HEIDENHAIN TNC 335 Technical Manual User Manual
Page 14
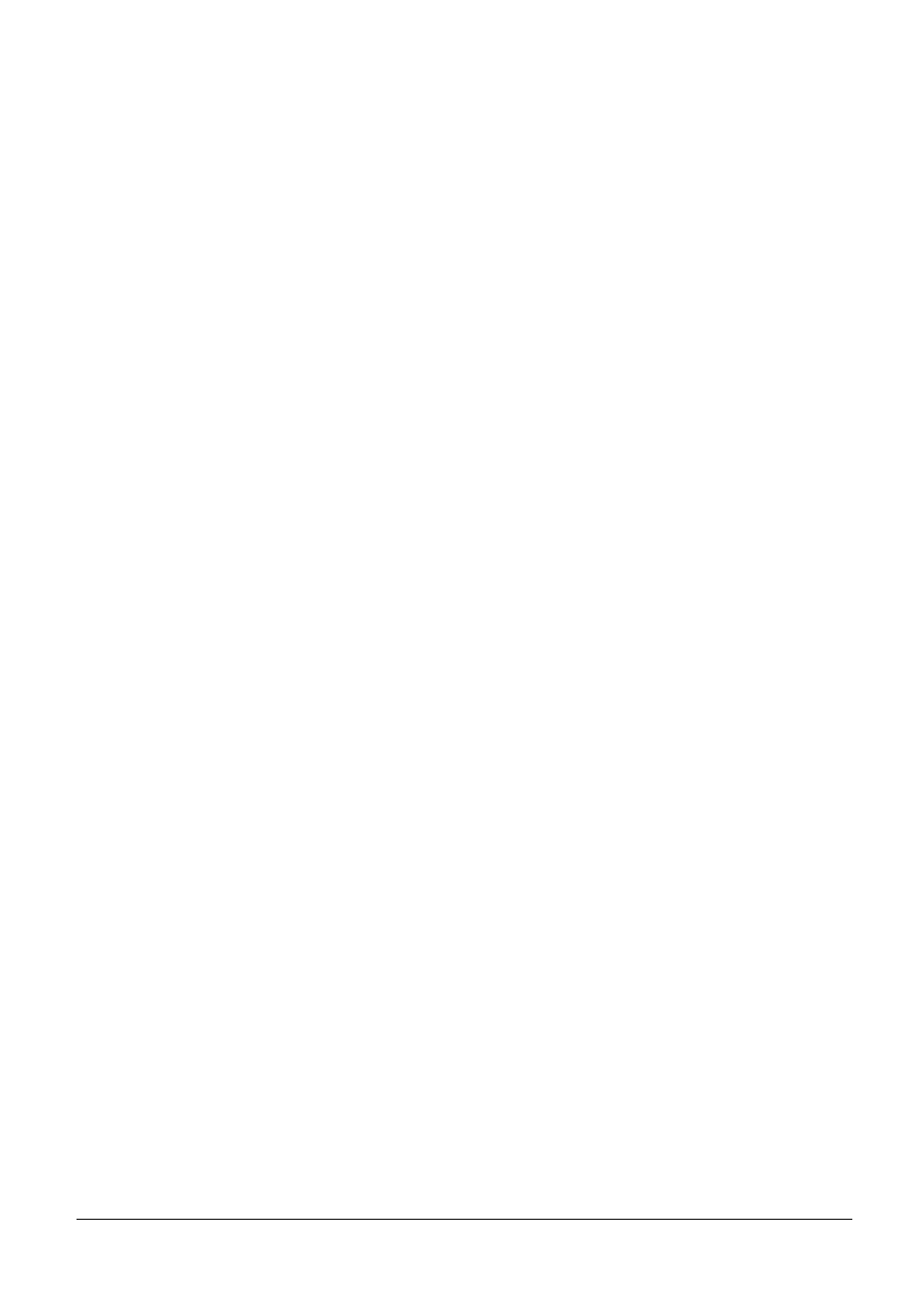
1-2
TNC 360/TNC 335
Update information No. 3
1/94
•
The new PLC module 9124 makes it possible to set a feed rate override value for secondary
axes. The override value can lie between 0% and 100% (resolution 0.01 %) and must be
transferred as a whole number (0 to 10 000). It can be set before the beginning of a movement
or during the movement of an auxiliary axis. If the control is reset, the NC presets an override
value of 100%.
Call :
PS B/W/D/K
PS B/W/D/K
CM 9124
PL B/W/D
0: Override was set
1: Invalid axis was entered
2: Axis is not defined as auxiliary axis
3: Override value is invalid
Error status after call: M3171
= 0 : Override was set
= 1 : Error condition see above
If more than one of the PLC modules 9120/9121/9123 for controlling the movement of auxiliary
axes is called within one PLC scan, only the last called PLC module is executed. The module
9124 can be called in addition to the above modules within one PLC scan, but it will always
become effective after the other module.
•
In PLC module 9036 (transferring PLC status information to the NC) the interpolation factor can
be set for all axes by transferring the value 4 or 5.
•
The PLC can inhibit the reference pulse for specific axes through Word W608 (bit-
coded,....4zyx).
Bit = 1 : Reference pulse is not evaluated
Bit = 0 : The next reference pulse is evaluated
•
By setting marker M2615 the reference mark of the spindle is evaluated again. The marker is
reset by the NC.
•
Marker 2510 fixes the spindle potentiometer setting at 100%. Marker M2511 has the same
effect on the feed rate potentiometer.
•
CC blocks in OEM cycles are effective only locally and are not transferred into the calling
program.