Category 2 interlocked guard circuit – Banner SC22-3E Safety Controller with Ethernet User Manual
Page 95
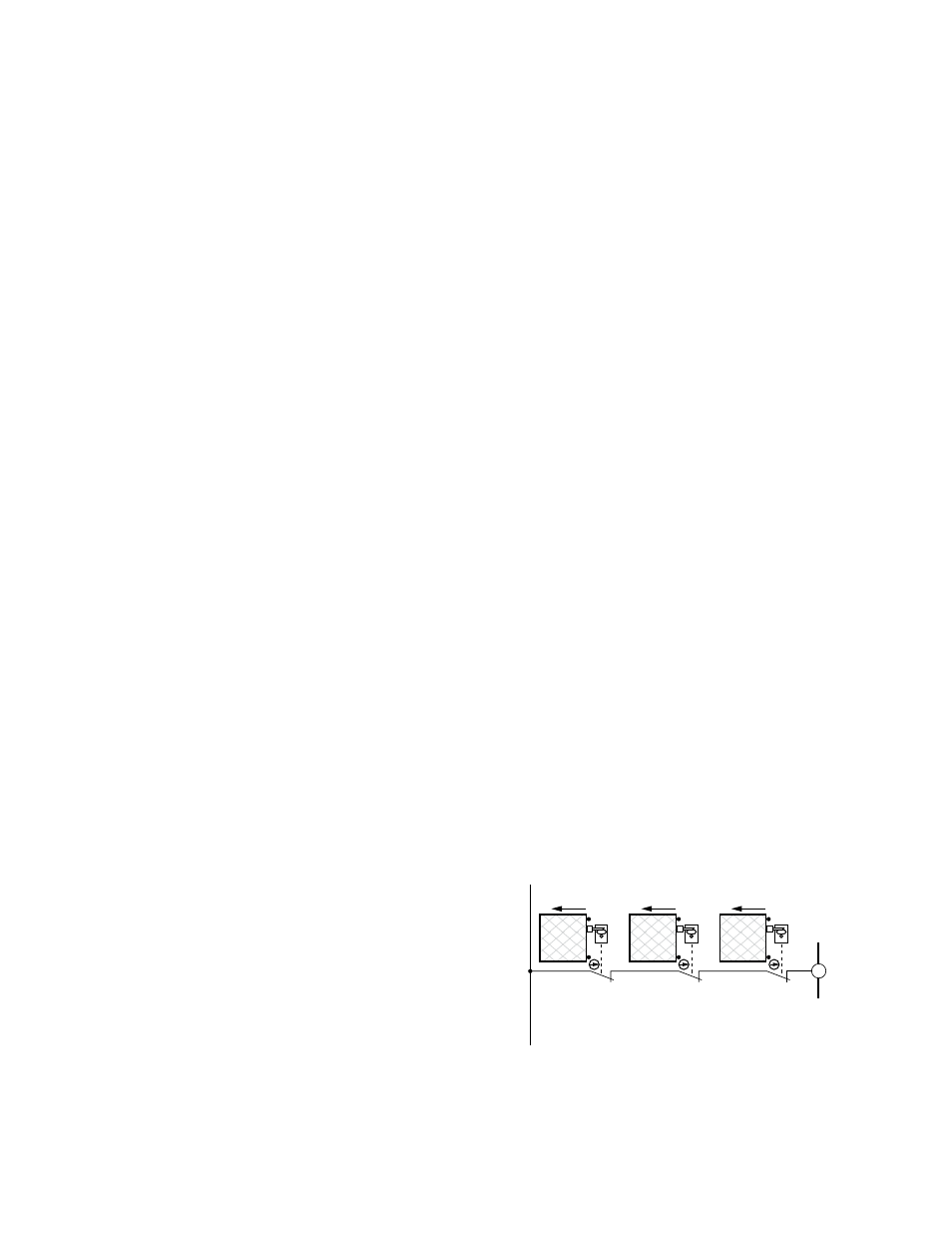
The switch and its magnet must be mounted a minimum distance from any magnetized or ferrous materials for proper operation. If either
the switch or magnet is mounted on a material that can be magnetized (a ferrous metal, such as iron), the switching distance will be
affected. This distance will be stated by the manufacturer.
Monitoring Series-Connected Safety Interlock Switches
When monitoring two individually mounted safety switches (as shown in the Category 2 circuit figure), a faulty switch will be detected if it
fails to switch as the guard opens. In this case, the Controller will de-energize its Safety Outputs (OSSDs) and disable its reset function
until the input requirements are met (i.e., the faulty switch is replaced). However, when multiple safety interlock switches are series-
connected, the failure of one switch in the system may be masked or not be detected at all (refer to Category 3 and 4 circuit figures).
Series-connected interlock switch circuits may not meet OSHA Control Reliability or ISO 13849 (EN954-1) Safety Category 4 require-
ments because of the potential of an inappropriate reset or a potential loss of the safety stop signal. This is due to the typical inability to
fault exclude the failure of the safety interlock switch. A multiple connection of this type should not be used in applications where
loss of the safety stop signal or an inappropriate reset can lead to serious injury or death. The following two scenarios assume two
positive-opening safety switches on each guard, both connected in series to switches of a second guard:
1. Masking of a failure. If a guard is opened but a switch fails to open, the redundant safety switch will open and cause the Controller
to de-energize its outputs. If the faulty guard is then closed, both Controller input channels also close, but because one channel did
not open, the Controller will not reset. However, if the faulty switch is not replaced and a second “good” guard is cycled (opening
and then closing both of the Controller’s input channels), the Controller considers the failure to be corrected. With the input require-
ments apparently satisfied, the Controller allows a reset. This system is no longer redundant and, if the second switch fails, may
result in an unsafe condition (i.e., the accumulation of faults resulting in loss of the safety function).
2. Non-detection of a failure. If a good guard is opened, the Safety Controller de-energizes its outputs (a normal response). But if a
faulty guard is then opened and closed before the good guard is re-closed, the faulty guard is not detected. This system also is no
longer redundant and may result in a loss of safety if the second safety switch fails to switch when needed.
The systems in either scenario do not inherently comply with the safety standard requirements of detecting single faults and preventing
the next cycle. In multiple-guard systems using series-connected safety switches, it is important to periodically check the functional integ-
rity of each interlocked guard individually. Operators, maintenance personnel, and others associated with the operation of the ma-
chine must be trained to recognize such failures and be instructed to correct them immediately.
Open and close each safeguard separately while verifying that the Controller outputs operate correctly throughout the check procedure.
Follow each safeguard closure with a manual reset, if needed. If a contact set fails, the Controller will not enable its reset function. If the
Controller does not reset, a switch may have failed; that switch must be immediately replaced.
This check must be performed and all faults must be cleared, at a minimum, during periodic checkouts. If the application can not ex-
clude these types of failures and such a failure could result in serious injury or death, then the series connection of safety
switches must not be used.
Series Connection and Safety Circuit Integrity Considerations
Category 2 Interlocked Guard Circuit
A single-channel interlocked guard application typically provides a
Category 2 level of circuit performance, because a short circuit
could cause loss of safety function. The principle of fault exclusion
must be incorporated into the design and installation to either elim-
inate, or reduce to an acceptable (minimal) level of risk, the possi-
bility of faults that can result in loss of the safety function.
Open
+24V dc
Open
Open
Figure 60. Category 2 Interlocked Guard Circuit
SC22-3/-3E Safety Controller Instruction Manual
P/N 133487 rev. C
www.bannerengineering.com - tel: 763-544-3164
95