Rigid tapping new (cycle g207, not tnc 410) – HEIDENHAIN TNC 410 ISO Programming User Manual
Page 229
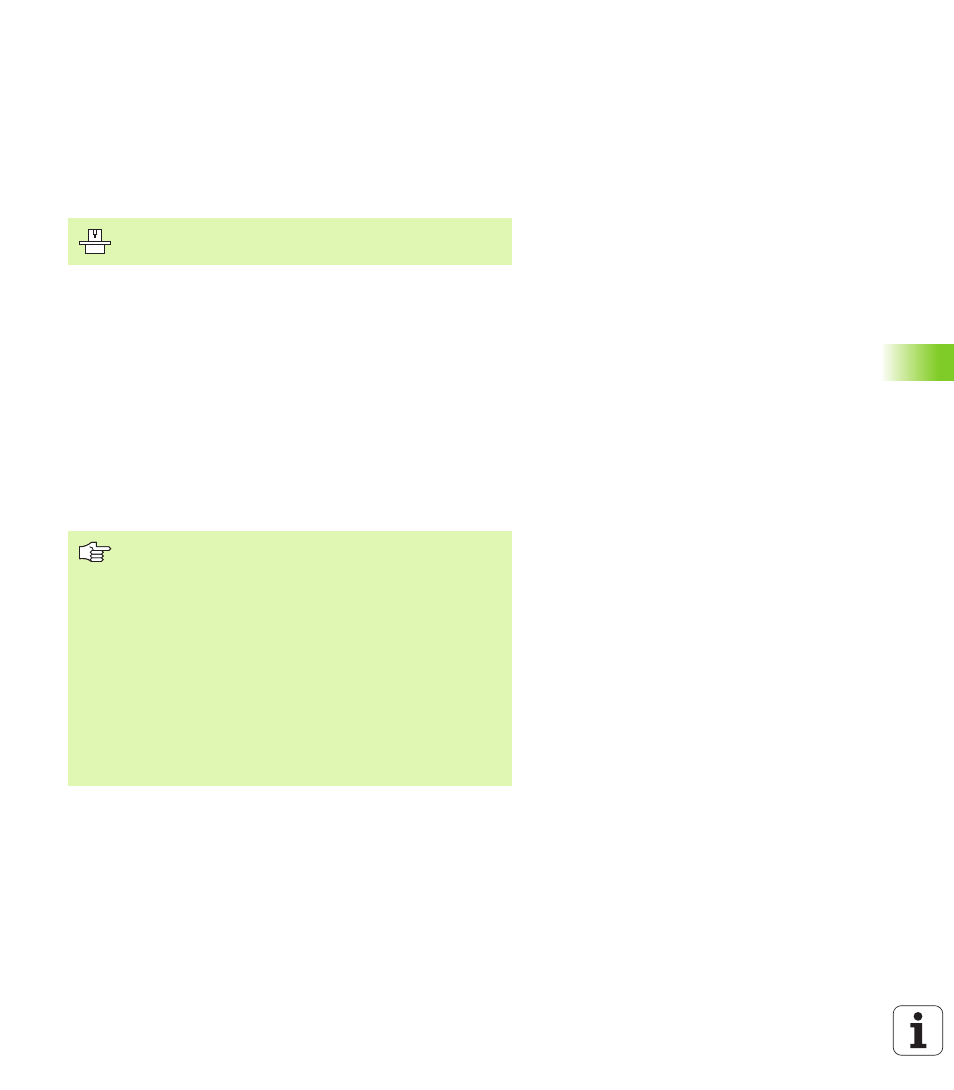
HEIDENHAIN TNC 410, TNC 426, TNC 430
203
8.3 Cy
cles f
o
r Dr
illing
, T
a
p
p
ing
and
Th
read Millin
g
Retract tool if program is interrupted (not TNC 410)
If you interrupt program run during tapping with the machine stop
button, the TNC will display the soft key MANUAL OPERATION. If you
press the MANUAL OPERATION key, you can retract the tool under
program control. Simply press the positive axis direction button of the
active tool axis.
RIGID TAPPING NEW (Cycle G207, not TNC 410)
The TNC cuts the thread without a floating tap holder in one or more
passes.
Rigid tapping offers the following advantages over tapping with a
floating tap holder: See “RIGID TAPPING (Cycle G85),” page 202.
1
The TNC positions the tool in the tool axis at rapid traverse to the
programmed setup clearance above the workpiece surface.
2
The tool drills to the total hole depth in one movement.
3
Once the tool has reached the total hole depth, the direction of
spindle rotation is reversed and the tool is retracted to the set-up
clearance at the end of the dwell time. If you have entered a 2nd
set-up clearance, the tool subsequently moves to that position in
rapid traverse.
4
The TNC stops the spindle turning at set-up clearance.
Machine and control must be specially prepared by the
machine tool builder for use of this cycle.
Before programming, note the following:
Program a positioning block for the starting point (hole
center) in the working plane with radius compensation
G40
.
The algebraic sign for the parameter total hole depth
determines the working direction.
The TNC calculates the feed rate from the spindle speed.
If the spindle speed override is used during tapping, the
feed rate is automatically adjusted.
The feed-rate override knob is disabled.
At the end of the cycle the spindle comes to a stop. Before
the next operation, restart the spindle with M3 (or M4).