Single encoder, Dual encoders, Single encoder dual encoders – Rockwell Automation 2094-EN02D-M01-S1 Kinetix 6200 and Kinetix 6500 Safe Speed Monitoring Safety Reference Manual User Manual
Page 50
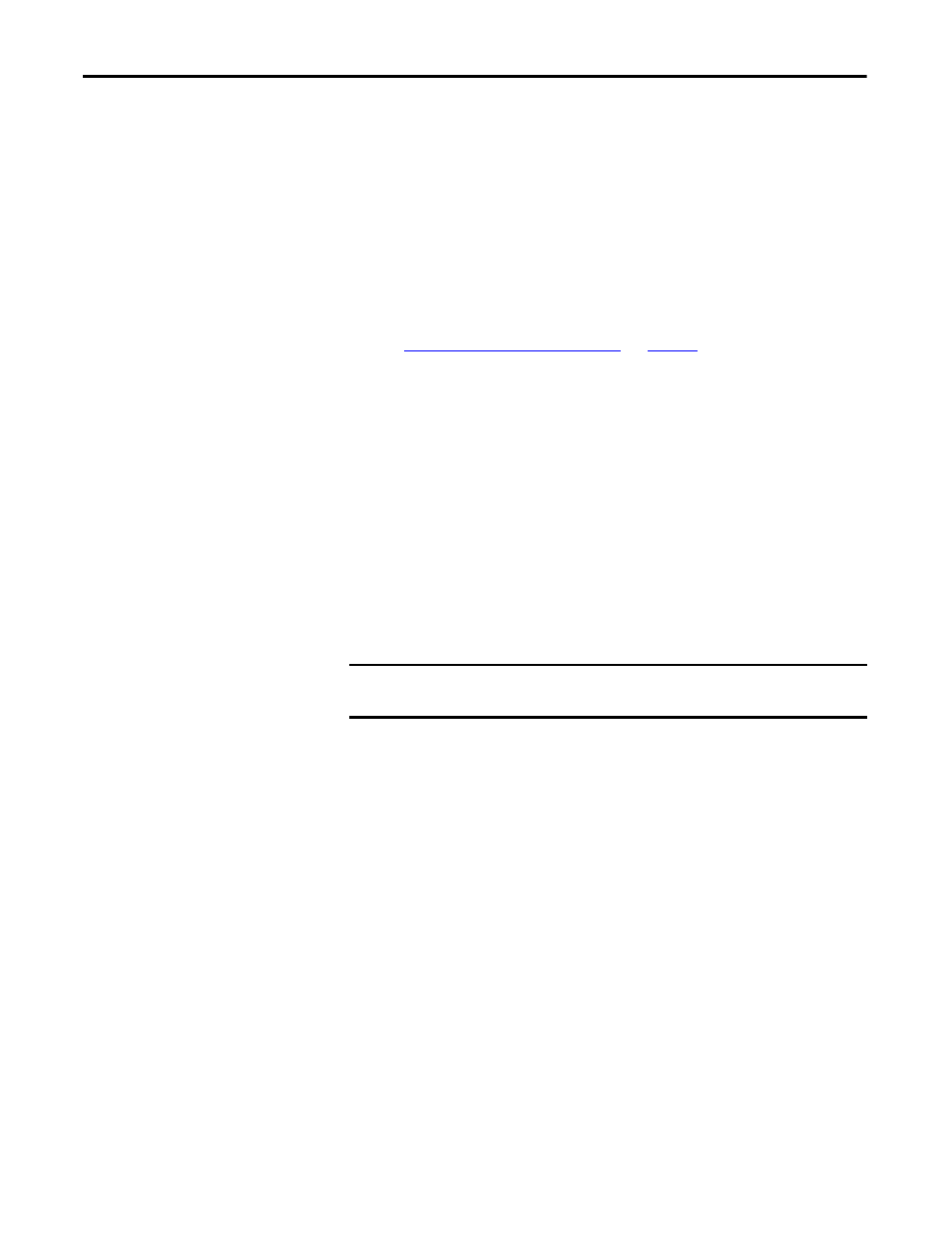
50
Rockwell Automation Publication 2094-RM001C-EN-P - May 2013
Chapter 5
General Device and Feedback Monitoring Configuration
Single Encoder
If the [Feedback Mode] parameter is set to Single Encoder, the single encoder
input is processed redundantly and cross-checked in a 1oo2 architecture. The
speed, direction, and stopped status are derived from the single encoder by the
1oo2 architecture.
Considerations for Safety Ratings
, for more information.
Dual Encoders
If the [Feedback Mode] parameter is set to Dual Encoders, each encoder input is
processed by a single channel and cross-checked in a 1oo2 architecture.
Discrepancy checking is performed between the two encoders. After the
discrepancy checks have passed, the speed, direction, and stopped status are
derived from encoder 1.
Speed and direction checks are affected by these parameters:
• Dual Feedback Speed Ratio, [Velocity Ratio]
• Dual Feedback Position Tolerance, [Position Discrepancy Tolerance]
• Dual Feedback Speed Discrepancy Tolerance, [Velocity Discrepancy
Tolerance]
TIP
If the [Feedback Mode] parameter is set to Single Encoder, the single encoder
input corresponds to the Kinetix 6200 motor feedback (MF connector)
connections.
TIP
If the [Feedback Mode] parameter is set to Dual Encoders, the encoder 1 input
corresponds to the Kinetix 6200 motor feedback (MF) connector and the
encoder 2 input corresponds to Kinetix 6200 auxiliary feedback (IOD)
connector.
IMPORTANT
All monitoring functions are based on the speed of encoder 1. The encoder 2
signal is used for fault diagnostics.