1 overview of tool movements, 1 ov erview of t ool mo v ements – HEIDENHAIN TNC 410 User Manual
Page 77
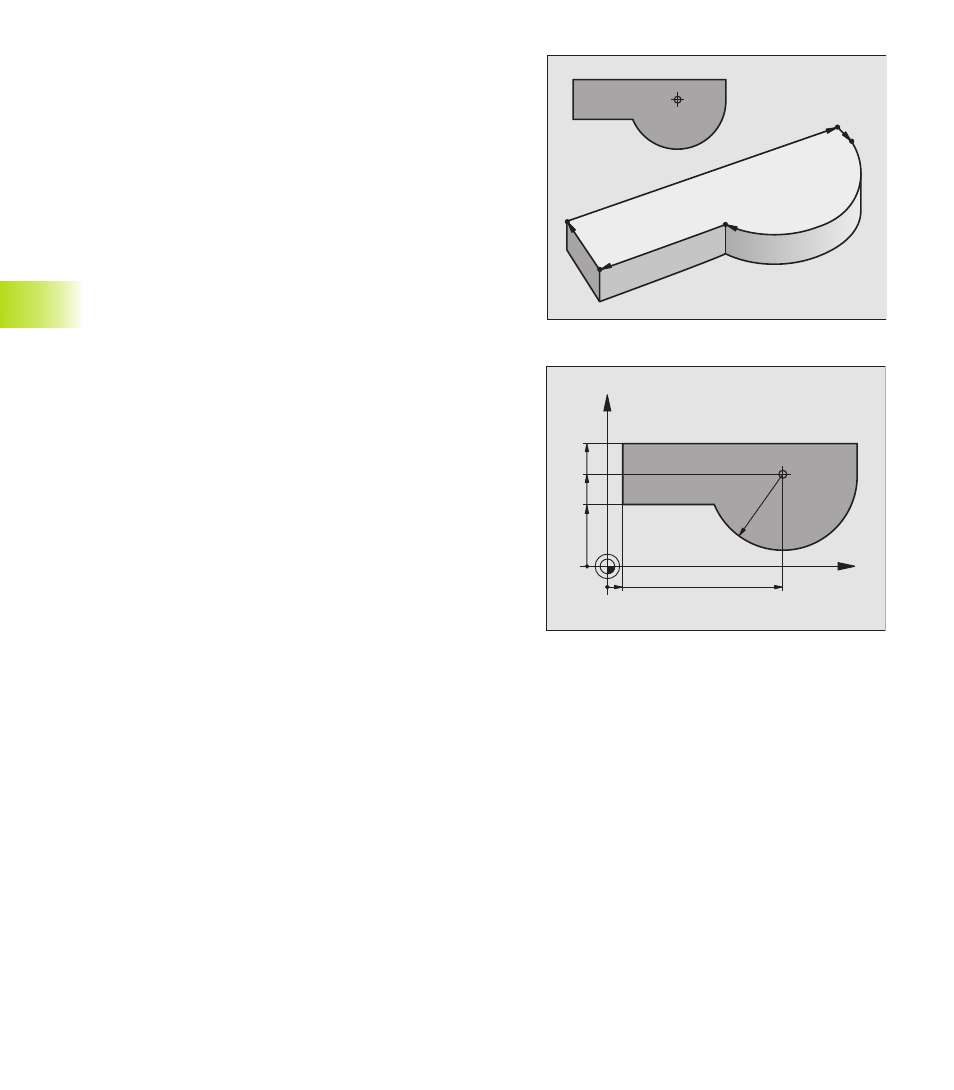
64
6 Programming: Programming Contours
6.1 Overview of Tool Movements
Path functions
A workpiece contour is usually composed of several contour
elements such as straight lines and circular arcs. With the path
functions, you can program the tool movements for straight lines
and circular arcs.
Free contour (FK) programming
If a production drawing is not dimensioned for NC and the
dimensions given are not sufficient for creating a part program, you
can program the workpiece contour with the FK free contour
programming and have the TNC calculate the missing data.
With FK programming, you also program tool movements for
straight lines and circular arcs.
Miscellaneous functions M
With the TNC’s miscellaneous functions you can affect
■
program run, such as a program interruption
■
machine functions, such as switching spindle rotation and coolant
supply on and off
■
contouring behavior of the tool.
Subprograms and program section repeats
If a machining sequence occurs several times in a program, you can
save time and reduce the chance of programming errors by
entering the sequence once and then defining it as a subprogram
or program section repeat. If you wish to execute a specific pro-
gram section only under certain conditions, you also define this
machining sequence as a subprogram. In addition, you can have a
part program call a separate program for execution.
How subprograms and program section repeats are used in
programming is described in Chapter 9.
Programming with Q parameters
Instead of programming numerical values in a part program, you
enter markers called Q parameters. You assign the values to the Q
parameters separately with the Q parameter functions. You can use
the Q parameters for programming mathematical functions that
control program execution or describe a contour.
In addition, parametric programming enables you to measure with
the 3-D touch probe during program run.
Programming with Q parameter is described in Chapter 10.
L
L
L
CC
C
X
Y
R40
115
10
80
60
40
CC
6.1 Ov
erview of T
ool Mo
v
ements