Feedback monitoring, Feedback polarity – Rockwell Automation 2094-EN02D-M01-S1 Kinetix 6200 and Kinetix 6500 Safe Speed Monitoring Safety Reference Manual User Manual
Page 49
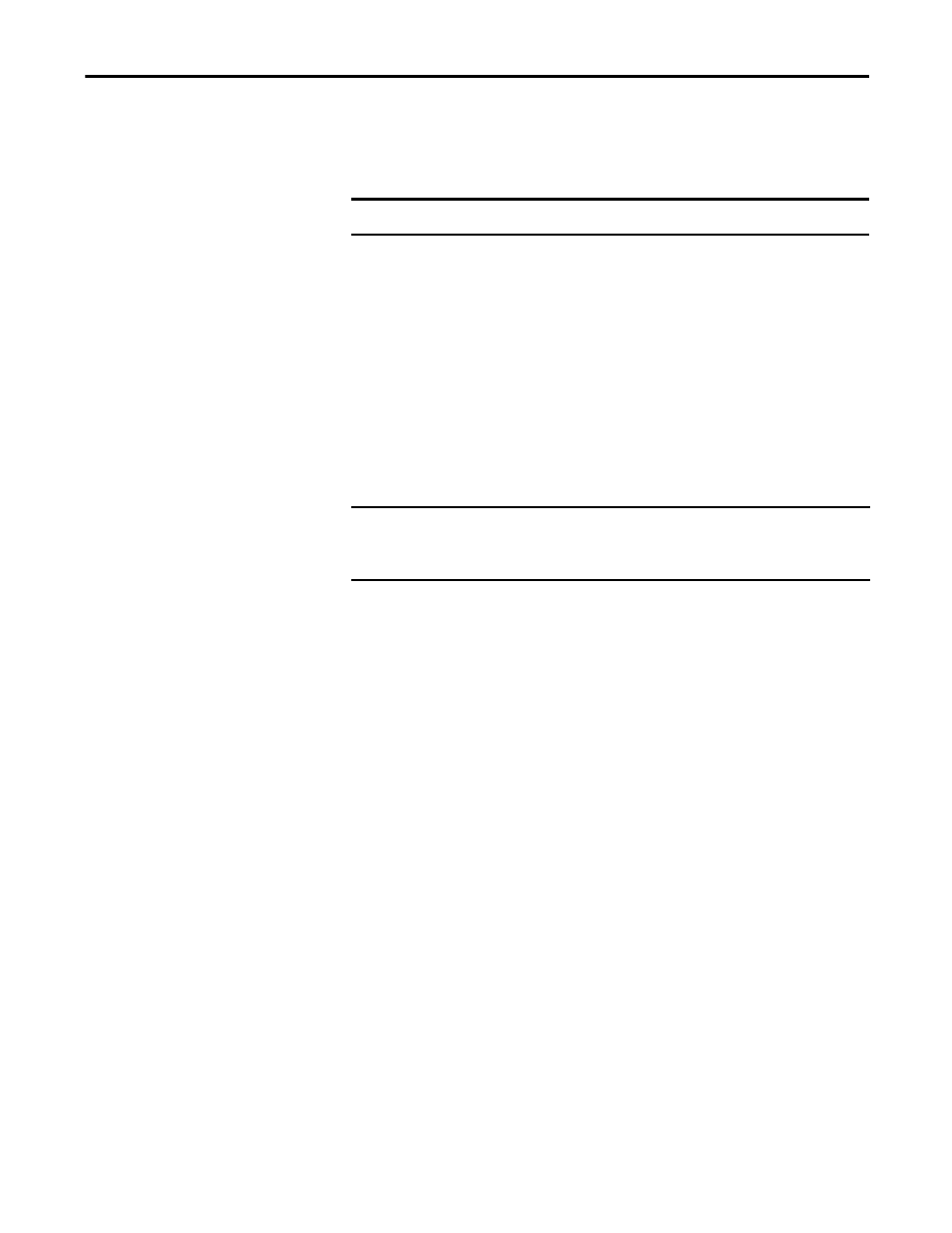
Rockwell Automation Publication 2094-RM001C-EN-P - May 2013
49
General Device and Feedback Monitoring Configuration
Chapter 5
Feedback Monitoring
The [Feedback Mode] parameter defines whether the feedback monitoring
devices are configured as a single encoder or as dual encoders. When two
encoders are used, the [Feedback Mode] parameter also defines the type of
discrepancy checking that is performed between the two encoders.
You choose the type of feedback device, either sine/cosine or incremental for
encoder 1 by using the [Primary Feedback Type] parameter. You also choose the
feedback type, resolution, and polarity of both encoders.
Configure the feedback type as rotary or linear by using the [Primary Feedback
Units] parameter. Configure the resolution in lines per revolution or lines per
millimeter by using the [Primary Feedback Cycles] parameter.
For dual encoder configurations, the resolution of the first encoder can be
different than the resolution of the second encoder. After discrepancy testing has
passed, the speed, relative position, and direction used by the drive are based on
encoder 1.
Feedback Polarity
Configure the direction of polarity to be the same as the encoder or reversed by
using the [Primary Feedback Polarity] parameter. The drive defines the normal
positive direction for encoders as A leading B. To use encoders where B leads A,
you must choose Negative for the [Primary Feedback Polarity] parameter. Set the
[Secondary Feedback Polarity] parameter so that the resulting speed direction is
of the same polarity as encoder 1.
IMPORTANT
Feedback devices can be a Sin/Cos or incremental feedback device.
IMPORTANT
For dual-encoder configurations, the resolution of the first encoder can be
different than the resolution of the second encoder, but it must be equal to or
higher than the resolution of the second encoder.