SkyTrak 3606 Service Manual User Manual
Page 284
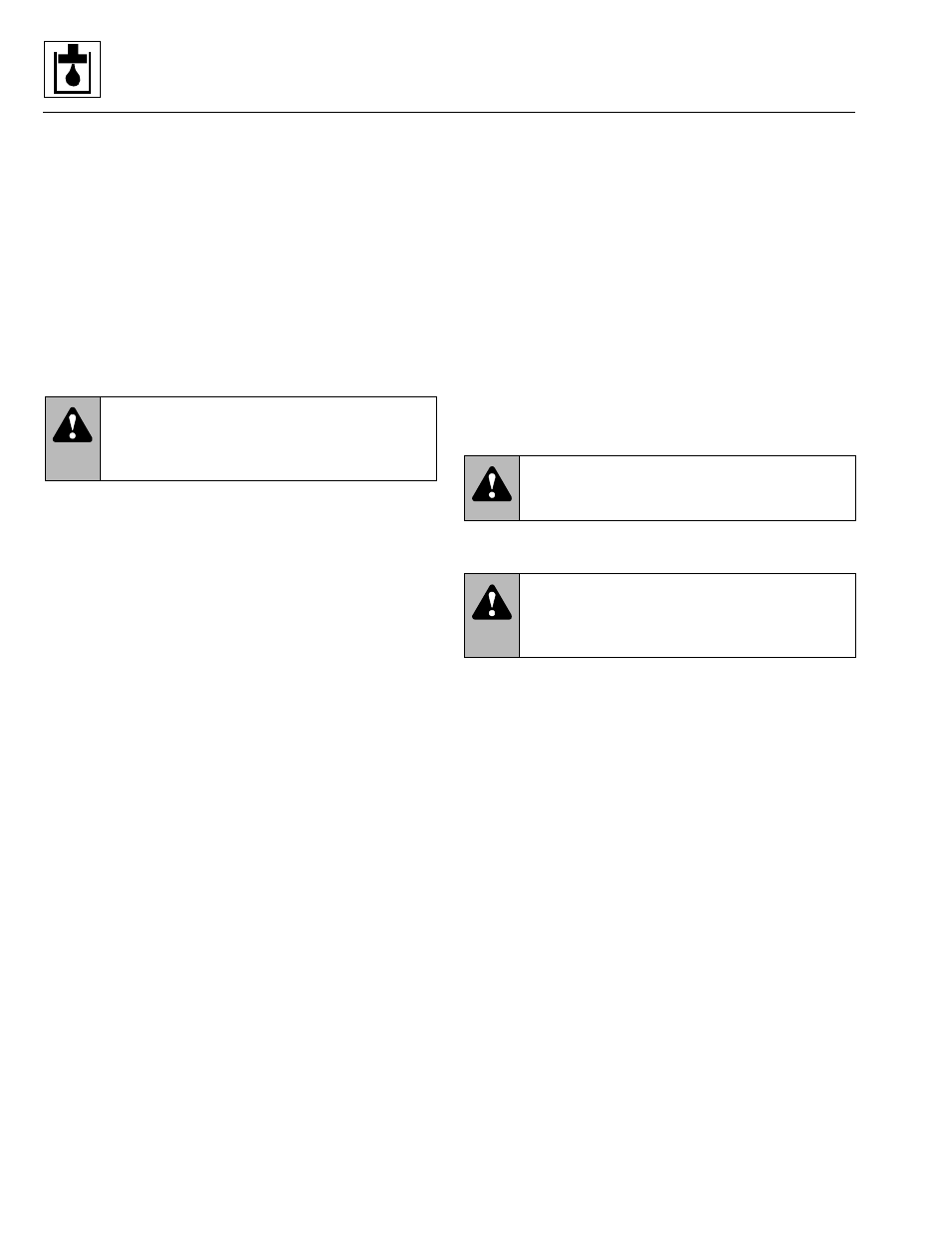
Section 9
9-90
2. Install the lower attachment tilt cylinder pin by tapping
it out through the bottom of the quick attach (if
installed).
