Establishing mdc-360 control loop parameters, Stablishing, Mdc-360 c – INFICON MDC-360 Thin Film Deposition Controller User Manual
Page 91: Ontrol, Arameters
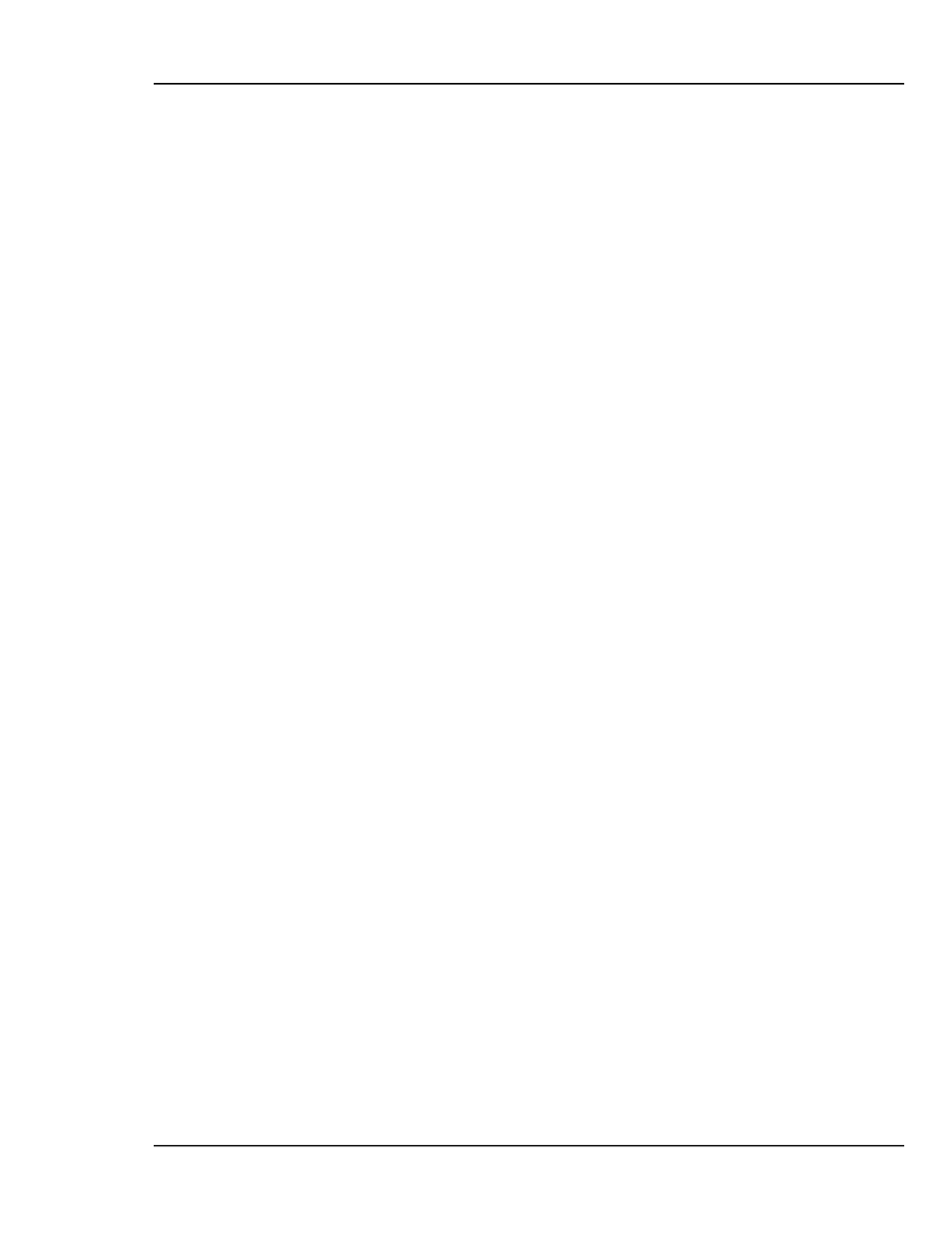
MDC-360 DEPOSITION CONTROLLER
6-3
Tuning the MDC-360 Control Loop
gone 48 miles because of some traffic earlier on. Our Integral error is 2 miles. If
we want to get back on schedule we need to speed up a bit. If schedule is very
important to us, we will speed up a lot to get back on schedule fast. If schedule is
not important at all we will maintain our speed. The Integral Time constant
instructs the controller on how much attention to pay to the schedule. If we don’t
care what happened in the past and we want zero rate error right now, we don’t
want any Integral feedback. To accomplish that we set the Integral Time constant
to its maximum value, which tells the controller to ignore any past error unless it
lasts for a very long.
6.3
ESTABLISHING MDC-360 CONTROL LOOP PARAMETERS
As explained above, the MDC utilizes three control loop parameters referred to as
PID parameters; Proportional gain, Integral Time constant and Derivative Time
constant to provide for optimization of the control loop. The MDC provides
default values for each of these parameters.
Default and Range for PID Parameters
Parameter
Minimum
value
Maximum
value
Default
value
Proportional gain
1
9999
1000
Integral time constant,
sec.
0
99.9
99.9
Derivative time constant
sec.
0 99.9
0.0