Side finishing (cycle g124), G124 side finishing (optional) – HEIDENHAIN TNC 410 ISO Programming User Manual
Page 300
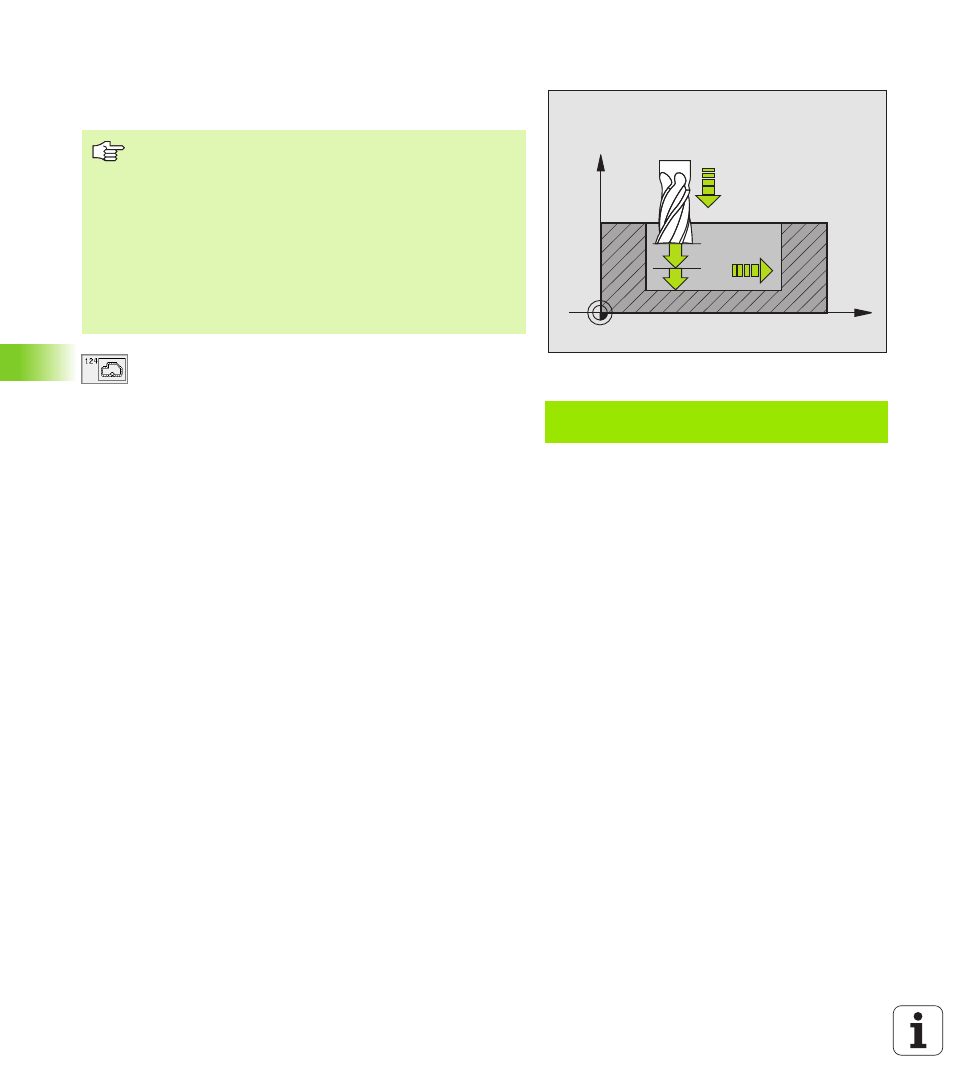
274
8 Programming: Cycles
8.7 SL Cy
cles Gr
ou
p II (no
t T
N
C
4
1
0)
SIDE FINISHING (Cycle G124)
The subcontours are approached and departed on a tangential arc.
Each subcontour is finish-milled separately.
U
U
U
U
Direction of rotation ? Clockwise = -1
Q9:
Machining direction:
+1: Counterclockwise
-1: Clockwise
U
U
U
U
Plunging depth
Q10 (incremental value): Dimension
by which the tool plunges in each infeed.
U
U
U
U
Feed rate for plunging
Q11: Traversing speed of the
tool during penetration.
U
U
U
U
Feed rate for milling
Q12: Traversing speed for
milling.
U
U
U
U
Finishing allowance for side
Q14 (incremental
value): Enter the allowed material for several finish-
milling operations. If you enter Q14 = 0, the remaining
finishing allowance will be cleared.
Example: NC block
N61 G124 Q9=+1 Q10=+5 Q11=100 Q12=350
Q14=+0 *
X
Z
Q11
Q12
Q10
Before programming, note the following:
The sum of allowance for side (Q14) and the radius of the
finish mill must be smaller than the sum of allowance for
side (Q3, Cycle G120) and the radius of the rough mill.
This calculation also holds if you run Cycle G124 without
having roughed out with Cycle G122; in this case, enter "0"
for the radius of the rough mill.
The TNC automatically calculates the starting point for
finishing. The starting point depends on the available
space in the pocket.