Cleaning -14, Replacement -14, Hoses and tubes -14 2.8.1 – SkyTrak 3606 Service Manual User Manual
Page 30: Hose and tube inspection -14, Hose and tube installation -14, Bearings -14 2.9.1, Bearing removal -14, Bearing cleaning -14
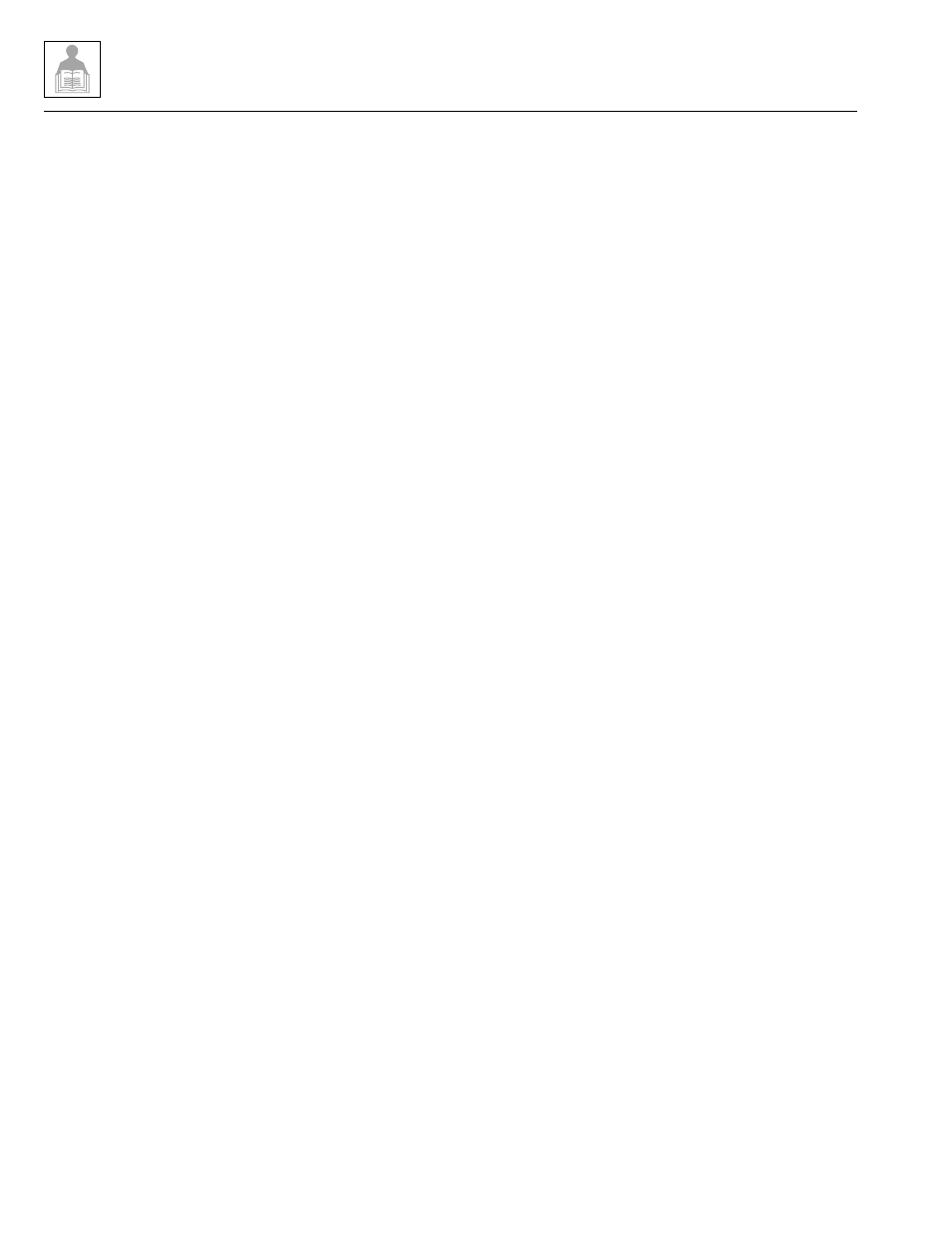
Section 2
2-14
2.6
CLEANING
Dirt and abrasive dust reduce the efficient working life of
parts and systems, and lead to the costly replacement of
components. To help increase the service life of parts,
clean the exterior of all parts before beginning any repairs.
