8a.7.5, Fuel filter a-14, 8a.7.6 – SkyTrak 3606 Service Manual User Manual
Page 160: Venting air from the fuel system a-14, 8a.7.7, Fuel injectors a-14
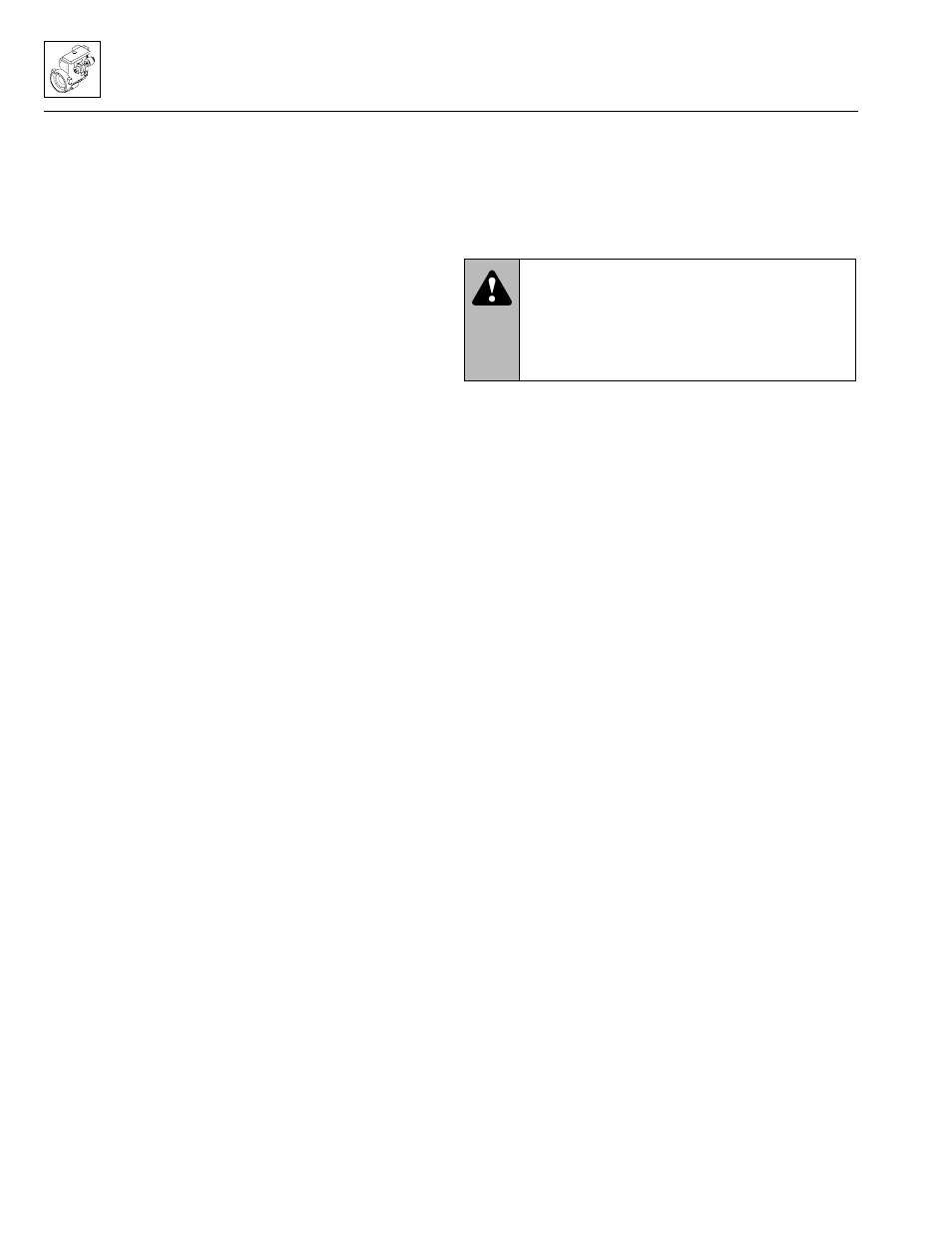
Section 8A
8A-14
8A.7.5 Fuel Filter
Refer to Section 2 General Information, Specifications,
and Maintenance Instructions for information on remov-
ing and replacing the fuel filter (item 1, Fig. 8A–7).
