Photoelectric sensors (opposed mode), Positive-opening safety switches, Inductive proximity sensors – Banner SC22-3E Safety Controller with Ethernet User Manual
Page 118: 3 muting device hookup options
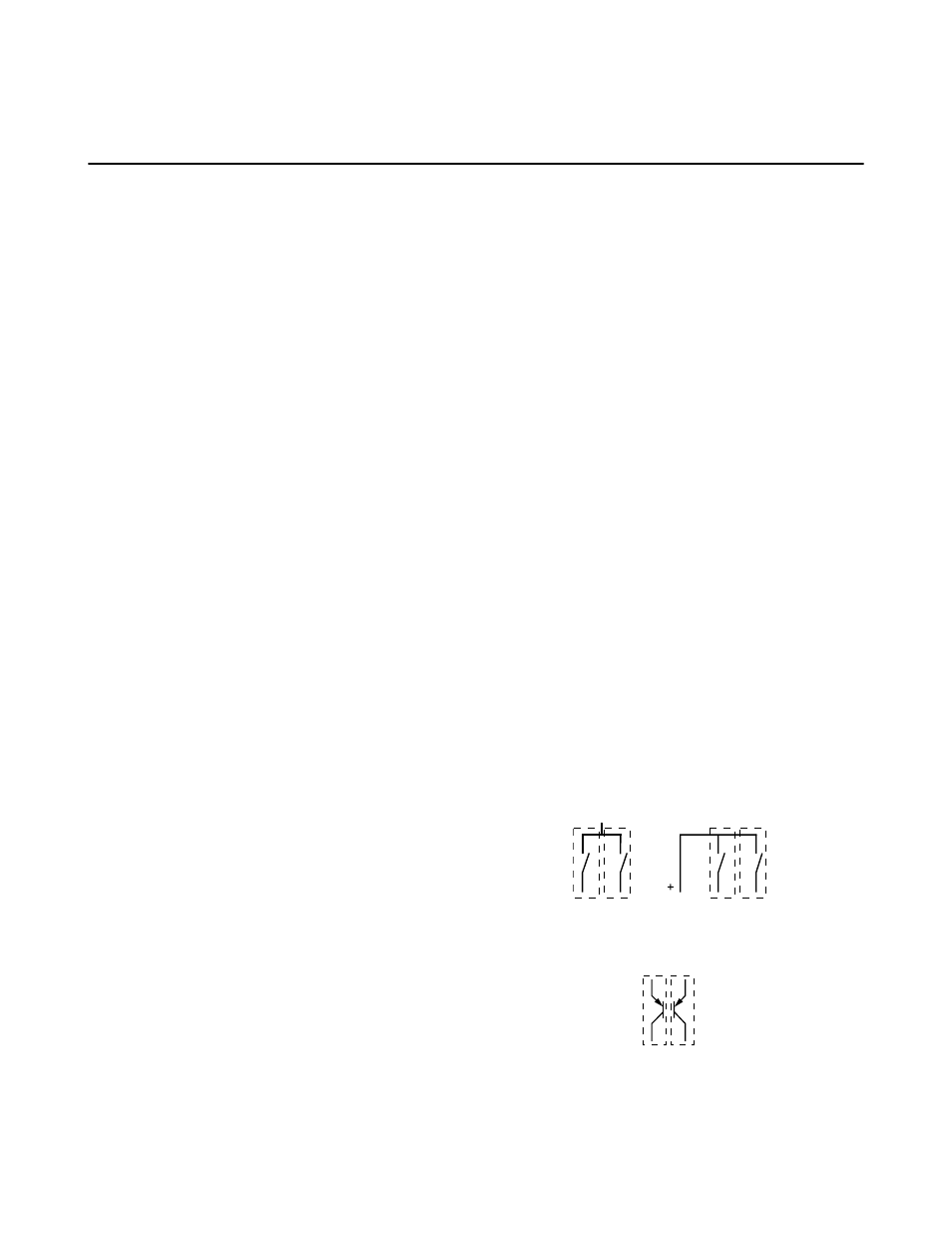
The user has the responsibility to satisfy all local, state, and national laws, rules, codes, and regulations relating to the use of
safety equipment in any particular application. It is extremely important to be sure that all appropriate agency requirements
have been met and that all installation and maintenance instructions contained in the appropriate manuals are followed.
Photoelectric Sensors (Opposed Mode):
Opposed-mode sensors, which initiate the muted condition when the beam path is blocked, should be configured for dark operate (DO)
and have open (non-conducting) output contacts in a power OFF condition. Both the emitter and receiver from each pair should be pow-
ered from the same source to reduce the possibility of common mode failures.
Photoelectric Sensors (Polarized Retroreflective Mode):
The user must ensure that false “proxing” (activation due to shiny or reflective surfaces) is not possible. Banner “LP” sensors with linear
polarization can greatly reduce or eliminate this effect.
Use a sensor configured for Light Operate (LO or N.O.) if initiating a mute when the retroreflective target or tape is detected (e.g., home
position). Use a sensor configured for Dark Operate (DO or N.C.) when a blocked beam path initiates the muted condition (e.g., entry/
exit). Both situations must have open (non-conducting) output contacts in a power OFF condition.
Positive-Opening Safety Switches:
Two (or four) independent switches, each with a minimum of one closed safety contact to initiate the mute cycle, are typically used. An
application using a single switch with a single actuator and two closed contacts could result in an unsafe situation.
Inductive Proximity Sensors:
Typically, inductive proximity sensors are used to initiate a muted cycle when a metal surface is detected. Due to excessive leakage
current causing false ON conditions, two-wire sensors are not to be used. Only three- or four-wire sensors that have discrete PNP or
hard-contact outputs that are separate from the input power should be used.
10.11.3 Muting Device Hookup Options
The Controller provides configuration options for the muting devices. One or two pairs of muting devices (typically sensors or switches)
must be used; these pairs are designated M1-M2 and M3-M4. In the circuit diagrams below, it is assumed that each contact or output
is being generated by an individual device for category 3 and category 4.
To meet category 4 requirements for the category 3 hookups shown, “design out” or otherwise eliminate the possibility of a
short circuit between muting sensors (input channels); see section
on page 92.
Dual-Channel (2 or 3 terminals): This circuit typically can meet
ISO 13849-1 category 2 or category 3 requirements depending on
the installation of the mute device(s). Dual-channel 3-terminal
hookups use pulse monitoring and can detect a short circuit to an-
other source of power. Both 2- and 3-terminal hookup can detect a
short between channels when the contacts are open if the short is
present longer than 2 seconds.
24V
Dual-Channel (PNP device): This circuit can meet ISO 13849-1
category 2 or category 3 requirements depending on the installa-
tion and the fault detection (e.g., short circuit) capabilities of the
mute device. The Safety Controller does not provide short circuit
detection in this configuration.
OFF
OFF
SC22-3/-3E Safety Controller Instruction Manual
118
www.bannerengineering.com - tel: 763-544-3164
P/N 133487 rev. C