IAI America PCON-CF User Manual
Page 111
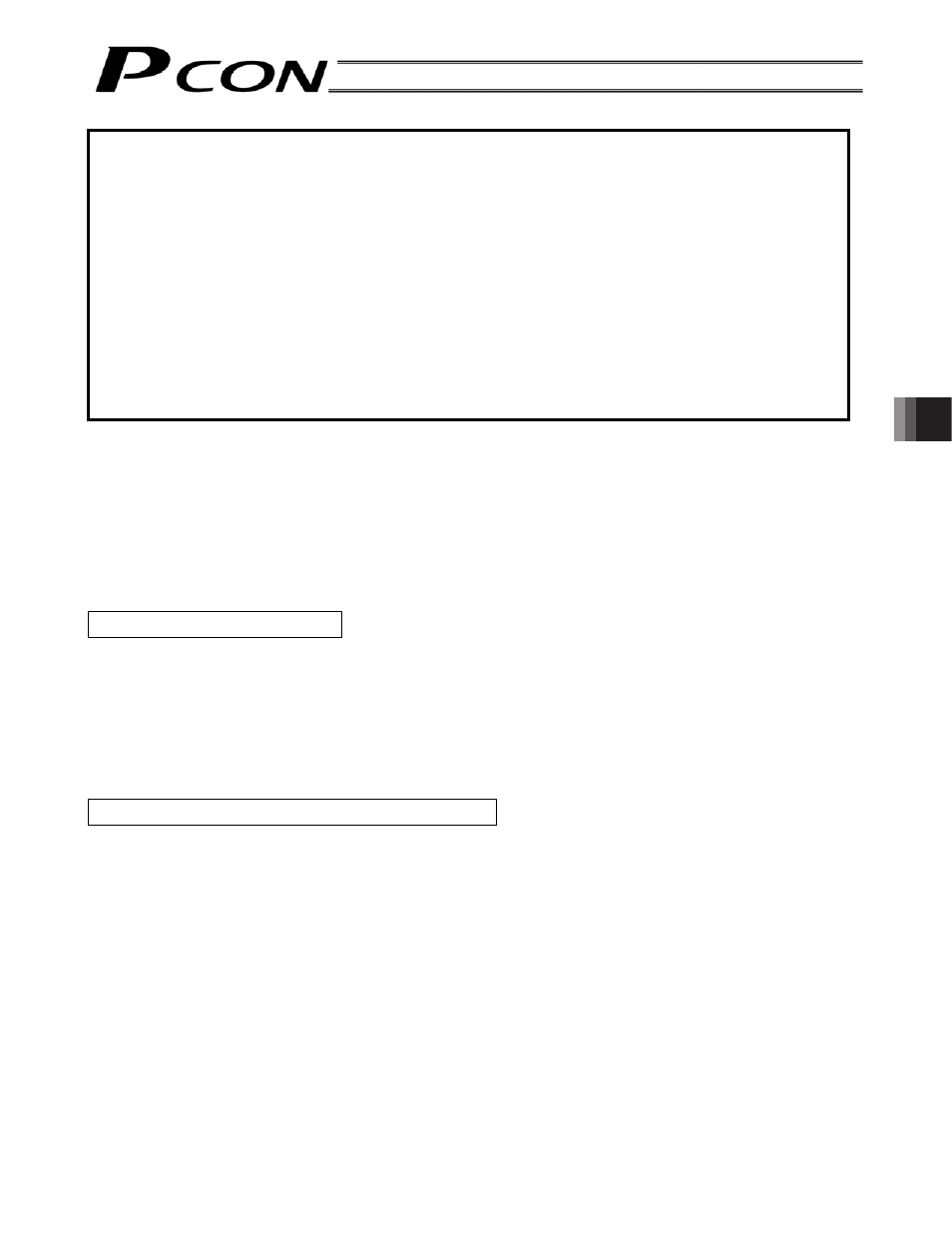
93
7. Operation
Warning: Since the drive motor uses a pulse motor, excited-phase detection is performed when the servo
is first turned on after the power on.
Therefore, the actuator must be able to move when the servo turns on.
If the slider or rod is contacting a mechanical end or the work part is contacting any surrounding
equipment, excited-phase detection will not be performed correctly and an abnormal operation
or excited-phase detection error may occur.
In this case, move the actuator by hand to a position where it can move before the servo turns
on.
If the actuator is equipped with a brake, the brake must be forcibly released by turning on the
brake release switch. The slider/rod may suddenly drop due to its dead weight when the brake is
released, so exercise caution not to pinch your hand or damage the robot hand or work part by
the falling slider/rod.
If the actuator cannot be moved by hand, one possible solution is to change the setting of
parameter No. 28 (Default direction of excited-phase signal detection). If you wish to change this
parameter, consult IAI beforehand.
7.1.2
Position Table and Parameter Settings Required for Operation
Startup adjustment
Immediately after the system has been started, the moving speed can be reduced by the methods specified
below to ensure safety of operators and prevent damage to jigs, etc.
Change the applicable parameters, if necessary.
o For details on the setting-change operations, refer to the operation manual for your PC software/teaching
pendant.
Safety speed during manual feed
To move the actuator using the PC/teaching pendant, set the mode selector switch on the front panel of the
controller to the “MANU” side.
For safety reasons, it is recommended that the actuator be moved at the safety speed during manual feed.
To do this, change the MANU operation mode to [Teaching mode: Enable safety speed] on the PC/teaching
pendant.
The safety speed is defined by parameter No. 35. Change the parameter value, if necessary.
Take note that the maximum speed is limited to 250 mm/s or below.
The factory setting is “100 mm/s” or below.
Speed override for movement commands from the PLC
You can lower the feed speed to be applied when the actuator is moved by the movement commands output
from the PLC.
To lower the speed to below the level set in the “Speed” field of the position table, you can use parameter No. 46
to override the “Speed” field.
Actual moving speed = [Speed set in the position table] x [Value of parameter No. 46]
y 100
Example) Value in the “Speed” field of the position table 500 (mm/s)
Value of parameter No. 46
20 (%)
Under the above settings, the actual moving speed becomes 100 mm/s.
The minimum setting unit is “1%,” while the input range is “1 to 100 %.” The factory setting is “100 %.”