HEIDENHAIN TNC 335 Technical Manual User Manual
Page 21
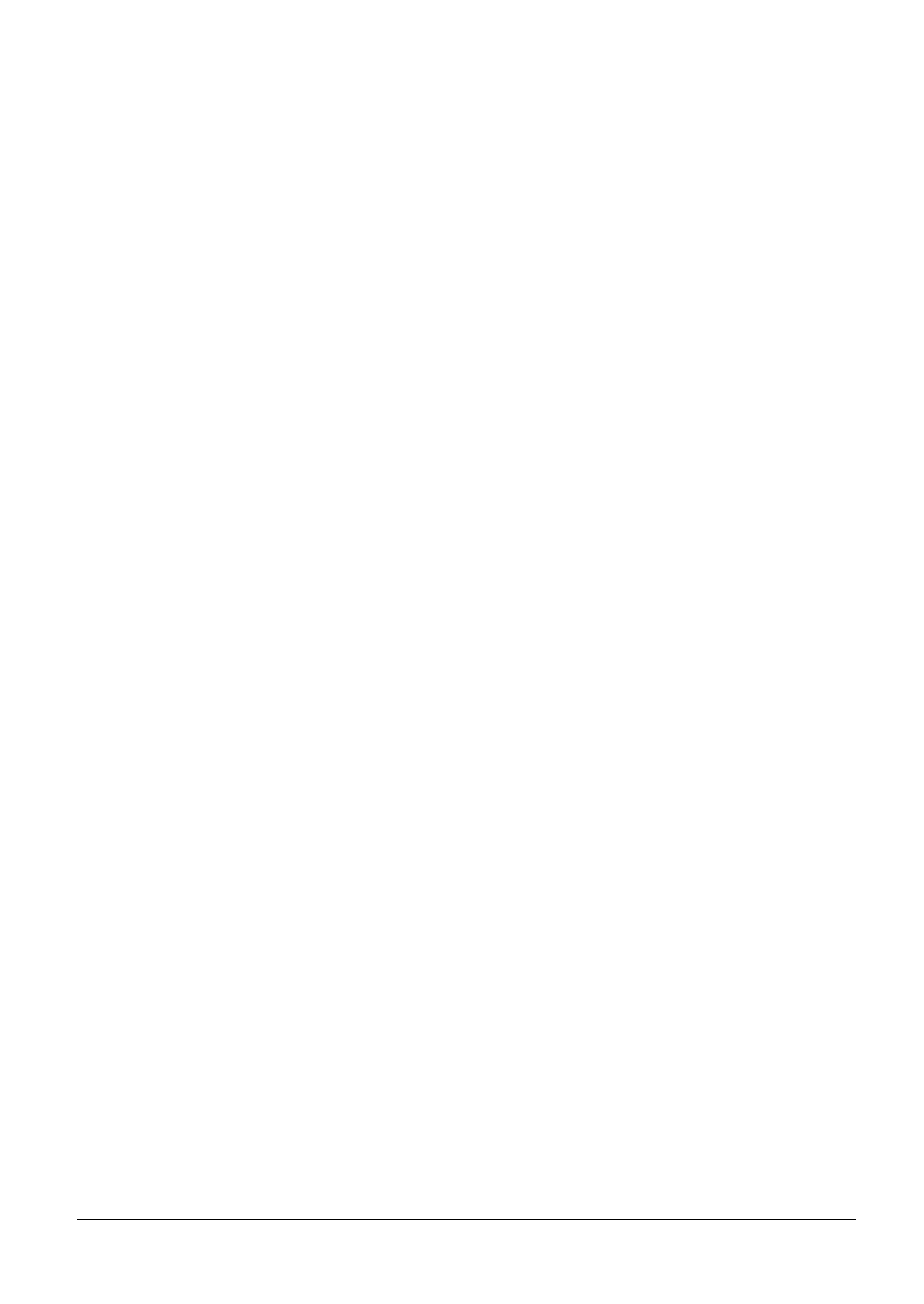
1-6
TNC 360/TNC 335
Update information No. 1
9/93
Potential errors:
A non-existent axis was transferred.
Call:
PS
B/W/D/K
CM9122
PL
B/W/D
Bit 0: 1= Axis is auxiliary axis
Bit 1: 1= Axis has traversed the reference point
Bit 2: 1= Axis is positioned
Bit 3: 1= Direction of motion is negative
Bit 4: 1= A positioning error has occurred
Error status after call: M3171
= 0: Status was transferred
= 1: Faulty execution
•
PLC MODULE 9123
Passing over the reference point of an auxiliary axis
The module starts positioning in a preset direction, which continues until a reference point is
found or the positioning is canceled with module 9121.
Conditions:
The given axis must be activated via MP10 and configured as an auxiliary axis via MP60.
The values for rapid traverse, analog voltage for rapid traverse, acceleration, etc., must be set
in the machine parameters.
There is no checking for violations of the limit switch ranges!
The axis must be stationary. If the axis is already moving, the positioning must be canceled
beforehand with module 9121.
The feed rate override is not included in the calculation.
The state "reference point not yet traversed" is set for the axis.
A reference point that already exists in this axis is erased, but not the numerical value of the
axis. This is not reinitialized until the reference point is found.
If modules 9120, 9121 and 9122 are called several times during a PLC scan, only the last
instruction is executed.
If a "positioning error" status was set in this axis it is erased.
The positioning is stopped as soon as the reference point is reached. Since the axis must
decelerate before it can stop, it comes to rest behind the reference point in the direction of
motion.