7 emergency stop push buttons, 1 safety circuit integrity levels – Banner SC22-3E Safety Controller with Ethernet User Manual
Page 106
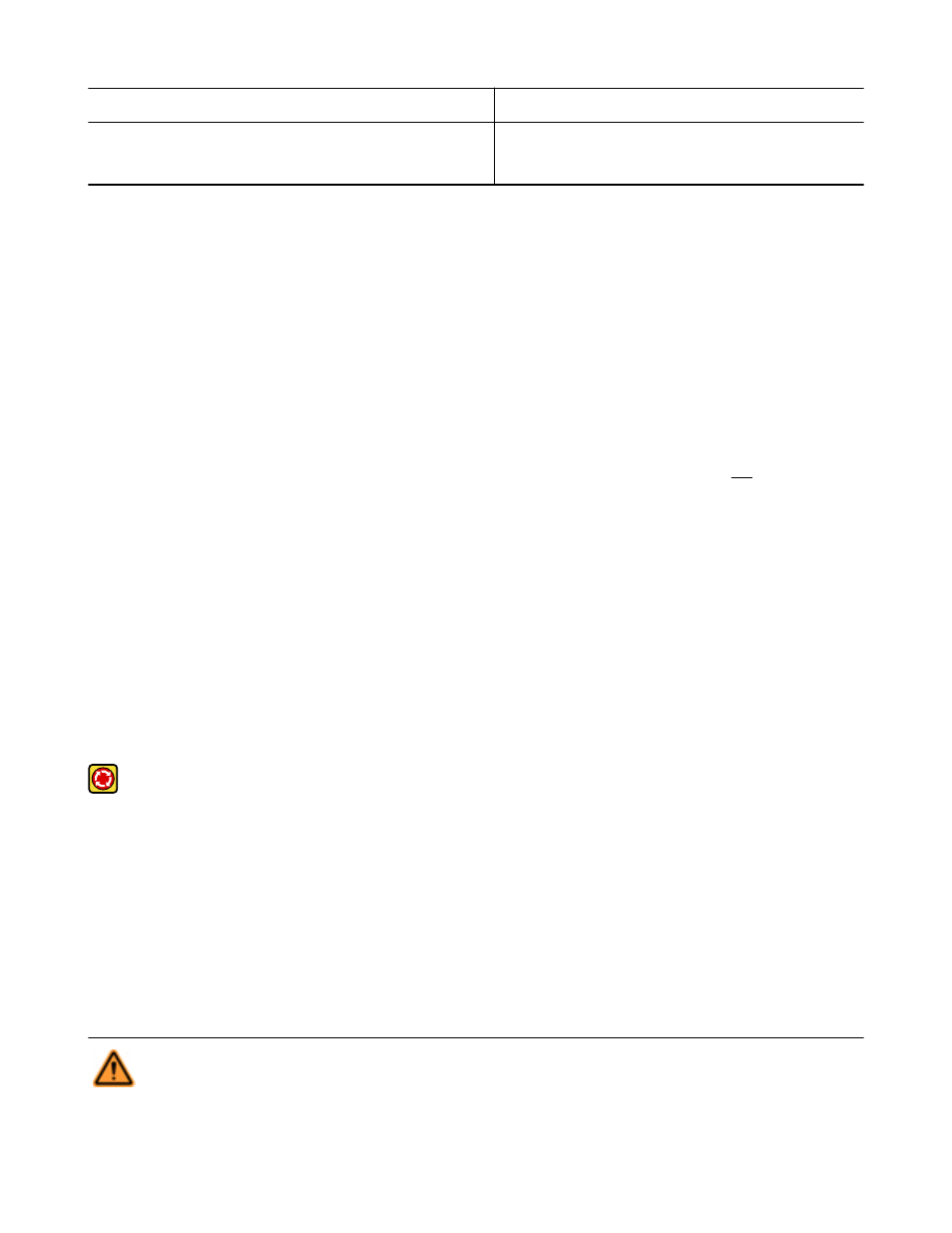
Formula for U.S. Installations
Formula for EU-Certified Installations
The formula used to calculate separation (safety) distance (Ds) is:
Ds = K x ( Ts + Tr ) + Dpf
The formula used to calculate minimum safety distance (S) is:
S = ( K x T ) + C
in both cases, where:
Ds = the separation (safety) distance in inches.
S = the minimum safety distance in millimeters.
K = the OSHA/ANSI and ISO 13855 hand speed constant of 1600 mm/second (63" per second) (see NOTE 1 below).
T = the overall stop time of the machine, measured from the actuation of the sensing function to the final ceasing of all motion (in es-
sence, T = Ts + Tr ).
Ts = the overall stop time of the machine, measured from the application of the “stop” signal to the final ceasing of all motion (including
stop times of all relevant control elements, and measured at maximum machine velocity) (see NOTE 2 below).
Tr = the response time of the safety mat system: the response time of the sensor(s), as stated by the manufacturer, plus the response
time of the Safety Controller as measured from the time a stop is signalled by the safety mat, after it was stepped on. (Controller default
response is 0.010 seconds, plus any additional closed-to-open debounce time.) If the debounce time is adjusted, the time in excess of 6
ms (default closed-to-open debounce time) must be added to the stated response; refer to Specifications, Section 2.2.)
Dpf = the added distance due to depth penetration factor: 1200 mm (48"), per ANSI B11.19.
C = the added distance due to depth penetration factor: 1200 mm (48"), per ISO 13855.
NOTES:
1. The hand-speed constant (K) has been determined by various studies, and although these studies indicate speeds of 1600mm/s
(63"/second), 2000 mm/s (79"/second), to more than 2540 mm/s (100"/second), they are not conclusive determinations. The em-
ployer should consider all factors, including the physical ability of the operator, when determining the value of K to be used.
2. Ts is usually measured by a stop-time measuring device. If the specified machine stop time is used, add at least 20% as a safety
factor to account for brake system deterioration. If the stop-time of the two redundant machine control elements is unequal, the
slower of the two times must be used for calculating the separation distance.
10.7 Emergency Stop Push Buttons
The Safety Controller safety inputs may be used to monitor emergency stop push buttons.
10.7.1 Safety Circuit Integrity Levels
Requirements vary widely for the level of control reliability or safety category per ISO 13849-1 (EN954-1) in the application of emergency
stops. While Banner Engineering always recommends the highest level of safety in any application, it is the responsibility of the user to
safely install, operate and maintain each safety system and comply with all relevant laws and regulations.
The safety performance (integrity) must reduce the risk from identified hazards as determined by the machine’s risk assessment. See
section
10.1 Safety Circuit Integrity and ISO 13849-1 (EN954-1) Safety Circuit Principles
on page 90 for guidance if the requirements as
described by ISO 13849-1 (EN954-1) are to be implemented.
In addition to the requirements stated in this section, the design and installation of the Emergency Stop device should comply with ANSI
NFPA79 or ISO 13850.
WARNING: . . . Emergency Stop Functions
Do not mute or bypass any Emergency Stop device. ANSI NFPA79 and IEC/EN 60204-1 require that the Emergency
Stop function remain active at all times. Muting or bypassing the Safety Outputs will render the emergency stop func-
tion ineffective.
SC22-3/-3E Safety Controller Instruction Manual
106
www.bannerengineering.com - tel: 763-544-3164
P/N 133487 rev. C