4 optical sensor, 1 safety circuit integrity levels, 2 optical sensor requirements – Banner SC22-3E Safety Controller with Ethernet User Manual
Page 98
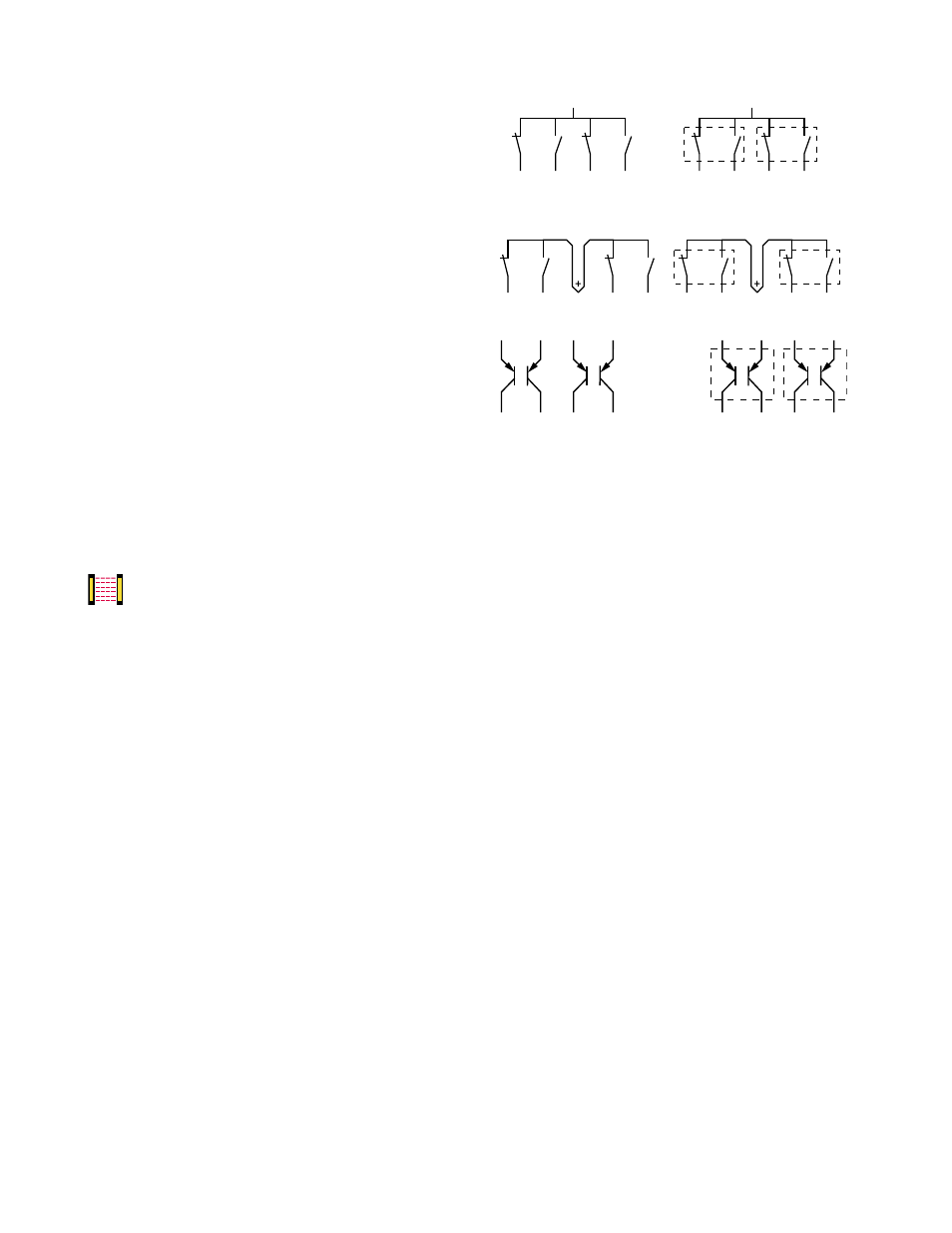
2x Complementary (4 or 5 terminals): This circuit can meet ISO
13849-1 category 4 requirements, depending on the safety rating
and the installation of the switches. This circuit can detect a short
circuit between channels. A coded magnetic switch would typically
use this style. In the guard-closed condition (as shown), a short
across the closed contact can cause the response time to increase
based on the debounce time. In this situation, the response time
could be longer than specified, based on the (selected) debounce
time, see section
4.3.2 Safety Input Device Properties
on page 28.
24V
24V
Two coded magnetic switches
mounted on a single guard can meet
Category 4.
2x Complementary (PNP device): This circuit can meet ISO
13849-1 category 4 requirements depending on the safety rating
and the installation of the switches. This circuit can detect a short
circuit between channels. In the guard-closed condition (as
shown), a short across the closed contact can cause the response
time to increase based on the debounce time. In this situation, the
response time could be longer than specified, based on the (selec-
ted) debounce time, see section
4.3.2 Safety Input Device Proper-
on page 28.
OFF
ON
OFF
ON
OFF
ON
OFF
ON
10.4 Optical Sensor
The Safety Controller safety inputs may be used to monitor optical-based devices that use light as a means of detection.
10.4.1 Safety Circuit Integrity Levels
Requirements vary widely for the level of control reliability or safety category per ISO 13849-1 (EN954-1) in the application of optical
safeguarding. While Banner Engineering always recommends the highest level of safety in any application, it is the responsibility of the
user to safely install, operate and maintain each safety system and comply with all manufacturer instructions and all relevant laws and
regulations.
The safety performance (integrity) must reduce the risk from identified hazards as determined by the machine’s risk assessment. See
section
10.1 Safety Circuit Integrity and ISO 13849-1 (EN954-1) Safety Circuit Principles
on page 90 for guidance if the requirements as
described by ISO 13849-1 (EN954-1) are to be implemented.
In addition to the requirements stated in this section, the design and installation of the optical safeguarding device should comply with
ANSI B11.19 or IEC61496 (all parts).
10.4.2 Optical Sensor Requirements
When used as safeguarding, these devices are described by IEC61496-1/-2/-3 as “active Opto-electronic protective device” (AOPD) and
“active opto-electronic protective device responsive to diffuse reflection” (AOPDDR).
AOPDs include safety light screens (curtains) and safety grids and points (multiple-/single-beam devices). These devices are described
as meeting Type 2 or Type 4 design requirements; a Type 2 device is allowed to be used in a Category 2 application, per ISO 13849-1,
and a Type 4 device can be used in a Category 4 application.
AOPDDRs can also be area or laser scanners. The primary designation for these devices is a Type 3, for use in up to Category 3 appli-
cations.
SC22-3/-3E Safety Controller Instruction Manual
98
www.bannerengineering.com - tel: 763-544-3164
P/N 133487 rev. C