Ultra5000 power wiring diagrams, This drawing included for reference only – Rockwell Automation 2098-IPD-xxx Ultra5000 Intelligent Positioning Drives Installation Manual User Manual
Page 127
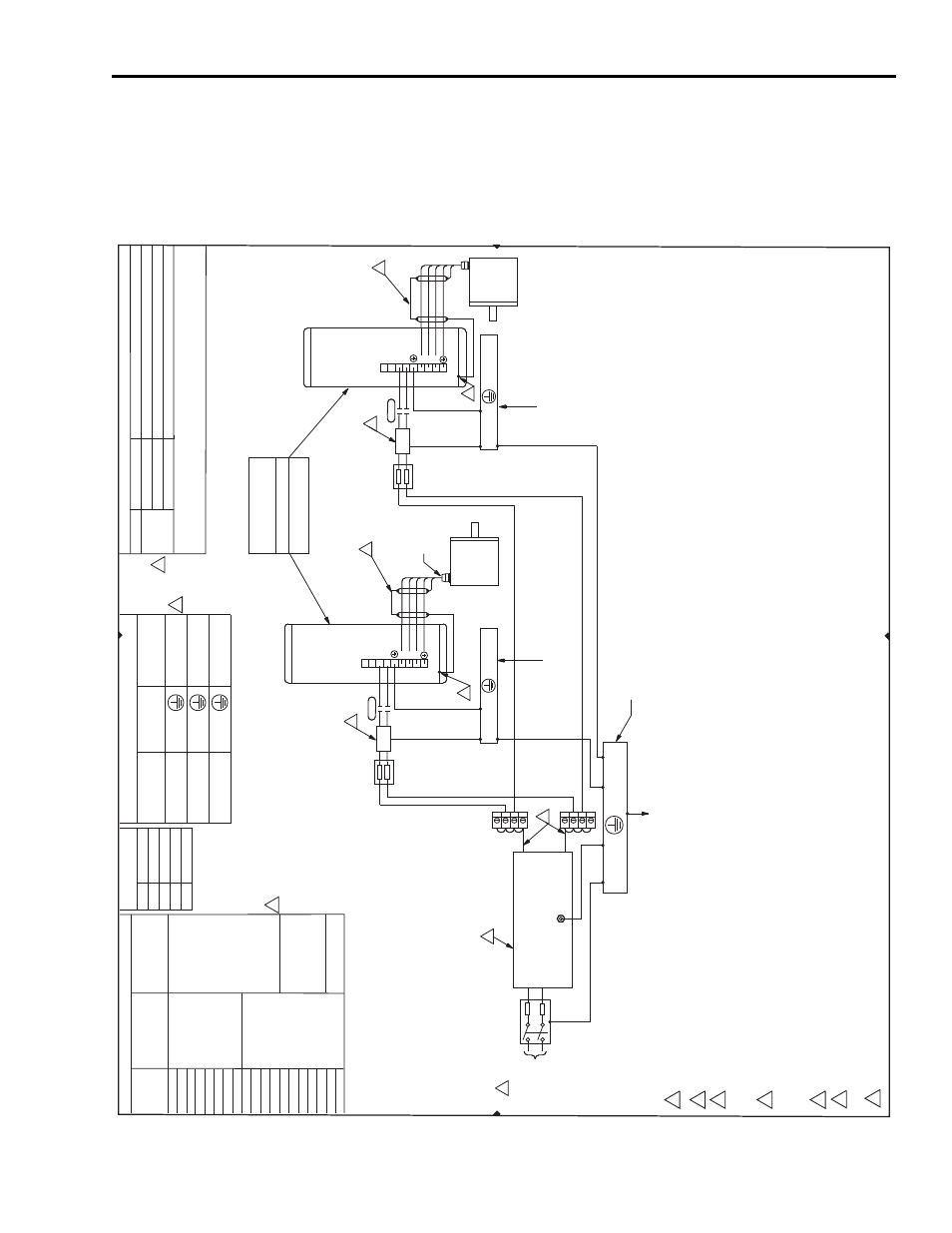
Publication 2098-IN001E-EN-P — April 2002
Interconnect Diagrams
B-15
Ultra5000 Power Wiring
Diagrams
This section provides information to assist you with AC input and
motor power wiring to your Ultra5000 drive.
Figure B.14
Typical Power Wiring of Ultra5000 System
2098-IPD-005-xx, -010-xx, and -020-xx
9
9
11
5
11
2
MACHINE COMMON
GROUNDING BUS BAR
T
O PROTECTIVE
EAR
TH TERMINAL
ISOLA
TION OR
AUT
O
TRANSFORMER
(OPTIONAL, NOT
REQUIRED WHEN
DESIRED INPUT
VOL
T
AGE IS
A
V
AILABLE
DIRECTL
Y
FROM
THE LINE)
FUSED DISCONNECT
OR CIRCUIT
BREAKER
SINGLE PHASE
AC LINE
50/60Hz
L1
L2/N
TRANSFORMER
CHASSIS
TERM.
