6 control loop theory – INFICON XTC/C Thin Film Deposition Controller User Manual
Page 144
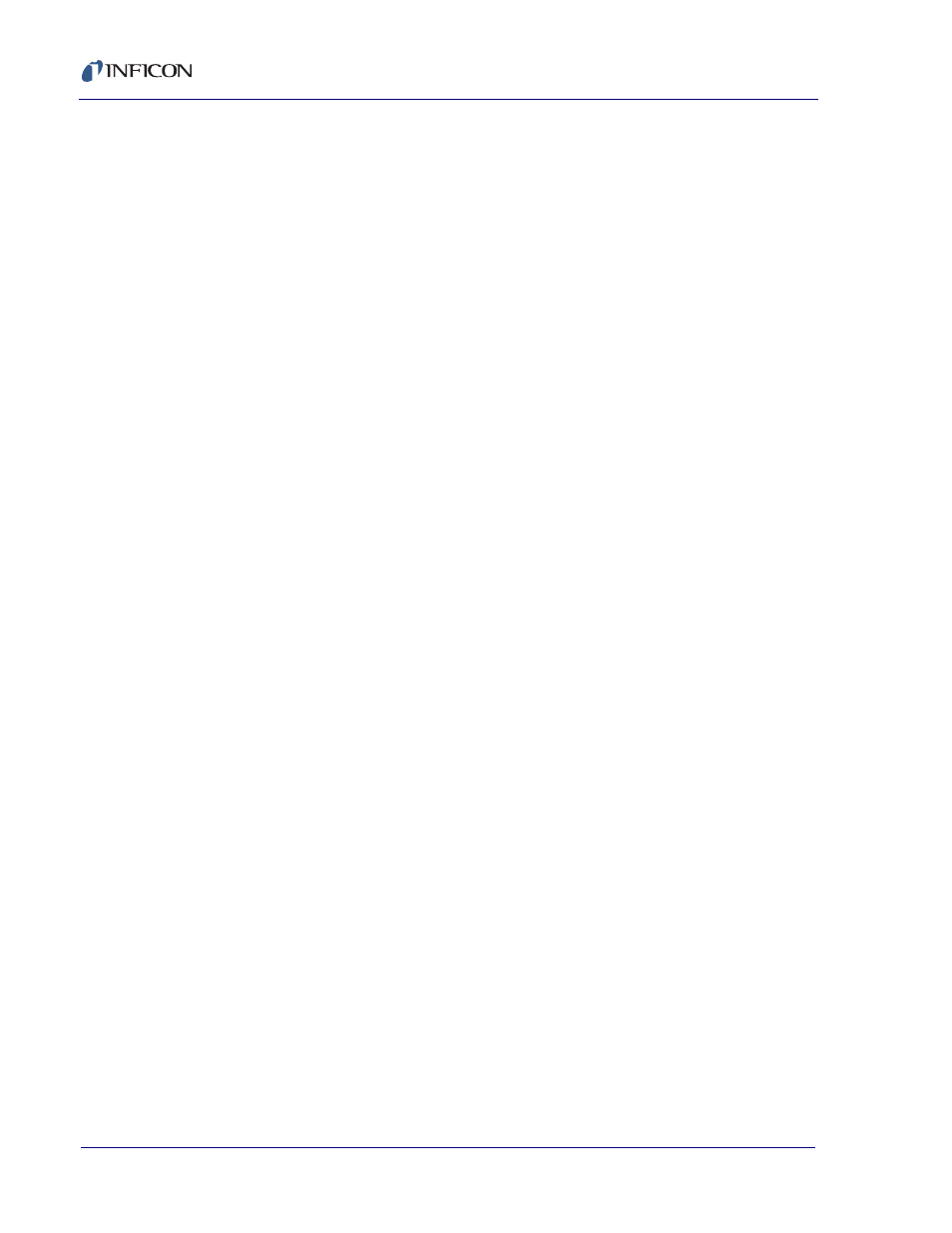
5 - 12
IP
N 07
4-
18
3X
XTC/C - XTC/2 Operating Manual
frequencies slightly higher than resonance it is inductive in nature. This
information is useful if the resonance frequency of a crystal is unknown. A quick
sweep of frequencies can be undertaken until the output of the phase
comparator changes, marking the resonance event.
For AT crystals we know that the lowest frequency event encountered is the
fundamental. The events slightly higher in frequency are anharmonics. This
information is useful not only for initialization, but also for the rare case when
the instrument loses track of the fundamental. Once the frequency spectrum of
the crystal is determined the instrument’s task is to follow the changing
resonance frequency and to periodically provide a measurement of the
frequency for subsequent conversion to thickness.
The use of the “intelligent” measurement system has a series of very apparent
advantages when compared to the previous generation of active oscillators;
namely immunity from mode hopping, speed of measurement, precision of
measurement, and the ability to measure heavily loaded (damped) crystals.
5.6 Control Loop Theory
The instrumental advances in measurement speed, precision and reliability
would not be complete without a means of translating this improved information
into improved process control. For a deposition process, this means keeping
the deposition rate as close as possible to the desired rate. The purpose of a
control loop is to take the information flow from the measurement system and
to make power corrections that are appropriate to the characteristics of the
particular evaporation source. When properly operating, the control system
translates small errors in the controlled parameter, or rate, into the appropriate
corrections in the manipulated parameter, power. The controller’s ability to
quickly and accurately measure and then react appropriately to the small
changes keeps the process from deviating very far from the set point.
The controller model most commonly chosen for converting error into action is
called PID. In the PID, P stands for proportional, I stands for integral and D
stands for derivative action. Certain aspects of this model will be examined in
detail a little further on.
Knowledge of the responses of the evaporation source can be found by
repetitively observing the system response to a disturbance under a particular
set of controller settings. After observing the response, improved controller
parameters are estimated and then tried again until satisfactory control is
obtained. Control, when it is finally optimized, essentially matches the
parameters of the controller model to the characteristics of the evaporation
source.