8b.7.3, Fuel level sender and gauge b-13, 8b.7.4 – SkyTrak 3606 Service Manual User Manual
Page 183: Fuel lift pump testing b-13, 8b.7.5, Fuel filter b-13, 8b.7.6, Venting air from the fuel system b-13, 8b.7.7, Fuel injectors b-13
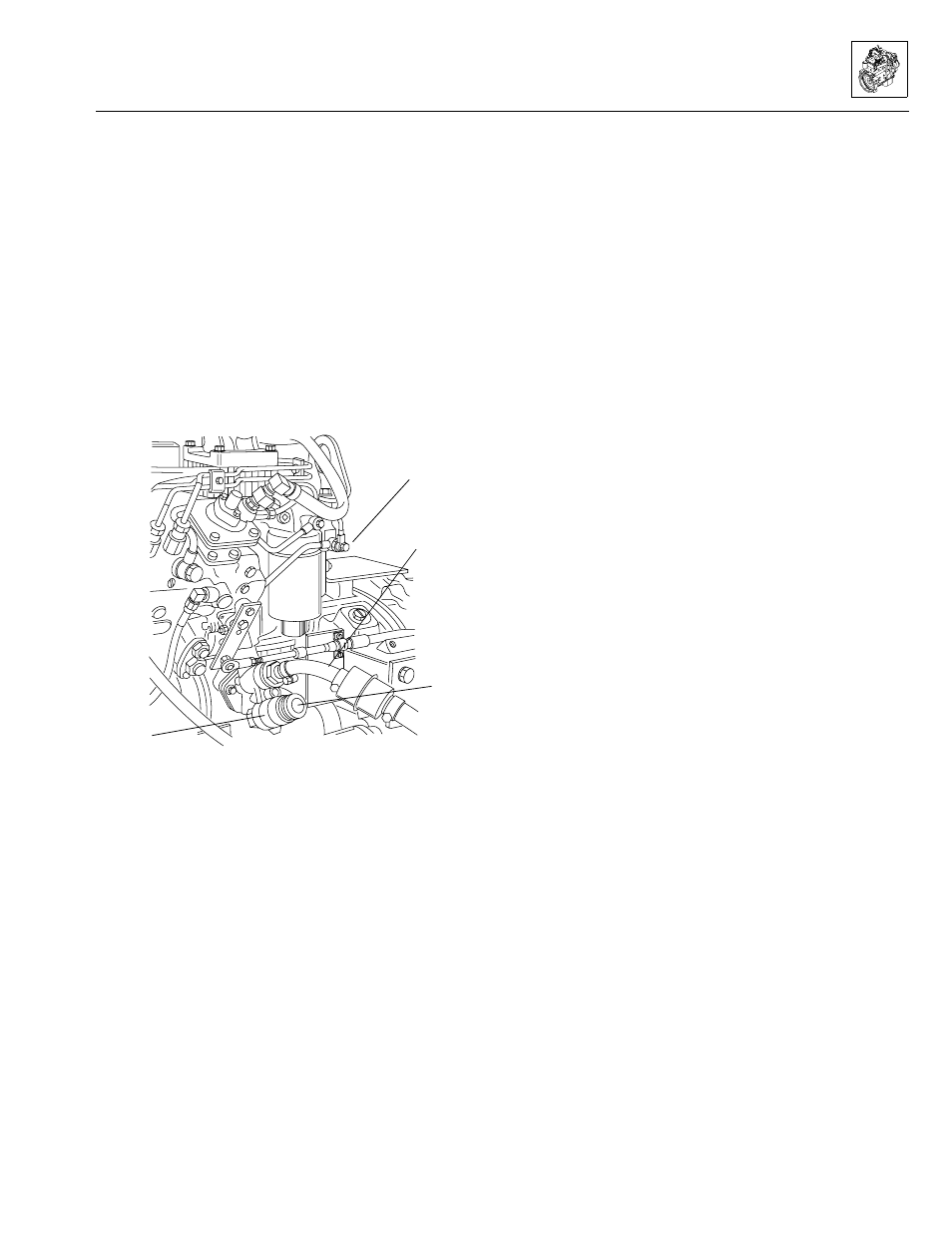
Cummins Engine
8B-13
4. Reconnect the fuel hoses and follow the directions in
Section 4 Cab, Covers and Mirrors to replace the
other fuel system components and the cab.
8B.7.3 Fuel Level Sender and Gauge
The fuel level sender and gauge assembly is described in
Section 10 Electrical System.
8B.7.4 Fuel Lift Pump Testing
Inspect the camshaft lever and return spring for exces-
sive wear. To test the diaphragm, remove the fuel inlet
line from the lift pump. Block the fuel inlet with a finger
(Fig. 8B–8) and operate the hand plunger. A properly
operating pump will provide suction that will remain until
the finger is removed from the inlet.
Figure 8B–8. Testing a typical fuel lift pump.
A. Fuel Lift Pump Removal
1. Clean debris from around the lift pump.
2. Disconnect the fuel lines.
3. Remove the capscrews, gasket, and fuel lift pump.
B. Cleaning and Drying
Clean the exterior of the pump with mineral spirits and
blow dry with compressed air.
Note: Parts replacement is not practical. The fuel lift
pump is serviced as an entire assembly.
C. Fuel Lift Pump Installation
1. Clean the mounting surface on the cylinder block.
2. Install the fuel lift pump with a new gasket. Install and
torque the capscrews to 18 lb/ft (24 Nm).
3. Connect the fuel lines.
8B.7.5 Fuel Filter
Refer to Section 2 General Information, Specifications,
and Maintenance Instructions for information on remov-
ing and replacing the fuel filter (item 1, Fig. 8B–7).
8B.7.6 Venting Air
from the Fuel System
Refer to Section 2 General Information, Specifications,
and Maintenance Instructions, paragraph 2.12.7 D, Vent-
ing Air from the Fuel System.
8B.7.7 Fuel Injectors
The Cummins engine uses Bosch 17 mm closed nozzle
hole-type injectors. The injectors have different part num-
bers for different engine ratings. The last four digits of the
Cummins part number (stamped on the bottom portion of
the injector) identify the injector.
IMPORTANT: Use only the specified injector for the
engine.
During the injection cycle, high pressure from the injec-
tion pump rises to the operating (or “pop”) pressure,
which causes the needle valve in the injector to lift. Fuel
is then injected into the cylinder. A shimmed spring is
used to force the needle valve closed as the injection
pressure drops below the pop pressure to seal off the
nozzle after injection. Failure of the needle valve to lift
and to close at the correct time, or a needle valve that is
stuck open, can cause the engine to misfire and produce
low power. Fuel leaking from the open nozzle can cause
a fuel knock, poor performance, smoke, poor fuel econ-
omy, and rough running.
A. Locating Faulty Fuel Injectors
A faulty fuel injector can cause:
• Misfiring
• Knocking
• Overheating
• Loss of power
• Smoky (black) exhaust
• Increased fuel consumption
The particular faulty fuel injector(s) may be determined
by releasing the pipe union nut on each fuel injector in
turn, with the engine running at a fast “tick-over.” If, after
slackening a pipe union nut, the engine revolutions
remain constant, a faulty fuel injector has been identified.
OS1450
Vent screw
Fuel inlet
line
Hand
plunger
Lift
pump
Model 3606 • Origin 10/99