3 what to do if the motor does not rotate – Lenze PLC Designer V2.x User Manual
Page 233
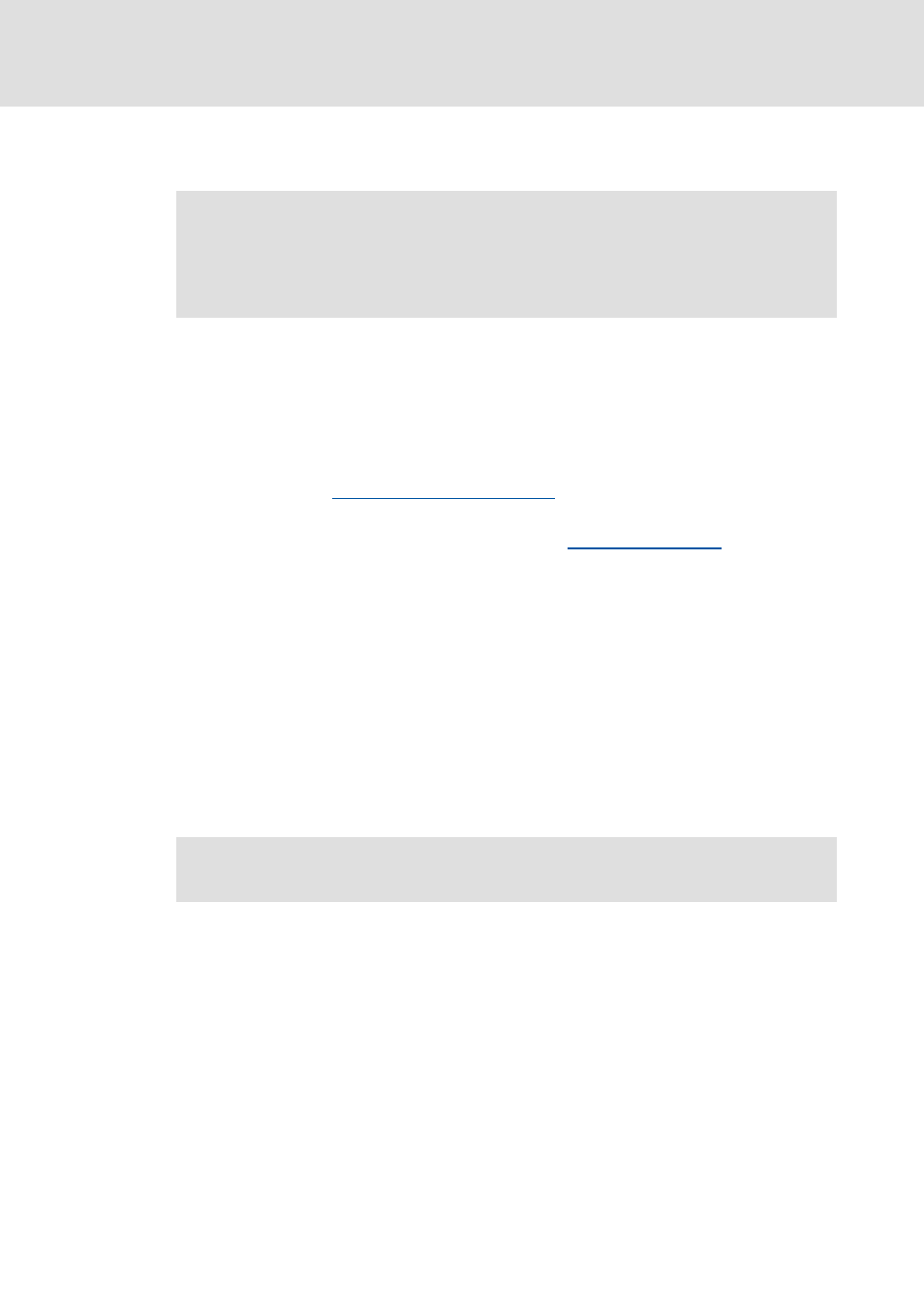
1.3 EN - 07/2012
L
233
PLC Designer V2.x| Lenze Application Samples
Diagnostics
What to do if the CAN bus is not running/CAN nodes do not respond?
10.2
What to do if the CAN bus is not running/CAN nodes do not respond?
By default the baud rate of the devices is set to 500K.
The CAN bus address (node ID) is set to 1 by default.
How to check the settings of CAN communication:
1. Check the CAN master settings of the EL100 or for the IPC/CPC in the »PLC
2. Check the wiring of the CAN bus cable (in the case of an individual cable, check the
terminal assignment) with the CAN nodes.
3. Check the setting of the DIP switches on the controllers.
4. Check the assignment of the terminating resistors (120 Ohm at the start and the
end of the bus, respectively).
5. Check the status information in the CAN diagnostics of the project.
6. Check the CAN status in the CAN nodes using the »Engineer« or »Global Drive
Control«.
Note: The CAN nodes have to be in the "Operational" status (see drive-specific
parameters).
7. Reset CAN node at the controller.
10.3
What to do if the motor does not rotate?
If the CAN bus is ready for operation and CAN communication works faultlessly, by
means of the drive-specific »Global Drive Control« or »Engineer« software it can be
checked whether the setpoint transmitted by the CAN master is accepted.
Check whether...
1. ...the digital inputs of the controllers for the loaded application are in the correct
position, and the suitable voltage level is applied.
2. ...the controller is enabled, CINH = 1 (TRUE).
Note!
Within a CAN bus line never two identical addresses must be used.
• In the sample project the addresses for the CAN nodes are already fixedly
entered or assigned.
Further information on the communication parameter settings can be found in
the documentation for the corresponding controller.