Position follower (master encoder), Hardware set up – Rockwell Automation 1398-DDM-xxx ULTRA 100 Series Drives Installation Manual User Manual
Page 126
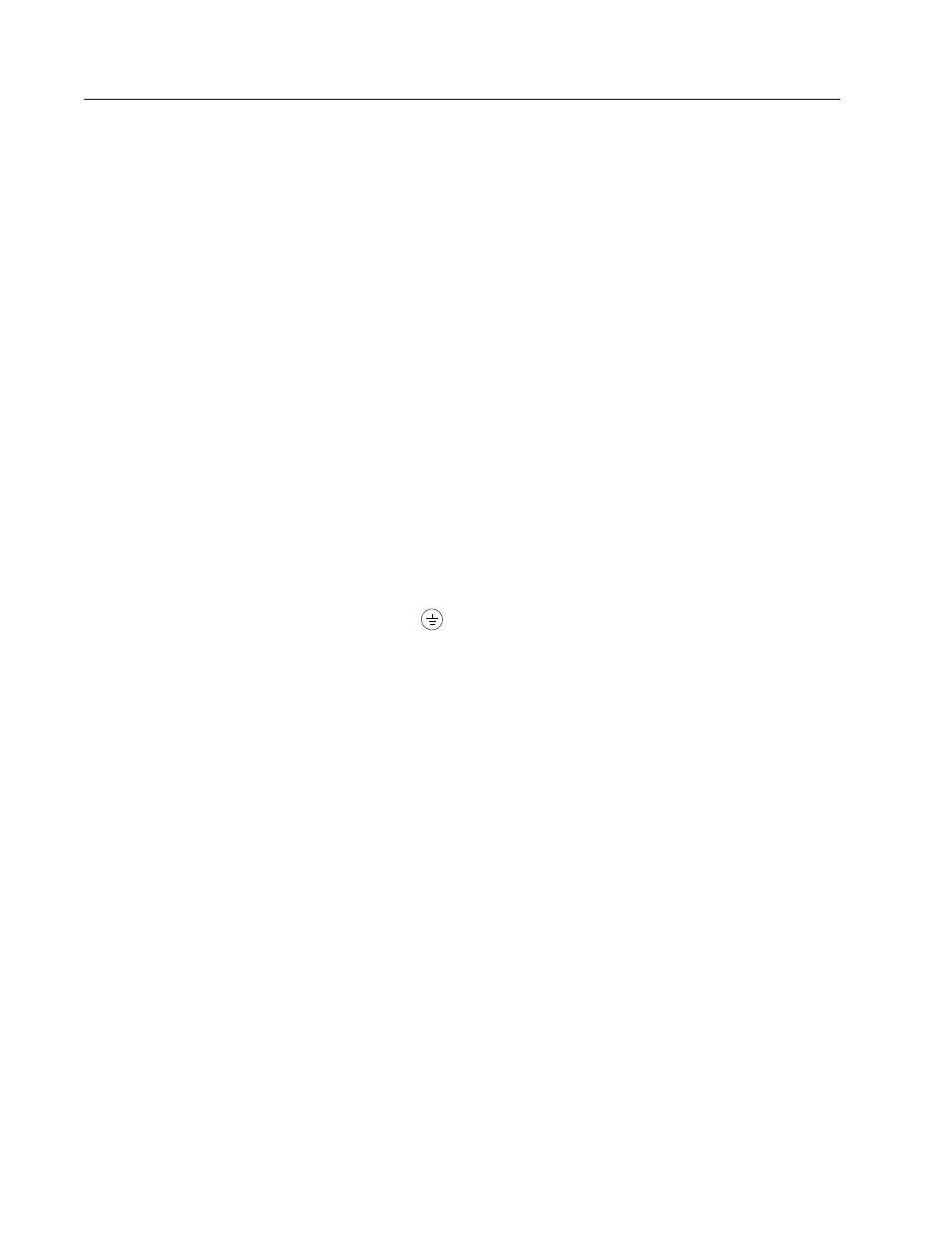
Publication 1398-5.2 – PDF 1997
8-12
Application and Configuration Examples
8Application and Configuration Examples
Position Follower (Master
Encoder)
The ULTRA 100 Series can be electronically geared to a master
incremental encoder generating quadrature encoder signals by making
the hardware connections and performing the software setup and
tuning described below. The connection diagram depicts the minimum
hardware necessary. Interfacing the drive to an external controller
requires similar circuitry from the controller to J1. Instructions are
provided to configure the drive using a PC with ULTRA Master
software, but the optional TouchPad also may be used.
Hardware Set Up
Make the connections described below and shown in the Figure 8.3.
The appendix “Options and Accessories” on page A-1 lists the
interconnect cables available from the factory.
1. Connect an RS-232 cable between the serial port on the PC and
the J4 connector on the ULTRA 100 Series. A simple 3 wire cable
is depicted in the figure below.
2. Connect a Motor/Feedback cable from the motor to the J2 connec-
tor on the drive.
3. Connect a Power cable from the motor to TB1 (terminals R, S, T
and
) on the drive.
4. Connect the Master Encoder to the drive as shown in the diagram.
5. Connect a jumper wire with a switches between the following
pins:
• J1-20 (ENABLE) and J1-26 (I/O PWR)
• J1-32 (INPUT1) and J1-26 (I/O PWR)
• J1-21 (FAULT RESET) and J1-26 (I/O PWR).
These connections provide manual control for enabling or
disabling the drive and resetting faults. The figure below shows
the jumper, including normally open toggle switches.
6. Connect an external 12 to 24 VDC power source for powering I/O
to J1-5 (I/O PWR) and J1-6 (I/O COM).
7. Connect the drive to a single phase 100-240 VAC, 50/60 Hz power
source.