Pcon-ca/cfa, Power con – IAI America PCON-CA User Manual
Page 208
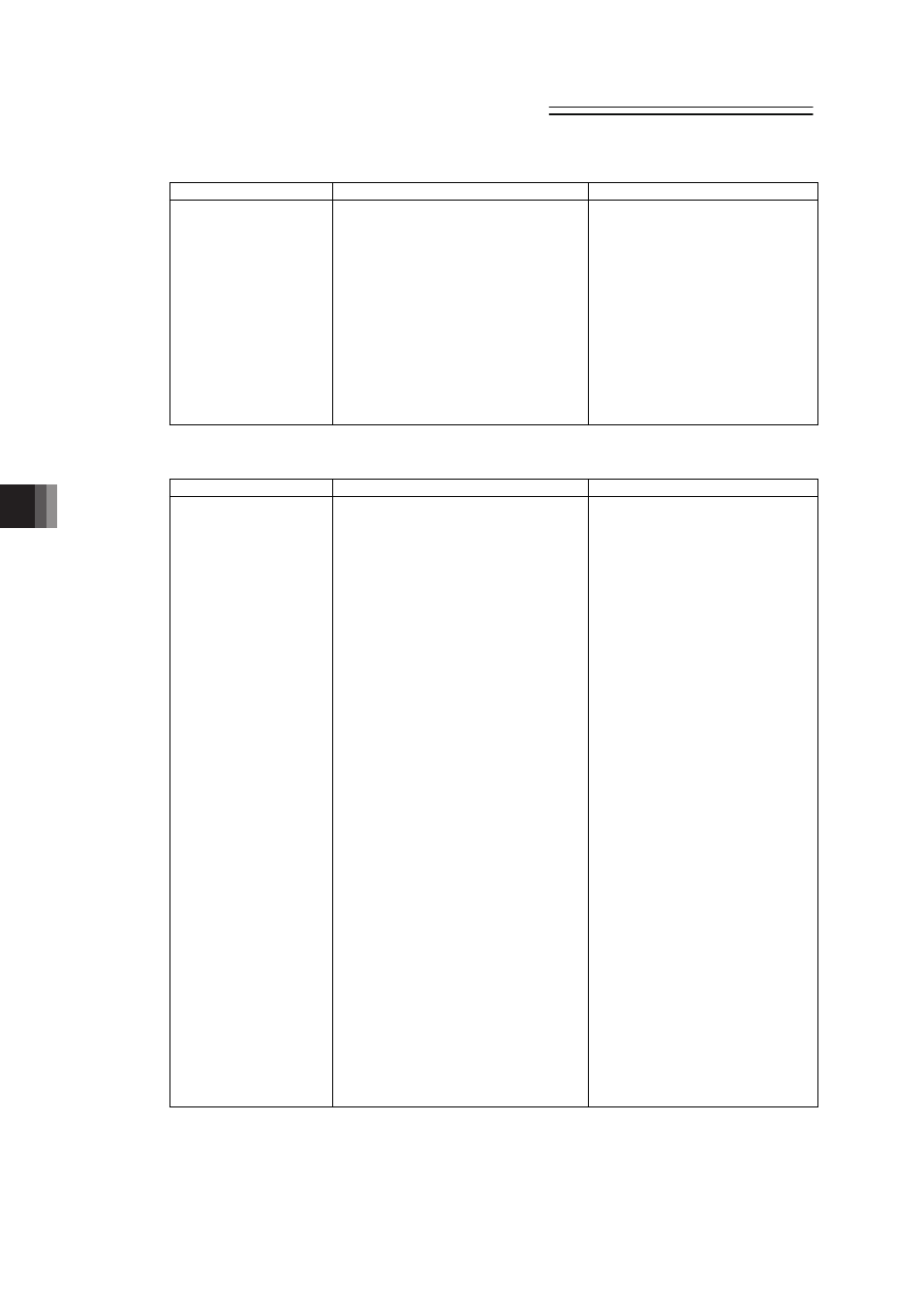
Chapter 8
Troubleshooting
POWER CON
PCON-CA/CFA
200
[In the case of Positioner Mode]
Situation
Possible cause
Check/Treatment
Both position No. and
start signal are input to
the controller, but the
actuator does not move.
There is a problem either in PIO signal
treatment, position table setting or
operation mode selection.
1) Servo OFF condition
2) The pause signal is OFF.
3) Positioning command is issued to a
stop position.
4) There is no positioning data set to
the commanded position number.
1) Is the status display LED SV
turned ON? [Refer to Name for
Each Parts and Their Functions]
Turn ON the servo-on signal
SON of PIO.
2) Operation is available when PIO
pause signal *STP is ON and
pause when it is OFF. Turn it
ON. [Refer to 2.1.2.]
3) Check the sequence or the
settings of the position table.
4) It will generate Alarm Code 0A2
“Position Data Error”. Conduct
the position table setting.
(Note) Refer to 2.1.3 [3] PIO Circuit for PIO signal.
[In the case of Pulse Train Control Mode]
Situation
Possible cause
Check/Treatment
In spite of inputting
pulse-train to the
controller, the actuator
does not move.
PIO signal processing or parameter
setting is incorrect.
1) Servo OFF state
2) The pause signal is OFF.
3) The pulse-train type, a parameter, is
selected incorrectly.
4) The positive/negative logic of
pulse-train, a parameter, is selected
inversely.
5) The unit moving distance per pulse,
which is a setting condition of
electronic gear ratio, a parameter, is
too small.
1) Is the status display LED SV
turned ON? [Refer to Name for
Each Parts and Their Functions]
Turn ON the servo-on signal
SON of PIO.
2) Operation is available when PIO
pause signal *STP is ON and
pause when it is OFF. Turn it
ON. [Refer to 2.1.2.]
3) Check the pulse train type.
[Refer to 3.3.4 [2] Format
Settings of Command Pulse
Train.]
4) Check the positive/negative
logic of pulse-train. (Host units
supplied by some manufacturers
have positive/negative logic
opposite to our logic. Reserve
the logic setting and try the
operation.)
[Refer to 3.3.4 [2] Format
Settings of Command Pulse
Train.]
5) Do not make the unit moving
distance less than the resolution
of the encoder. The actuator
does not move unless pulses by
the resolution of the encoder are
input.
[Refer to Caution in 3.3.4 [1]
Electrical Gear Setting]
(Note) In case of 3) or 4), the
actuator may not sometimes
operate smoothly.
You may not find case 5)
when the actuator is moved
for a long distance at a high
frequency.
(Note) Refer to 2.2.3 [3] PIO Circuit for PIO signal.