BLOCK
FUSE
BLOCK
M1
L2/N
U
V
W
L1
DC-
DC+
FUSE
BLOCK
L2/N
L1
DC-
U
V
W
DC+
10
10
Y
-SERIES
LD-2003
H-3007
LD-3009
LD-4012
LD-4030
H-3016
H-4030
F-4030
MPL-A310
MPL-A320
H-4050
F-4050
MPL-A330
MPL-A420
MPL-A430
MPL-A4520
MPL-A4530
MOT
OR POWER
MA
TING CONNECT
OR
CONT
ACT
SIZE
N-SERIES
MOT
OR
MINIMUM
RECOMMENDED
POWER WIRE
(75°C COPPER MIN)
A
B
C
D
PIN
SIGNAL
U
V
W
MOT
OR CASE
4
COMMON GROUNDING
POINT
FOR
AMPLIFIER
SYSTEM (ONE PER
AXIS)
COMMON GROUNDING
POINT
FOR
AMPLIFIER
SYSTEM (ONE PER
AXIS)
mm (A
WG)
mm (A
WG)
AC LINE FIL
TER
9
M2
AC LINE
FIL
TER
RECOMMENDED
POWER WIRE
(75°C COPPER MIN)
mm (A
WG)
COMP
A
TIBLE
MOT
ORS
12
MOT
OR POWER
CONNECT
OR
AND MA
TING
CONNECT
OR
COMP
A
TIBLE
MOT
ORS
9
INTELLIGENT
POSITIONING
DRIVE
INTELLIGENT
POSITIONING
DRIVE
2
2
2
2
2
2
2
2
T
ORQUE ALL
TERMINALS
T
O 1.25 Nm (1
1 LB-IN.)
TERMINAL
STRIP
ACCEPT
ABLE WIRE RANGE
?mm (A
WG)
0.5-4.0mm (20-12
A
WG)
2
2
DIGIT
AL
DRIVE MODULE INPUT
CURRENT
REQUIREMENTS
INPUT
POWER WIRES
MOT
OR POWER
CONNECT
OR
MOT
OR POWER
WIRES
U,
V
,
W
,
AND
GND
TERMINA
TE
THE MOT
OR POWER CABLE SHIELD BY
CLAMPING IT
T
O
THE DRIVE WITH
THE BRACKET
PROVIDED.
THIS BRACKET
CAN BE USED FOR STRAIN RELIEF IF NON-SHIELDED CABLES
ARE USED.
SNUG BRACKET
SCREWS, DO NOT
OVER
TIGHTEN. NEVER
T
ORQUE OVER 10 LB-IN.
AC LINE FIL
TER
AND SHIELDED MOT
OR CABLE
ARE
T
O BE USED FOR IMPROVING
THE DRIVE MODULES ELECTROMAGNETIC
COMP
A
TIBILITY
,
AND
ARE REQUIRED
T
O MEET
THE EUROPEAN ELECTROMAGNETIC COMP
A
TIBILITY
DIRECTIVE. CAUTION:
AC LINE FIL
TERS HA
VE LARGE LEAKAGE CURRENTS
AND REQUIRE DISCHARGE
TIME UPON POWER REMOV
AL. WIRING BETWEEN
THE DRIVE MODULE
AND FIL
TER SHOULD BE KEPT
AS SHOR
T
AS POSSIBLE.
THE COMMON GROUND BUS BAR SHOULD BE
AS
CLOSE T
O THE
DRIVE
AS
POSSIBLE.
A
SUPPL
Y
DISCONNECTING DEVICE IS REQUIRED FOR MAINTENANCE & SAFETY
. LOCAL
REGULA
TIONS SHOULD BE OBSER
VED.
IF
A
GROUNDED NEUTRAL
IS USED INSTEAD OF L2, ONL
Y
L1 MA
Y
BE SWITCHED OR FUSED.
CURRENT
RA
TINGS
ARE INDEPENDENT
OF
THE INPUT
VOL
T
AGE. REDUCED VOL
T
AGE WILL
RESUL
T
IN
A
REDUCTION IN SPEED,
BUT
NOT
T
ORQUE.
WIRE SIZES
ARE MINIMUM RECOMMENDED V
ALUES.
THE REQUIREMENTS OF LOCAL
REGULA
TIONS SHOULD BE OBSER
VED.
MUL
TIPLE DRIVE MODULES MA
Y
BE POWERED FROM ONE
TRANSFORMER OR OTHER
AC SUPPL
Y
SOURCE.
DO NOT
DAISY
CHAIN DRIVE MODULE POWER CONNECTIONS. MAKE SEP
ARA
TE CONNECTIONS DIRECTL
Y
T
O
THE
AC SUPPL
Y
.
DRIVE RA
TED 100-240 V
AC RMS, SINGLE PHASE INPUT
VOL
T
AGE (230 V
AC ST
ANDARD).
NOTES
2
4
9
10
11
5
6.
8.
2
1.5mm (16
A
WG)
3.0mm (12
A
WG)
2
1.5mm (16
A
WG)
3.0mm (12
A
WG)
2
2.5mm (14
A
WG)
TERMINALS
DRIVE
2098-IPD-005-xx
L1,L2/N
L1,L2/N
L1,L2/N
2.5mm (14
A
WG)
1.5mm (16
A
WG)
3.0mm (12
A
WG)
POWER INITIALIZA
TION REQUIRES
A
SHOR
T
PERIOD OF INRUSH CURRENT
OF 100A
FOR
THE INPUT
. DUAL
ELEMENT
TIME DELA
Y
(SLOW BLOW) FUSES
ARE RECOMMENDED.
FUSE SIZES MUST
BE SELECTED
ACCORDING
T
O LOCAL
REGULA
TIONS.
18.0 Amps AC
at
100-240
V
olts AC
9.0
Amps
AC at 100-240 V
olts
AC
L1,L2/N
5.0
Amps
AC at 100-240 V
olts
AC
CURRENT
REQUIREMENT
, MAXIMUM (AMPS
AC RMS)
TERMINALS
DRIVES
NOTE:
12
IF USING
AN
AUT
OTRANSFORMER, ENSURE
THE PHASE
T
O NEUTRAL/GROUND VOL
T
AGE DOES NOT
EXCEED 265V
AC
A
T
THE DRIVE
AC INPUT
.
2098-IPD-010-xx
2098-IPD-020-xx
2098-IPD-005-xx
2098-IPD-010-xx
2098-IPD-020-xx
This drawing included
for reference only
.