3. Coat the attachment tilt cylinder base pin with anti-
seize compound and install the pin by tapping it in
through the top of the gooseneck.
4. Secure the attachment tilt cylinder base pin to the
boom with two 2" external retaining rings.
5. Install the lower pivot pin and quick attach as
required.
6. Connect the attachment tilt cylinder hydraulic hoses
in relation to the labels or markings made during
removal.
7. Start the engine and run at approximately one-third
to one-half throttle for about one minute without
moving the vehicle or operating any hydraulic
functions.
8. Inspect for leaks and check the level of the hydraulic
fluid in the reservoir. Add hydraulic fluid to the
reservoir as needed. Shut the engine OFF.
9. Wipe up any hydraulic fluid spillage in, on, near and
around the vehicle, work area and tools.
10. Conduct a pressure check of the attachment tilt
cylinder hydraulic circuit and bleed the circuit as
outlined below.
g. Attachment Tilt Cylinder Pressure Checking
and Circuit Bleeding
1. Attach a 4000 psi (276 bar) gauge to the main control
valve at the extend base port relief to test the
attachment tilt cylinder hydraulic system circuit
pressure. The unit is equipped with test fittings from
the factory. Pressure readings should be 3200 psi ±
100 psi (220,6 ± 7 bar).
2. With no accessory installed on the quick attach, start
with the hoist and fork tilt cylinders fully retracted.
3. Fully extend the fork tilt cylinder. Hold the fork tilt
joystick at full extend while fully raising the hoist
cylinder.
4. Fully retract the fork tilt cylinder. Hold the fork tilt
joystick at full retract while fully retracting the hoist
cylinder.
5. Repeat steps 3 and 4 five times.
9.10.2 Slave Cylinders
Each slave cylinder (Fig. 9– 65) is secured to the vehicle
frame and outer boom with cylinder mount pins, hex-
head capscrews and nuts.
a. Slave Cylinder Removal
Note: An additional O-ring may be included at the base
of the cylinder rod. This additional O-ring may be
discarded, as it served only in a temporarily protective
role to keep paint off the rod while the cylinder was
painted at the factory.
1. Park the vehicle on a firm, level surface, fully retract
all hydraulic cylinders, then raise the boom to
approximately a 30-degree angle. Place the travel
select lever in NEUTRAL (N), engage the park brake
switch and shut the engine OFF.
2. Unlatch, unlock and open the engine cover. Allow the
hydraulic fluid to cool.
3. Label or otherwise mark the hydraulic hoses in
relation to the slave cylinder being removed.
Disconnect and cap the hydraulic hoses and slave
cylinder fittings.
4. Securely support the slave cylinder. Remove the
nuts, hex-head capscrews and cylinder pins securing
the slave cylinder to the vehicle frame and outer
boom. Refer to Section 3.2.3 A. Outer Boom
Removal as required.
5. With the help of at least one assistant, remove the
slave cylinder from the vehicle. Wipe up any hydraulic
fluid spillage in, on, near and around the vehicle.
b. Slave Cylinder Disassembly
1. Clean the slave cylinder (Fig. 9– 65) with a suitable
cleaner before inspection.
2. Place the slave cylinder in a soft-jawed vise or other
acceptable holding equipment if possible. DO NOT
damage the tube. If necessary, remove the grease
fitting from the end of the rod weldment (15).
3. Extend the rod weldment (15) to allow access to the
base of the cylinder.
WARNING: Avoid prolonged engine operation
in closed areas with inadequate ventilation.
Failure to properly ventilate exhaust fumes can
result in death or severe personal injury.
WARNING: Hot hydraulic fluid can cause
severe burns. Wait for hydraulic fluid to cool
before servicing any hydraulic component.
WARNING: Escaping hydraulic fluid under
pressure can penetrate the skin, causing seri-
ous injury. Relieve hydraulic pressure before
servicing any hydraulic component.
Model 3606 • Origin 10/99