Before reading this chapter, Parameter configurations – Yaskawa FSP Amplifier User Manual
Page 70
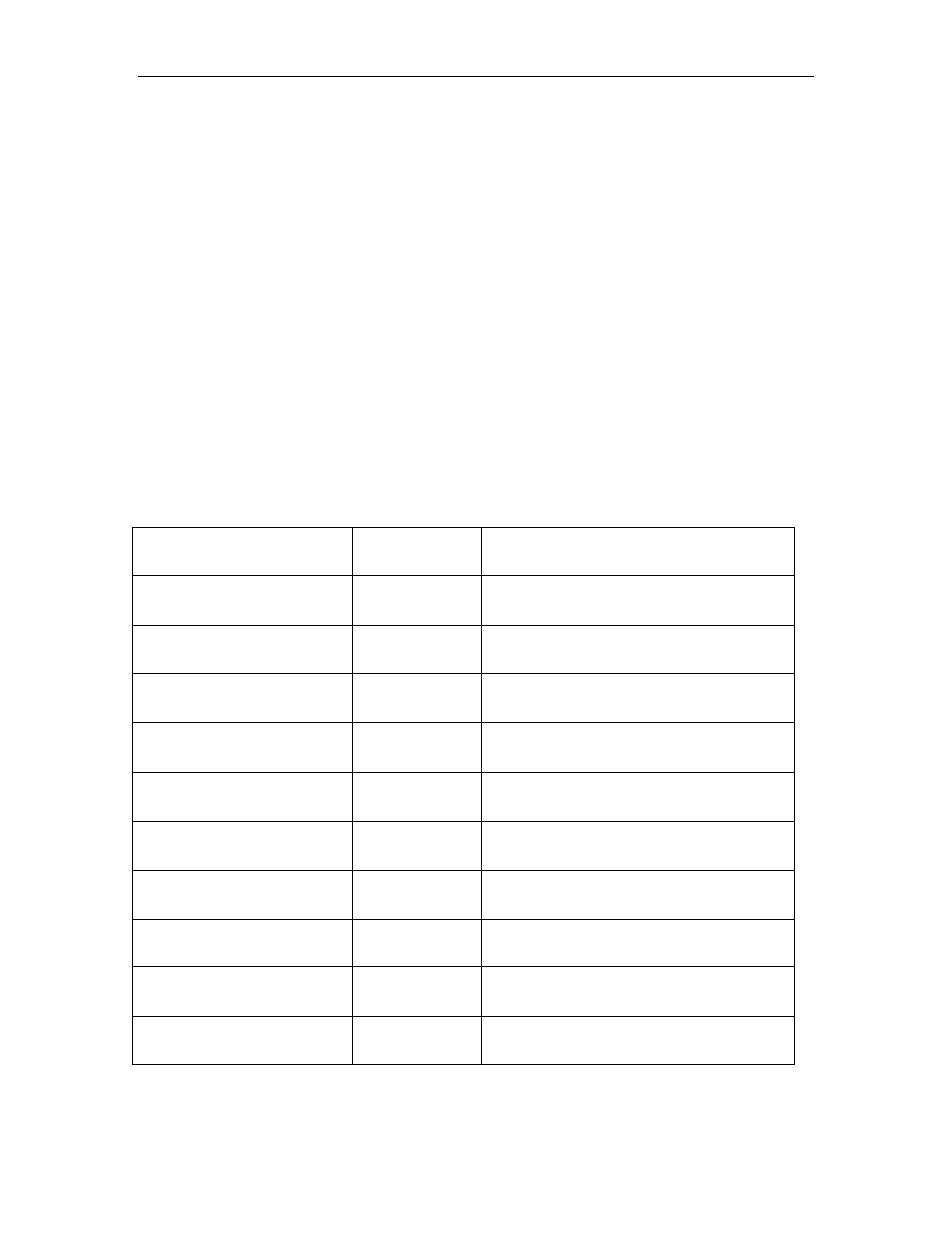
FSP Amplifier User’s Manual
Chapter 5: Parameter Settings and Functions
5-3
Before Reading this Chapter
This chapter describes the use of each CN1 connector I/O signals in the
FSP Amplifier as well as the procedure for setting the related parameters
for the intended purposes.
The following sections can be used as references for this chapter.
• List of CN1 I/O signals: See 3.4.3. I/O Signal Names and Functions.
• CN1 I/O signal terminal layout: See 3.4.2. List of CN1 Terminals.
• List of parameters: Appendix D. List of Parameters.
• Parameter setting procedure: 7.1.5 Operation in Parameter Setting
Mode
The CN1 connector is used to exchange signals with the host controller and
external circuits.
Parameter Configurations
Parameters are comprised of the types shown in the following table. See
Appendix D. List of Parameters.
Type
Parameter
Number
Description
Function Selection Constants
Pn000 to Pn007
Pn550 to Pn551
Select basic and application functions such as
the type of control or the stop mode used when
an alarm occurs.
Servo Gain and Other
Constants
Pn100 to Pn11E
Pn1A0 to Pn1C0
Set numerical values (speed control).
Set numerical values (position control).
Position Control Constants
Pn200 to Pn216
Pn2A2 to Pn2CB
Set position control parameters such as the
reference pulse input form gear ratio and
application setting.
Speed Control Constants
Pn300 to Pn308
Set speed control parameters such as speed
reference input gain and soft start deceleration
time.
Torque Control Constants
Pn400 to Pn40A
Set torque control parameters such as the
torque reference input gain and
forward/reverse torque limits.
Sequence Constants
Pn500 to Pn511
Pn200 to Pn2D2
Set output conditions for all sequence signals
and change I/O signal selections and
allocations.
Others
Pn600 to Pn601
Specify the capacity for an external
regenerative resistor and reserved constants.
Auxiliary Function Execution
Fn000 to Fn013
Execute auxiliary functions such as JOG Mode
operation.
Monitor Modes
Un000 to Un00D
Enable speed and torque reference
monitoring, as well as monitoring to check
whether I/O signals are ON or OFF.
Encoder Selection
Pn190 to Pn192
Encoder type selection