Dual feedback speed ratio, Dual feedback position discrepancy tolerance – Rockwell Automation 2094-EN02D-M01-S1 Kinetix 6200 and Kinetix 6500 Safe Speed Monitoring Safety Reference Manual User Manual
Page 51
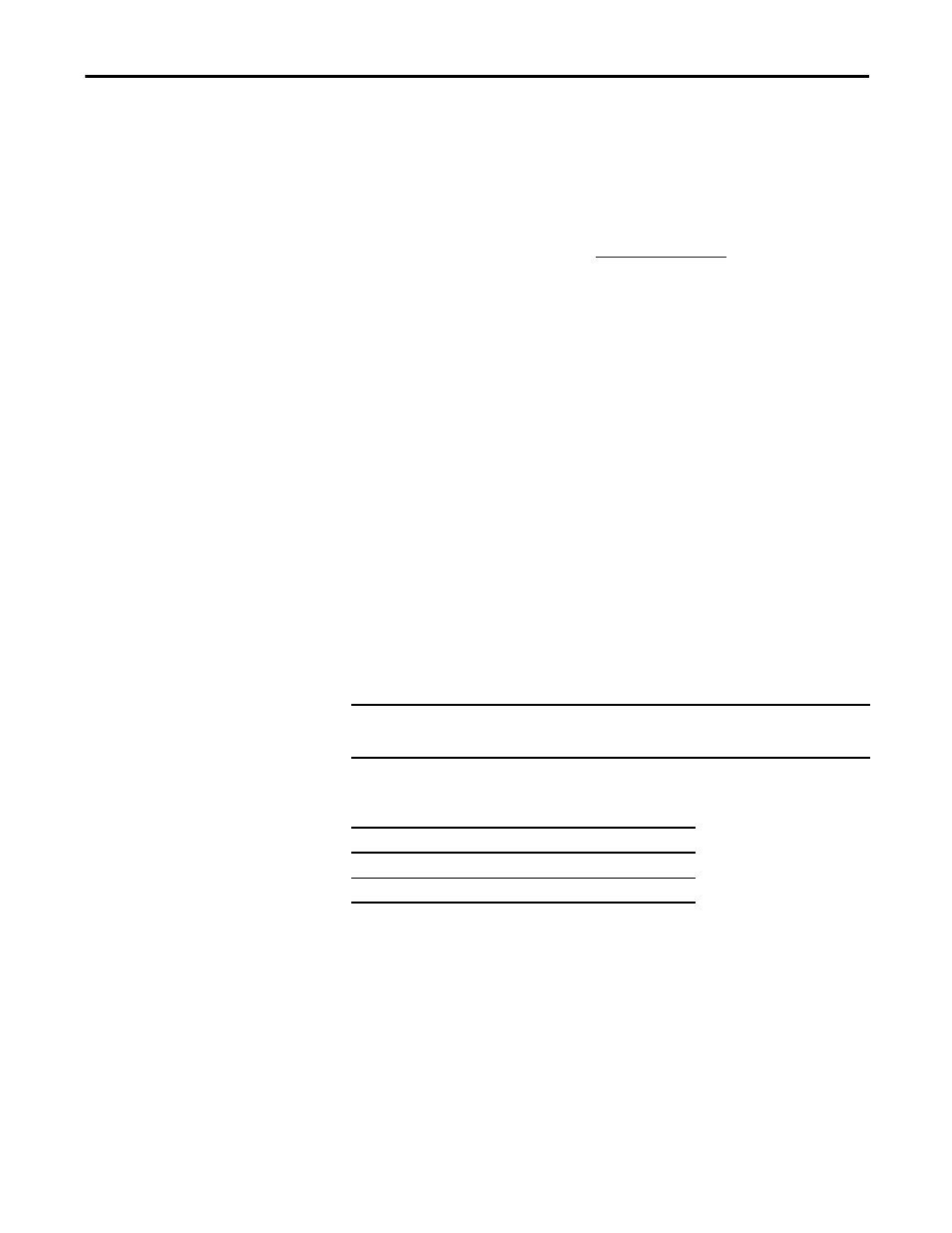
Rockwell Automation Publication 2094-RM001C-EN-P - May 2013
51
General Device and Feedback Monitoring Configuration
Chapter 5
Dual Feedback Speed Ratio
The Dual Feedback Speed Ratio, [Velocity Ratio] parameter, is defined as the
ratio of the expected speed of encoder 2 divided by the expected speed of encoder
1. This parameter configures the anticipated gearing between encoder 1 and
encoder 2.
If [Feedback Mode] equals Single Encoder, the only legal value for [Velocity
Ratio] parameter is 0.0.
If [Feedback Mode] is any Dual Encoder configuration, the range of legal values
for [Velocity Ratio] is from 0.0001…10,000.0.
For example, if encoder 2’s speed is expected to be 1000 revolutions per second
while encoder 1’s speed is expected to be 100 revolutions per second, then
configure the [Velocity Ratio] as 10.0.
The units used to measure encoder speed are configurable as either rotary (rev) or
linear (mm) units. Any combination of rotary and linear units for the two
encoders is allowed.
Dual Feedback Position Discrepancy Tolerance
The Dual Feedback Position Discrepancy Tolerance, [Position Discrepancy
Tolerance] parameter, defines the cumulative position discrepancy that is
tolerated between encoder 1 and encoder 2. The position discrepancy is defined
as position change relative to encoder 1.
This discrepancy checking is performed only while the [Feedback Mode]
parameter is equal to one of these values.
IMPORTANT
The relative position discrepancy difference is reset to zero at each Safe Stop
Reset.
[Feedback Mode] Parameter Settings
Dual encoder with speed and position discrepancy checking
Dual encoder with position discrepancy checking
Expected Speed of Encoder 2
Expected Speed of Encoder 1
=
Dual Feedback Speed Ratio
[Velocity Ratio] Parameter