IAI America PCON-CF User Manual
Page 184
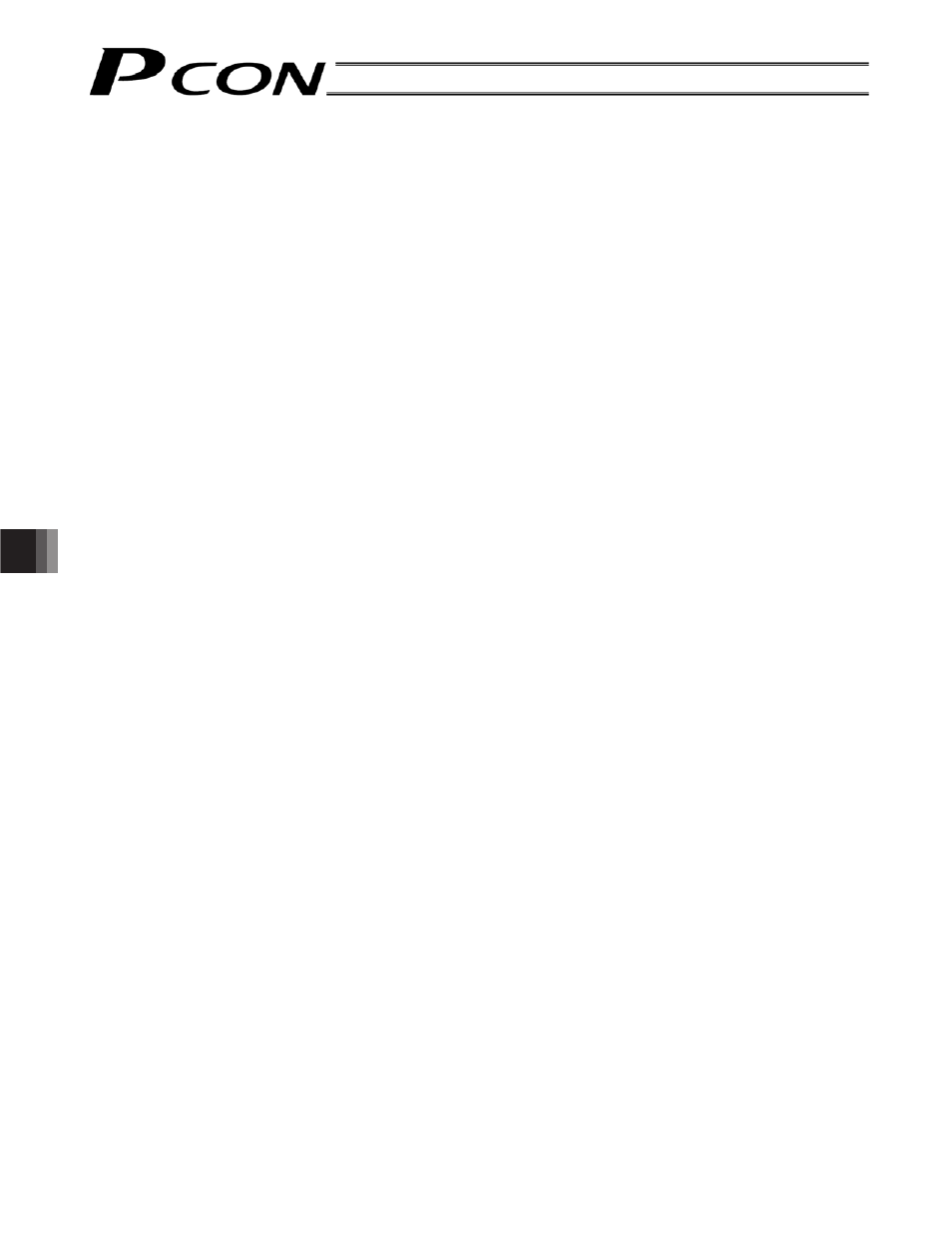
166
10. T
roubleshooting
z Home return ends in the middle in a vertical application.
Cause: [1] The load exceeds the rating.
[2] The ball screw is receiving torsional stress due to the affixing method of the actuator, tightening
of bolts only on one side, etc.
[3] The slide resistance of the actuator itself is large.
Action: [1] Increase the value set in parameter No. 13 (Current-limiting value during home return).
Increasing the parameter value will increase the home return torque. As a guide, however,
remember that the maximum limit is 100% for the RA3C/RGD3C types and 75% for all other
types.
[2] Loosen the fixing bolts and check if the slider moves smoothly.
If the slider moves smoothly, review the affixing method and bolt tightening condition.
[3] If the slide resistance of the actuator itself is large, please contact IAI.
z Noise occurs during downward movements in a vertical application.
Cause: The load exceeds the rating.
Action: [1] Decrease the speed.
[2] Decrease the value set in the parameter No. 7 (Servo gain number). Do not decrease the
parameter setting below “3.”
z Vibration occurs when the actuator is stopped.
Cause: The slider is receiving an external force.
Action: If the external force cannot be removed, increase the value set in parameter No. 12 (Current-limiting
value at standstill during positioning).
Increasing this value will cause the holding torque at standstill to increase, so do not increase the
parameter setting above 70%.
z The actuator overshoots when decelerated to a stop.
Cause: The load inertia is high due to an inappropriate balance of load and deceleration.
Action: Decrease the acceleration/deceleration setting.
z The home and target positions sometimes shift.
Cause: [1] The encoder waveform is disturbed by the effect of noise.
[2] In the case of a rod-type actuator, the non-rotation precision increased due to application of
rotating moment to the rod.
Action: [1] Check if the grounding is implemented correctly. Also check for any equipment being a potential
noise source.
[2] The actuator may have to be replaced in some cases. Please contact IAI.
z The speed is slow during push & hold operation.
Cause: The set current-limiting value is low with respect to the loading mass and slide resistance.
Action: Increase the current-limiting value for push & hold operation.
z The actuator moves only a half of, or twice as much as, the specified movement.
Cause: [1] The combination of controller and actuator is wrong.
The lead length of the ball screw varies depending on the actuator type, so a wrong combination
will cause the movement and speed to change.
[2] Factory setting error at IAI
Action: [1] If multiple actuators of different types must be used, confirm using the identification labels, etc.,
that the correct actuator is connected to the controller.
[2] Please contact IAI.