Use cleaning fluids and solvents suitable for cleaning
parts that do not create safety hazards. Certain types of
cleaning fluids can cause skin irritation and damage to
components (such as rubber, electrical parts, etc.).
Servicing the hydraulic system in particular requires
cleanliness.
Follow these precautions before attempting to service
any hydraulic component:
1. Flush hose and tube assemblies with a solvent
compatible with hose materials. Blow excess solvent
away with shop air.
2. Cap hydraulic fittings, hoses and tube assemblies,
and protect threads until time of installation. Clean up
any hydraulic fluid spillage immediately.
3. Flush hydraulic reservoir, fuel tank, and gear housing
with a suitable solvent to remove paint, metal chips,
etc.
4. Protect hydraulic system components from airborne
contaminants. Plug all cylinder, valve, reservoir, tank
and pump openings until time of installation.
5. Use clean, filtered oil when filling the system. Maintain
the hydraulic system at a minimum cleanliness level
of ISO code 18/15-particle ration count.
2.7
REPLACEMENT
ALWAYS use the correct tool when removing or replac-
ing any part or performing any service.
Replace O-rings, seals, and gaskets whenever they are
disturbed. NEVER mix new and old seals or O-rings,
regardless of apparent visual condition. Always lubricate
new seals and O-rings with hydraulic oil before installation.
2.8
HOSES AND TUBES
2.8.1
Hose and Tube Inspection
1. Damaged, dented, crushed, or leaking hose and tube
fittings restrict oil flow and the operation of the
system being served. Fittings showing signs of
movement from their original position have failed and
must be replaced. ALWAYS replace the entire hose
or tube assembly if the fittings are damaged.
2. Hoses must remain in good condition. Obvious signs
of external hose wear or hydraulic fluid leaking or
weeping indicates the need to replace the hose
assembly. If in doubt, replace the hose.
3. Replace if any of the following conditions exist:
• Ballooning (replace hose immediately!)
• Kinking, crushing, stretching or deforming
• Concealed corrosion of wire reinforcement
• Chafed outer cover
2.8.2
Hose and Tube Installation
1. When installing a new hose, loosely connect each
end and verify that the hose takes up the designed
position before tightening the connection completely.
Tighten clamps sufficiently to hold the hose without
crushing it, and to prevent movement and chafing.
2. If a hose is replaced on a moving part, move the part
through its entire range of motion to verify that the
hose will not incur damage. Adjust as necessary.
3. When installing any hose, verify that it does not
become kinked or twisted.
4. NEVER allow freely-moving or unsupported hoses to
contact each other or a related work surface. Such
contact causes chafing and reduces hose life.
2.9
BEARINGS
2.9.1
Bearing Removal
1. NEVER remove bearings unless absolutely
necessary! Always use the recommended puller to
reduce the risk of bearing or related component
damage.
2. When bearings or bushings are removed, verify that
the bearing or bushing is free from discoloration,
nicks, scuffing, and signs of overheating. If in doubt,
replace the bearing or bushing.
2.9.2
Bearing Cleaning
Wear safety glasses. Clean bearings acceptable for ser-
vice in a suitable solvent. NEVER spin-dry a bearing with
compressed air; this can cause metal-to-metal contact
and bearing damage. Compressed air can also cause a
bearing to come apart. After cleaning a bearing, immerse
it in clean lubricating oil until needed.
Model 3606
•
Origin 10/99