Pcon-ca/cfa, Power con – IAI America PCON-CA User Manual
Page 217
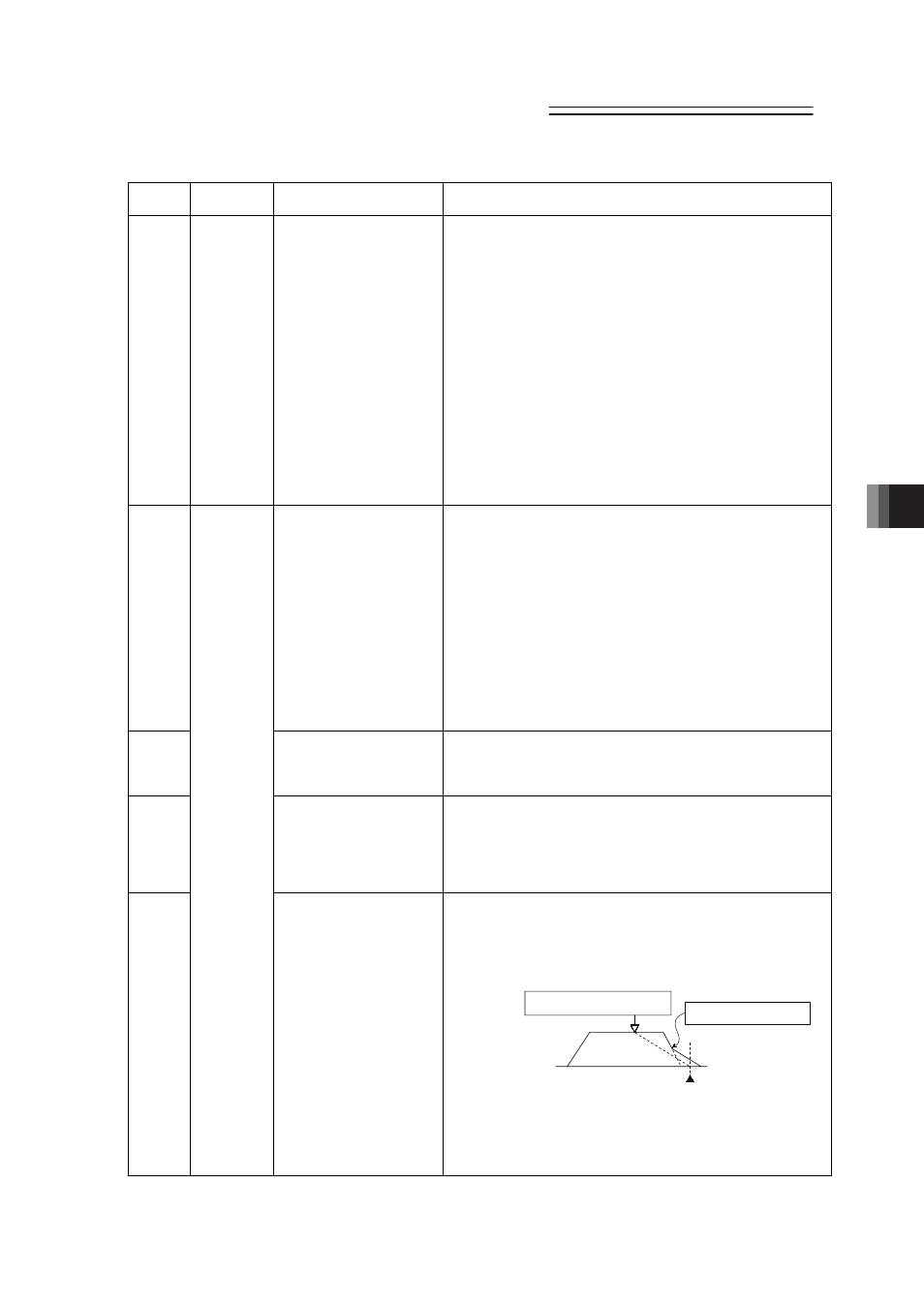
Chapter 8
Troubleshooting
POWER CON
PCON-CA/CFA
209
Alarm
Code Alarm Level
Alarm Name
Cause/Treatment
0A1
Cold start
Parameter data error
Cause
: The data input range in the parameter area is not
appropriate.
Example 1) This error occurs when the
magnitude relationship is apparently
inappropriate such as when 300mm
was incorrectly input as the value of
the soft limit negative side while the
value of the soft limit positive side
was 200.3mm.
Example 2) In rotary axis, when the index mode
is changed to the normal mode and
the soft limit negative side is 0, this
error is issued. Set the soft limit
negative side to a value -0.3mm is
added to the outer side of the
effective stroke. [Refer to 7.2 [2] Soft
limit +, Soft limit -]
Treatment : Change the value to the appropriate one.
0A2
Position data error
Cause
: 1) A move command was input when no target
position was set in the “Position” field of a
position No. in the position table.
2) The value of the target value in the “Position”
field exceeded the Parameter No.3 and 4
“Soft limit set value”.
3) A target position was specified in the
“Position” field by relative coordinate in the
solenoid valve mode 2 of PIO pattern 5.
Treatment : 1) Set the target position.
2) Change the target position value to the one
within the soft limit set value.
3) The target position cannot be set by relative
coordinate (incremental feed).
0A3
Position command data
error
Cause
: 1) The speed or acceleration/deceleration value
during direct numeric specification exceeded
the maximum set value.
Treatment : 1) Edit point table to input a proper value.
0A4
Command counter
overflow
Cause
: The number of input command pulses exceeded
the range of -134217728 to +134217728
(H'F8000000 to '07FFFFFF).
Treatment : Attempt to make the value of the electrical gear
ratio smaller (make the movement against the
unit bigger).
0A7
Operation
release
Command deceleration
error
Cause
: Because there is not enough deceleration
distance when the deceleration is changed to a
lower setting during the operation, the actuator
exceeded the soft limit when deceleration was
made from the current position with the
deceleration after the change.
Soft limit
Deceleration starting position
not resulting in soft limit overshoot
If a command is issued here,
soft limit overshoot will occur.
The cause is that the timing to make the next
movement command when the speed was
changed during the operation was late.
Treatment : Make the timing earlier for the movement
command for the deceleration speed change.