2 absolute specification (absolute reset), Absolute specification (absolute reset) – IAI America RCP2-CF User Manual
Page 97
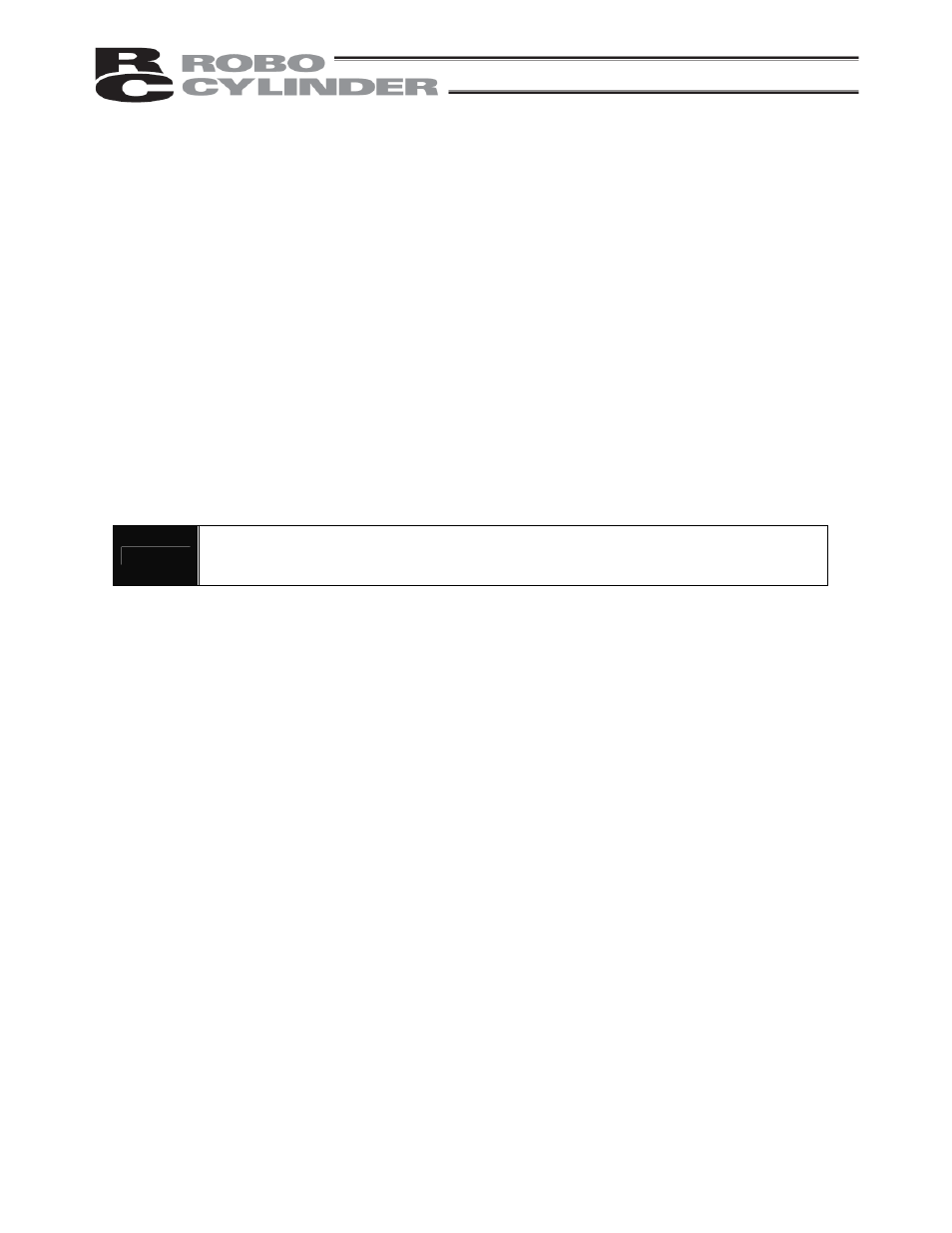
77
7.1.2
Absolute Specification (Absolute Reset)
(1) Connect the motor cable and encoder cable to the controller.
(2) Connect the host PLC to the PIO connector using the supplied flat cable.
(3) If two or more axes are connected, set the address of each axis using the address switch. For details, refer
to 9, “Controlling Multiple Controllers via Serial Communication.”
(4) Actuate an emergency stop or cut off the motor drive power.
(5) Connect the battery connector.
(6) Supply 24 VDC to the controller’s terminal block.
The alarm output signal (*ALM) will turn OFF, the alarm code output signals (PM8 to PM1) will indicate
“1101,” and the ALM lamp will illuminate.
The message “Absolute encoder error (2)” will be displayed on the PC/teaching pendant, if connected.
Also, a pause signal (*STP) is input from the PLC (if this signal is enabled).
(7) Confirm that the slider or rod is not contacting the mechanical end.
If the slider or rod is contacting the mechanical end, or when the slider/rod is not contacting the mechanical
end but is located near the home, move the slider/rod away from the home.
If the actuator is equipped with a brake, move the slider/rod after turning ON the brake release switch to
forcibly release the brake. At this time, exercise caution not to allow the load to drop suddenly due to its
own weight. Your hand may be caught by the dropped load or the robot hand or load itself may be damaged.
If the screw lead is short and the actuator cannot be moved by hands, change the setting of parameter No.
28, “Direction of excitation phase signal detection” to the direction opposite to the mechanical end.
Warning
If the servo is turned ON while the slider/rod is contacting the mechanical end, excitation
phase detection may not be performed correctly and an abnormal operation or excitation
detection error may result.
(8) Connect a PC or teaching pendant and set the following parameters as the minimum initial settings:
Parameter No. 15, “Pause input disable selection”
Parameter No. 21, “Servo ON input disable selection”
Parameter No. 25, “PIO pattern selection”
Parameter No. 27, “Movement command type” (when “4 points” is selected)
For details, refer to 8, “Parameters.”
(9) Reset the alarm.
Using the teaching pendant
• On the RCA-T/RCA-E, press the BEGIN/END key.
• On the RCB-J, press the Stop key.
Using the PC software
Select an applicable position data in the main window, and then click the [Alarm] button.
Issuing a command from the PLC
• If the PIO pattern is set to “0: [Conventional],” input a start signal (CSTR) for 6 msec or longer.
• If the PIO pattern is set to a value other than “0: [Conventional],” input a reset signal (RES) for 6 msec
or longer.
The message “Absolute encoder error (2)” will be cleared.
The alarm output signal (*ALM) will turn ON and the alarm code output signals (PM8 to PM1) will turn
OFF.