8A.7.6 Venting Air from the Fuel System
Refer to Section 2 General Information, Specifications,
and Maintenance Instructions, paragraph 2.12.7 D, Vent-
ing Air from the Fuel System.
8A.7.7 Fuel Injectors
The Perkins engine uses closed nozzle hole-type injec-
tors (or “atomizers”). The injectors have different part
numbers for different engine ratings. The Perkins fuel
injector code (stamped on the fuel injector body) identify
the injector.
IMPORTANT: Use only the specified injector for the
engine.
During the injection cycle, high pressure from the injec-
tion pump rises to the operating (or “pop”) pressure,
which causes the needle valve in the injector to lift. Fuel
is then injected into the cylinder. A shimmed spring is
used to force the needle valve closed as the injection
pressure drops below the pop pressure to seal off the
nozzle after injection. Failure of the needle valve to lift
and to close at the correct time, or a needle valve that is
stuck open, can cause the engine to misfire and produce
low power. Fuel leaking from the open nozzle can cause
a fuel knock, poor performance, smoke, poor fuel econ-
omy, and rough running.
A. Locating Faulty Fuel Injectors
A faulty fuel injector can cause:
• Misfiring
• Knocking
• Overheating
• Loss of power
• Smoky (black) exhaust
• Increased fuel consumption
The particular faulty fuel injector(s) may be determined
by releasing the pipe union nut on each fuel injector in
turn, with the engine running at a fast “tick-over.” If, after
slackening a pipe union nut, the engine revolutions
remain constant, a faulty fuel injector has been identified.
To test a fuel injector:
1. Remove the fuel injector from the cylinder head.
2. Invert the fuel injector with the nozzle facing out, then
retighten the unions.
3. Loosen the unions of the other fuel injector pipes (to
help avoid the possibility of the engine starting).
4. Operate the starter to turn the engine over until fuel
sprays from the nozzle. Examine the shape of the
spray. If the spray is unduly “wet” or “streaky”, or
obviously sprays to one side, or if the nozzle
“dribbles” fuel, it may only be necessary to probe the
nozzle holes to remove blockage.
IMPORTANT: DO NOT attempt to adjust injection pres-
sure without a testing pump and pressure gauge. It is
impossible to accurately adjust the setting of fuel injec-
tors without the proper equipment.
A perfect fuel injector, when tested by pumping fuel
through it in the open air, gives a short “pinging” sound as
the fuel emerges from the holes. After the fuel injector
has been in service for some time, the pinging changes
to a crackling sound. It is not until the fuel injector sounds
“dead” that its condition is likely to affect the running of
the engine.
B. Injector Replacement
Preparatory steps:
• Thoroughly clean around the injector(s)
• Disconnect the high-pressure fuel line(s)
• Disconnect the fuel drain manifold
IMPORTANT: The injector must not rotate in the bore of
the cylinder head or damage to the cylinder head will
occur. If rust has formed on the hold-down nut, soak the
nut with rust-penetrating solvent for a minimum of three
minutes. Then, tap the injector body with a drift pin to
help loosen any rust.
To Replace a Fuel Injector:
1. Remove the fuel leak-off pipe.
2. Remove the high-pressure pipe union nuts from the
fuel injector and fuel injection pump and release the
pipe.
3. Remove the fuel injector flange nuts and remove the
fuel injector and seat washer.
WARNING: KEEP CLEAR of spraying fuel.
Diesel fuel will spray when venting high pres-
sure lines. The fuel pressure is sufficient to
penetrate the skin and cause serious bodily
injury. Wear protective clothing and safety
glasses.
Model 3606 • Origin 10/99