2) operation-cancellation level alarms, Operation-cancellation level alarms – IAI America RCP2-CF User Manual
Page 146
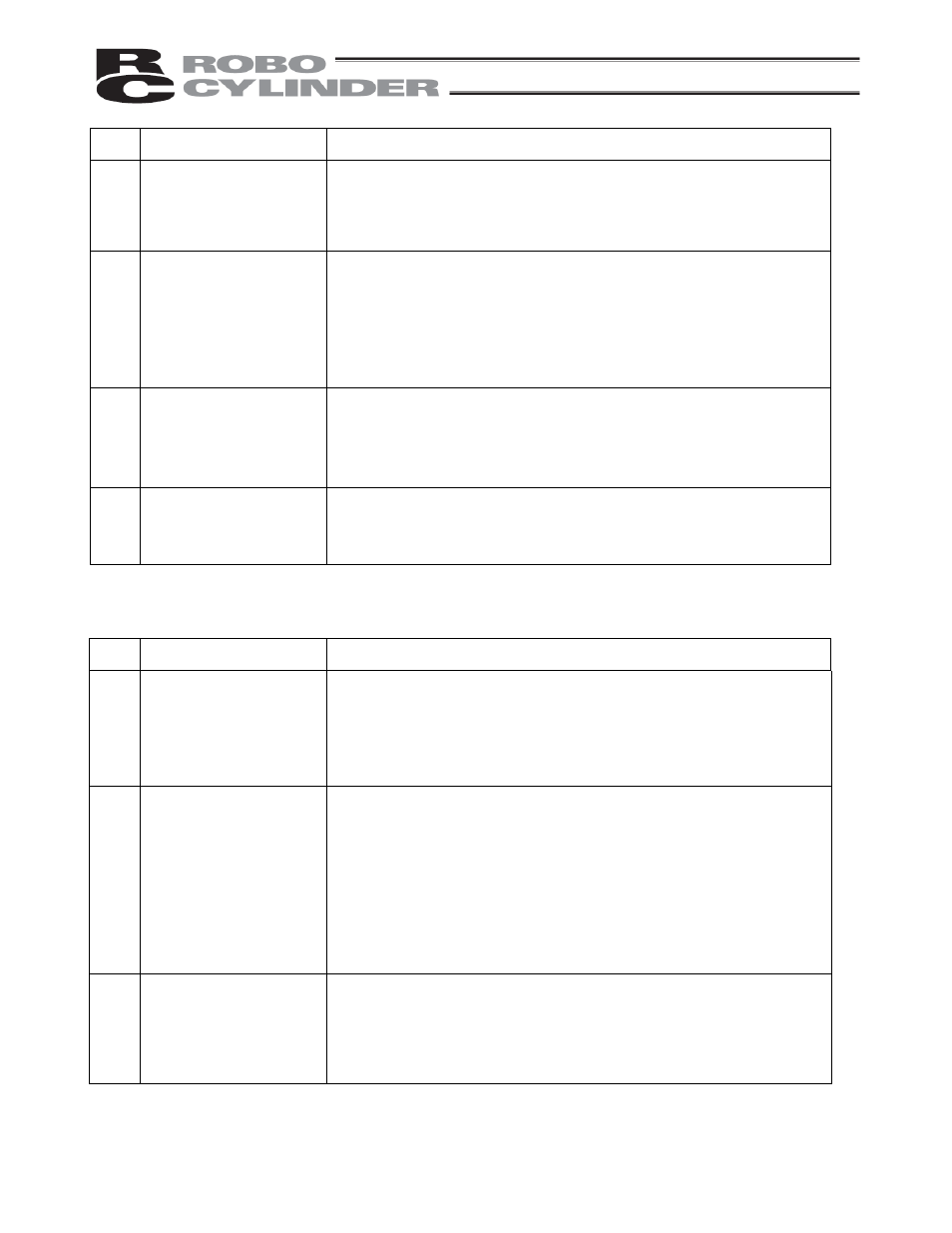
126
Code Error
name
Cause/Action
76
Soft reset during servo
ON
Cause: A soft reset command was sent while the servo was ON during
an operation by serial communication.
(PIO commands are excluded.)
Action: Send a soft reset command after confirming that the servo is
OFF.
77 Movement
command
during teaching
Cause: A position movement command was entered from a PC or
teaching pendant while the teaching mode was selected.
(Only the JOG inputs are enabled in the teaching mode.)
Action: Switch to the normal mode before entering a position
movement command.
(Turn OFF the MODE input signal and check if MODES is
OFF.)
78
EEPROM written during
teaching
Cause: Data was written from the PC or teaching pendant
simultaneously while the MODE signal was being input from
the PLC (teaching mode).
Action: Do not edit data from the PC or teaching pendant
simultaneously while a command is being issued from the PLC.
7A
ABS data backup battery
voltage low warning
Cause: The battery voltage was 4.4 V or below when the power was
input.
Action: Supply the power for at least 48 hours to charge the batteries.
(Moving the actuator will not affect the process of charging.)
(2) Operation-cancellation level alarms
Code Error
name
Cause/Action
B0
Bank 30 data error
Cause: Data in the parameter area is outside the input range or invalid.
(This alarm will not generate in normal parameter input
operation, but may occur during serial communication using
the PLC’s communication module.)
Action: Transfer data after confirming that the parameter values are
valid.
B1
Bank 31 data error
Cause: [1] A movement command was issued by selecting a number
to which no position data was registered.
[2] Position data value exceeds the soft limit setting.
[3] The timing of start signal is varied or too early.
Action: [1] Revise the sequence in such a way that unregistered
position numbers will not be selected.
[2] Change the position data to a value inside the soft limit
settings.
[3] The minimum timer setting may not be recognized
depending on the PLC. Pay attention to the timer setting.
BE
Home return timeout
Cause: Home return does not complete within the period set in the
applicable system parameter after the start of home return
operation.
(This alarm will not generate in normal operation.)
Action: The combination of controller and actuator may be wrong.
Please
contact
IAI.