2 safe speed measurement and position detection, Safe speed measurement and position detection, 3safe configuration – Lenze E94AYAE SM301 User Manual
Page 31
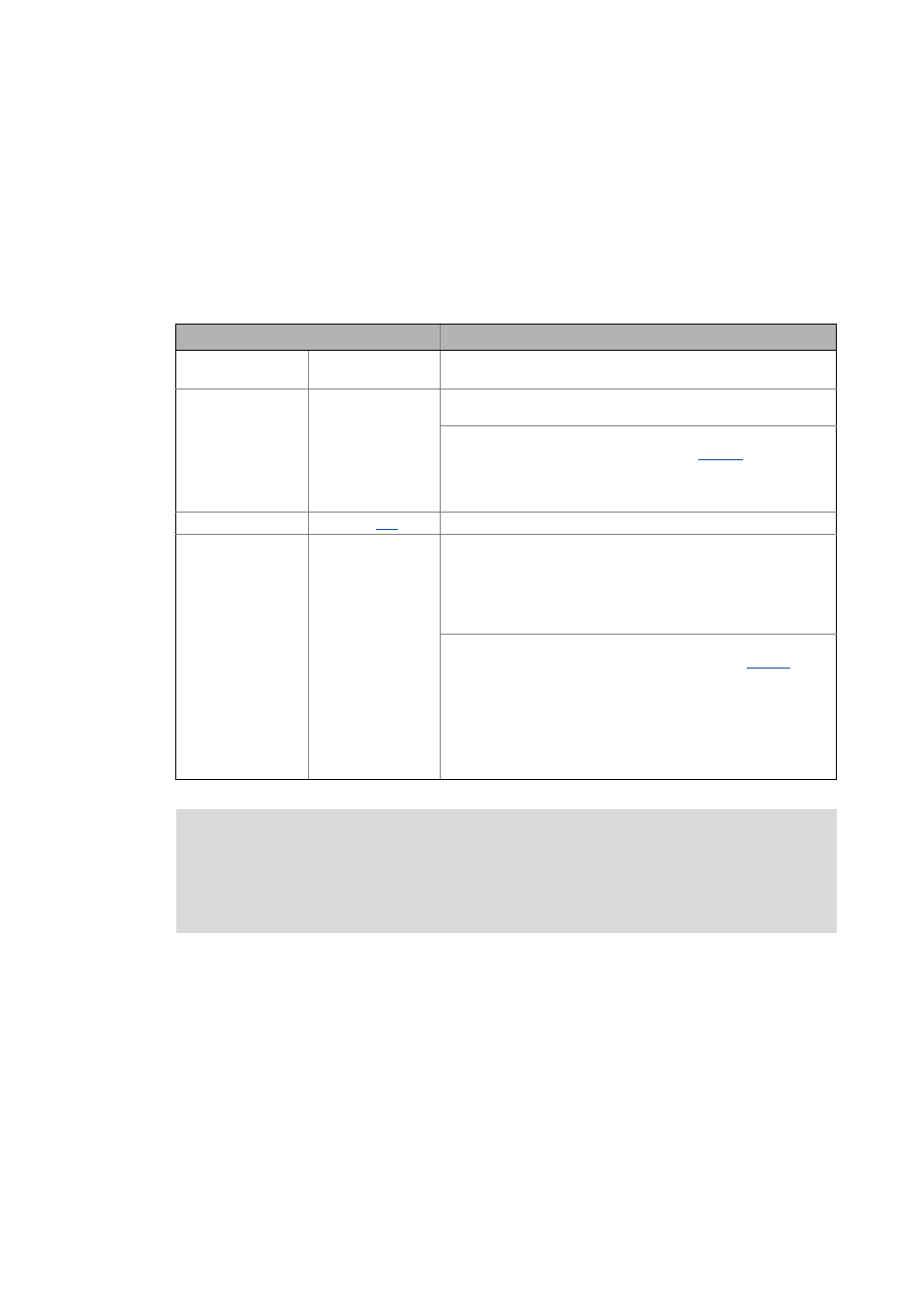
Lenze · SM301 safety module · Parameter setting & configuration · DMS 2.3 EN · 11/2013 · TD05
31
3
Safe configuration
3.6
General parameters
_ _ _ _ _ _ _ _ _ _ _ _ _ _ _ _ _ _ _ _ _ _ _ _ _ _ _ _ _ _ _ _ _ _ _ _ _ _ _ _ _ _ _ _ _ _ _ _ _ _ _ _ _ _ _ _ _ _ _ _ _ _ _ _
3.6.2
Safe speed measurement and position detection
For safe speed measurement a sin/cos encoder must be connected to terminal X8 (Sub-D) at the
controller.
From SM301 V1.3
, you can alternatively connect a two-encoder system consisting of a motor and a
position encoder. When a two-encoder system is selected, a resolver can be used as motor encoder.
From SM301 V1.4
you can carry out the safe speed and position detection via a resolver without the
use of an additional position encoder. For this, connect the resolver to terminal X7.
Safe speed measurement - properties
Explanations
Max. speed
±16000 rpm
Restriction for the use of a resolver:
±(10000 rpm/number of resolver pole pairs)
Response time
encoder monitoring
≥ 12 ms
*
Time required to detect faults caused by continuous signal errors at
the encoder interface.
* From SM301 V1.2:
The response time can be parameterised via
* From SM301 V1.4:
If the resolver is used as a motor encoder without an additional
position encoder, the response time ≥ 50 ms has to be set.
Error response
Error stop (
)
Tolerance threshold
of speed comparison
20 min-1
**
The speed measured by the standard device and the speed measured
by the safety module are checked for plausibility.
• Up to SM301 V1.2, the maximum deviation (after approx. 2
seconds of filtering) is fixedly set to the limit value of 20 rpm.
• The filter time of approx. 2 s is part of the diagnostics function
and irrespective of the response time.
* From SM301 V1.3
:
The tolerance threshold can be parameterised under
.
Important: Select the tolerance threshold as low as possible.
If a speed/position information does not come in during operation,
the diagnostics function must be able to detect this. So, the
parameterised tolerance threshold must be exceeded during
operation for at least more than 2 seconds to ensure the two-
channel encoder information transfer. Selecting the tolerance
threshold too low may lead to a restricted plant availability.
Note!
It is necessary to assess the minimum response time required for the respective system.
A longer response time results in a higher system availability if, for instance, short-time,
process-related speed steps occur at safe operational stop during setting-up operation.