3 dr illing cy cles – HEIDENHAIN TNC 410 User Manual
Page 150
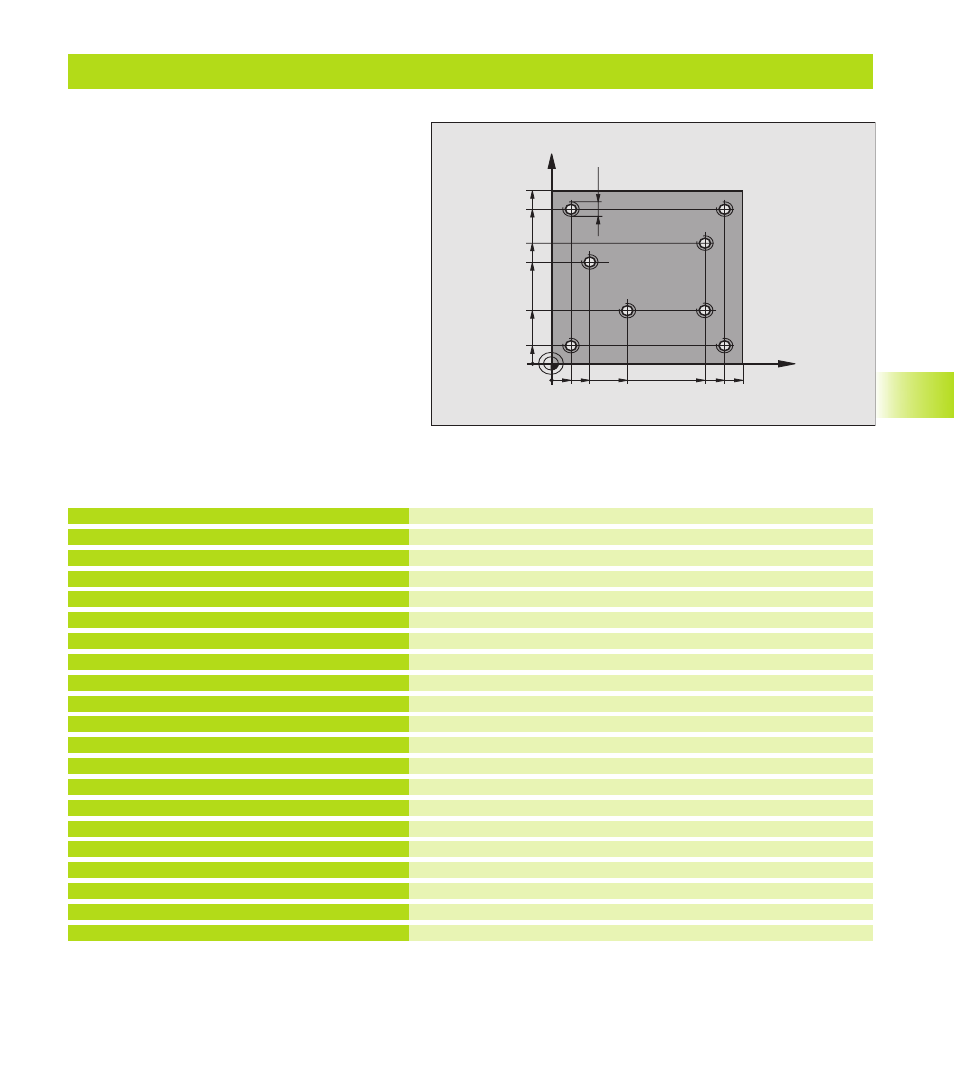
137
HEIDENHAIN TNC 410
Example: Calling drilling cycles in connection with point tables
Define the blank form
Tool definition of center drill
Define tool: drill
Tool definition of tap
Tool call of centering drill
Move tool to clearance height (Enter a value for F.
The TNC positions to the clearance height after every cycle)
Defining point tables
Cycle definition: Centering
Surface coordinate (0 must be entered here)
2nd set-up clearance (0 must be entered here)
Cycle call in connection with point table TAB1.PNT.
Feed rate between points: 5000 mm/min
Retract the tool, change the tool
0 BEGIN PGM 1 MM
1 BLK FORM 0.1 Z X+0 Y+0 Z-20
2 BLK FORM 0.2 X+100 Y+100 Z+0
3 TOOL DEF 1 L+0 R+4
4 TOOL DEF 2 L+0 R+2.4
5 TOOL DEF 3 L+0 R+3
6 TOOL CALL 1 Z S5000
7 L Z+10 R0 F5000
8 SEL PATTERN TAB1
9 CYCL DEF 200 DRILLING
Q200=2
;SET-UP CLEARANCE
Q201=-2 ;DEPTH
Q206=150
;FEED RATE FOR PLUNGING
Q202=2
;PLUNGING DEPTH
Q210=0
;DWELL TIME AT TOP
Q203=+0 ;SURFACE COORDINATE
Q204=0 ;2. SET-UP CLEARANCE
10 CYCL CALL PAT F5000 M3
11 L Z+100 R0 FMAX M6
Program sequence
■
Centering
■
Drilling
■
Tapping M6
The drill hole coordinates are stored in the point
table TAB1.PNT (see next page) and are called by the
TNC with CYCL CALL PAT.
The tool radii are selected so that all work steps can
be seen in the test graphics.
X
Y
20
10
100
100
10
90
90
80
30
55
40
65
M6
8.3 Dr
illing Cy
cles