IAI America RCP2-CF User Manual
Page 96
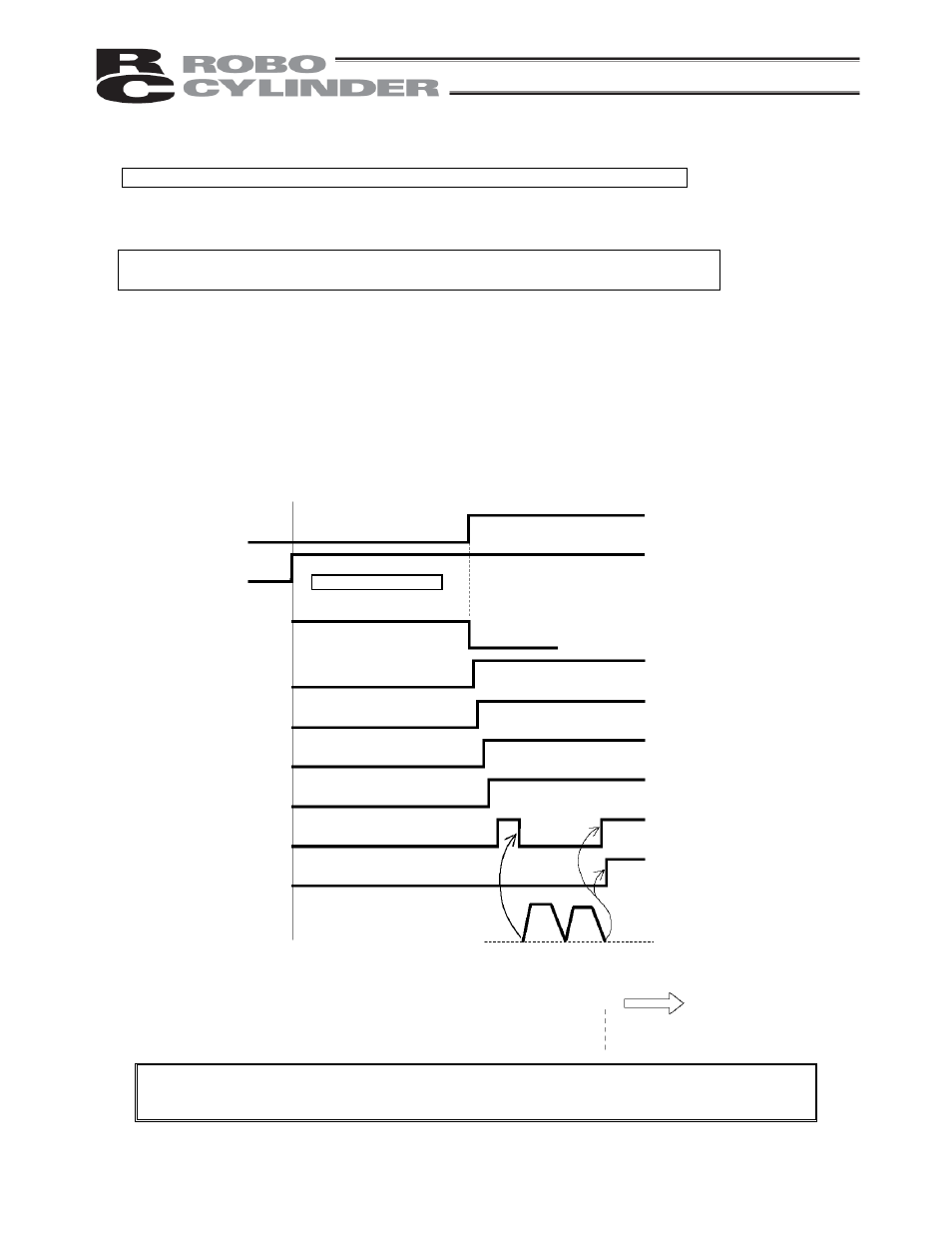
76
Overview of operation on the PC software
Select an applicable position data in the main window, and then click the [Home] button.
For details, refer to the operation manual for the teaching pendant or PC software.
Issuing a command from the PLC
Perform signal processing appropriate for the selected PIO pattern by referring to 7.2.1, “Standard
Specification.”
Issue a command after confirming that the position complete signal (PEND) has
turned ON.
If home return cannot be performed, confirm that the *pause signal and servo ON signal are ON and that
the safety circuit is released, and also check if any error message is displayed.
(11) Set the target position, speed, acceleration/deceleration, positioning band and other data in the position
table. For details on how to set these data, refer to the operation manual for the teaching pendant/PC
software.
Now, automatic operation can be performed via PLC link.
Timing chart at startup
Note: If parameter No. 25 (PIO pattern) is set to “0: [Conventional],” “2: [64-point positioning]”
or “5: [4 points],” the servo ON input and ready output are not provided.
Safety circuit condition
24-VDC power ON
ALM lamp
*Pause input
(STP)
Servo ON input
(SON)
RUN lamp
Ready output
(SRDY)
Position complete output
(PEND)
Home return completion output
(HEND)
Home return operation
Emergency stop is actuated or
motor drive power is cut off
Emergency stop is not actuated
or motor drive power is supplied
Initial parameter settings
Pause is cancelled
Creation of position table using the
teaching pendant or PC operation
Lit
Ho
me
p
o
s
ition
M
e
chani
cal
en
d
S
ta
rt
of
mo
ve
men
t