5 bypass function – Banner SC22-3E Safety Controller with Ethernet User Manual
Page 38
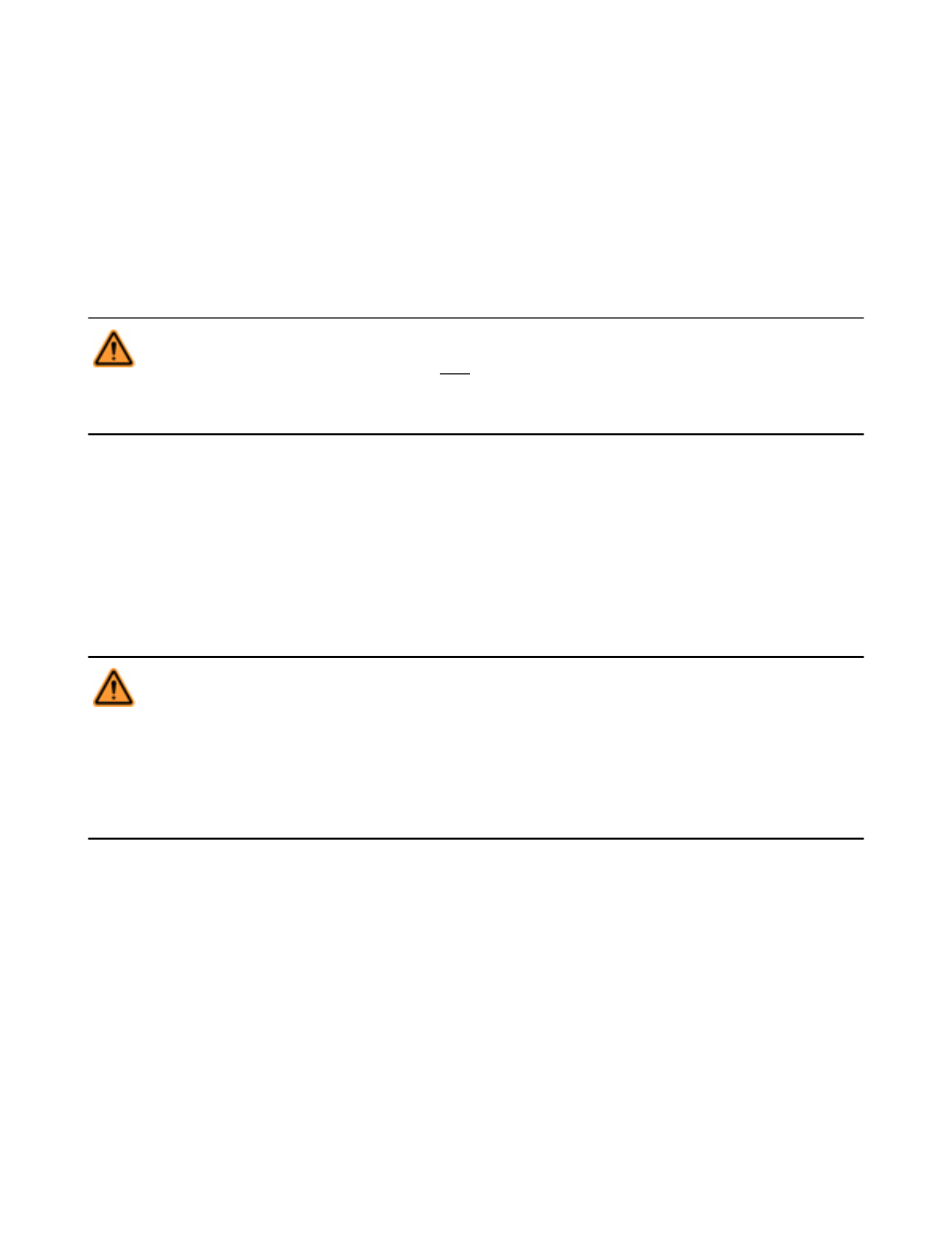
Directional Muting. As soon as two mute sensor pairs are configured and mapped to a muteable Safety Input, an advanced setting
option appears in the PCI to provide the option of directional muting. Check the box "Enable Directional Muting," then select the muting
sensor pair to be blocked first. The Controller requires sensor pair 1 to be blocked first, then the safeguard, then sensor pair 2 (all within
the configured time limits) in order for the mute to take place.
Mute Sensor Debounce Time. The input debounce time, accessible under the "Advanced settings" in the Mute Sensor Pair properties
window, can be used to extend a mute cycle after a mute sensor signal is removed. By configuring the "closed-to-open" debounce time,
the mute cycle can be extended up to 1.5 seconds (1500 ms) to allow the Safety Input Device to re-energize its outputs (turn ON). The
start of the mute cycle can also be delayed, by configuring the "open-to-closed" debounce time.
Mute on Power-Up Function. If configured, the Mute on Power-Up function will initiate a mute cycle after power is applied to the Safety
Controller if the muted safety inputs are active (Run state or closed), and either M1-M2 or M3-M4 (but not all four) are signaling a muted
condition (e.g., active or closed).
WARNING: . . . Mute on Power-Up
The Mute on Power-Up function should be used
only in applications where:
• Muting the System (M1 and M2 closed) when power is applied is required, and
• Using it does not, in any situation, expose personnel to any hazard.
Mute on Power-Up Disabled. When the mute on power-up option is disabled, the Controller will not go into a mute cycle, even if the
conditions for a valid mute cycle are fulfilled at power-up.
Mute on Power-Up Enabled. When the Mute on Power-Up option is enabled, the Controller will go into a mute cycle if the conditions for
a valid mute cycle are fulfilled at power-up. Specific valid mute signal conditions must be present for a mute cycle to be initiated and
maintained.
If Auto Power-Up is configured, the Controller allows approximately 2 seconds for the input devices to become active (closed) to accom-
modate systems that may not be immediately active at power-up. If Manual Power-Up is configured and all other conditions are satisfied,
the first valid system reset after the muted safety inputs are active (Run state or closed) will result in a mute cycle. The Mute On Power-
up function should only be used if safety can be assured when the mute cycle is expected, and the use of this function is the
result of a risk assessment and is required by that particular machine operation.
WARNING: . . . Mute and Bypass
Mute and Bypass operations must be done in a way that minimizes personnel risk. Implement the following when cre-
ating mute and bypass applications:
• Guard against unintended stop signal suspension by using one or more diverse-redundant mute sensor pairs or a
dual channel key-secured bypass switch.
• Set reasonable time limits (no longer than needed) for the mute and bypass functions.
Failure to follow these rules could lead to an unsafe condition that could result in serious injury or death.
See section
on page 116 for more information.
4.6.5 Bypass Function
The safety device bypass is a manually activated and temporary suspension of one or more safety input stop signals when no immediate
hazard is present. Bypass switches can be mapped to one or more of the following safety input devices:
• Safety gate (interlocking) switches
• Optical sensors
• Two-hand control devices
• Safety mats
• Protective stop
When the bypass switch signal changes to the Bypass (Run) state, it will turn ON or keep ON all the Safety Outputs that are controlled by
the bypassed safety input devices only if all other non-bypassed safety devices that are mapped to these Safety Outputs are in the Run
state.
SC22-3/-3E Safety Controller Instruction Manual
38
www.bannerengineering.com - tel: 763-544-3164
P/N 133487 rev. C