
This parameter determines the response of the speed control loop.
Increasing the set value lowers the response to the speed command and reduces the reactive force to load
change. Also, conformance to the position command drops and positioning takes a longer time.
An excessively low setting may trigger overshooting or oscillation and cause the mechanical parts to vibrate
easily.
Current-loop control band number
Driver card parameter number
Unit
Input range
Default value (reference)
40
-
0 to 4
4
This parameter sets the control band for the PI current control system.
Normally the default setting need not be changed.
If this parameter is changed carelessly, safety of the control system may be compromised and a very dangerous
situation may occur.
If the actuator generates resonance noise, etc., however, changing this parameter will help reduce the
resonance noise.
Consult IAI if you wish to change this parameter.
Torque filter time constant (Parameter list 1)
Driver card parameter number
Unit
Input range
Default value (reference)
42
-
0 to 2500
0
This parameter determines the filter time constant for the torque command.
The motor will vibrate if the resonance frequency of the machine is equal to or below the response frequency of
the servo loop.
This mechanical resonance can be reduced by increasing the value set in this parameter.
However, safety of the control system may be compromised if the setting is increased excessively.
Speed
Set value is low (overshoot).
Set value is high.
Time