INFICON XTC/C Thin Film Deposition Controller User Manual
Page 156
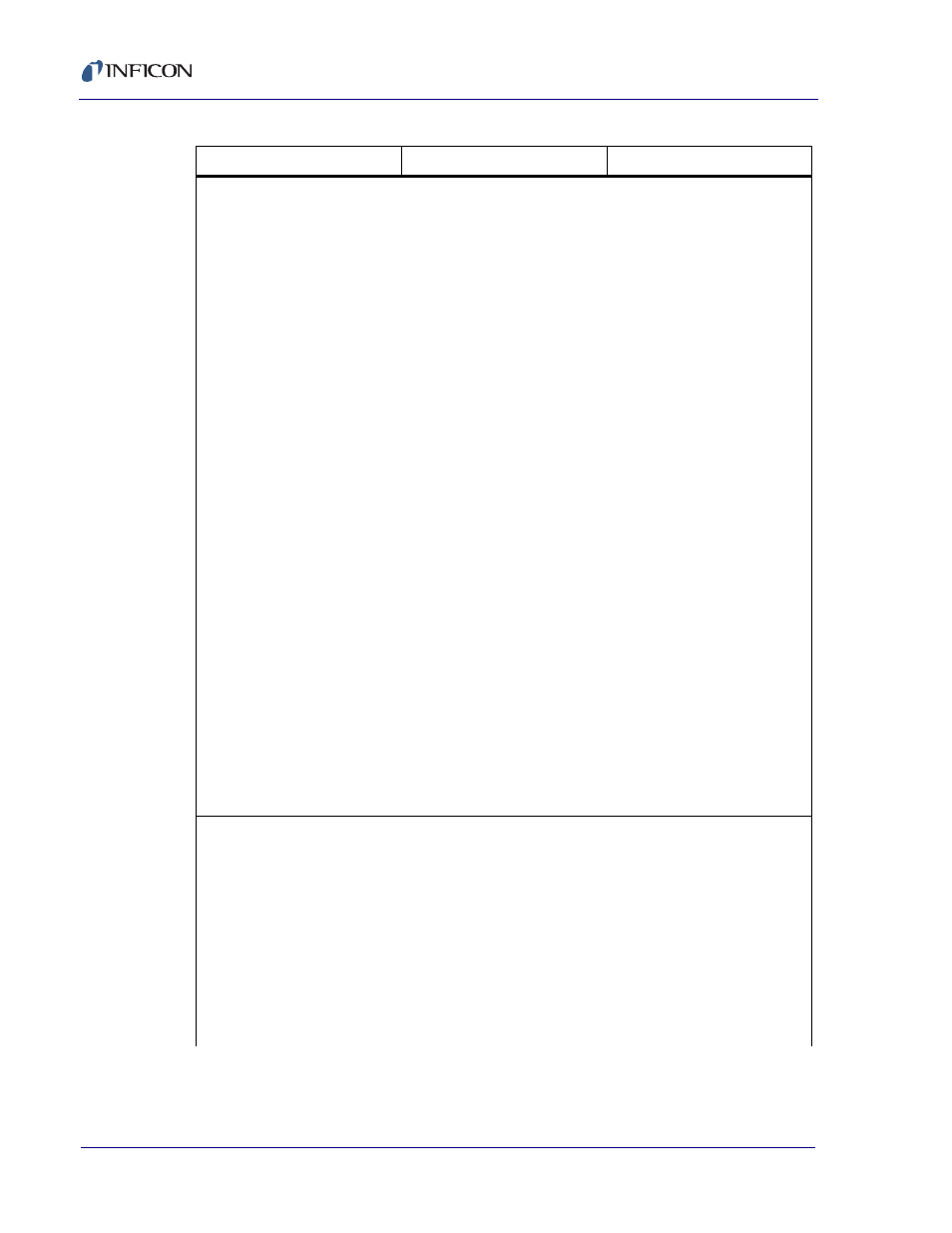
6 - 8
IP
N 07
4-
18
3X
XTC/C - XTC/2 Operating Manual
5. thermal instability: large
changes in thickness reading
during source warm-up
(usually causes thickness
reading to decrease) and after
the termination of deposition
(usually causes thickness
reading to increase)
a. inadequate cooling
water/cooling water
temperature too high
a. check cooling water flow
rate, be certain that cooling
water temperature is less than
30 °C; refer to appropriate
sensor manual
b. excessive heat input to the
crystal
b. if heat is due to radiation
from the evaporation source,
move sensor further away
from source and use
sputtering crystals for better
thermal stability; install
radiation shield
c. crystal not seated properly
in holder
c. clean or polish the crystal
seating surface on the crystal
holder
d. crystal heating caused by
high energy electron flux
(often found in RF sputtering)
d. use a sputtering sensor
head
e. poor thermal transfer from
water line to body (CrystalSix
sensor)
e. use a new water tube
whenever the clamping
assembly has been removed
from the body; if a new water
tube is not available, use a
single layer of aluminum foil
between the cooling tube and
sensor body, if your process
allows
f. poor thermal transfer
(Bakeable)
f. use Al or Au foil washer
between crystal holder and
sensor body
6. poor thickness
reproducibility
a. variable source flux
distribution
a. move sensor to a more
central location to reliably
sample evaporant, ensure
constant relative pool height
of melt, avoid tunneling into
the melt
b. sweep, dither, or position
where the electron beam
strikes the melt has been
changed since the last
deposition
b. maintain consistent source
distribution by maintaining
consistent sweep
frequencies, sweep amplitude
and electron beam position
settings
Table 6-2 Troubleshooting Transducers/Sensors (continued)
SYMPTOM
CAUSE
REMEDY