Fieldbus device analog output or pid integration – Rockwell Automation PLC-5 Fieldbus Solutions for Integrated Architecture User Manual User Manual
Page 53
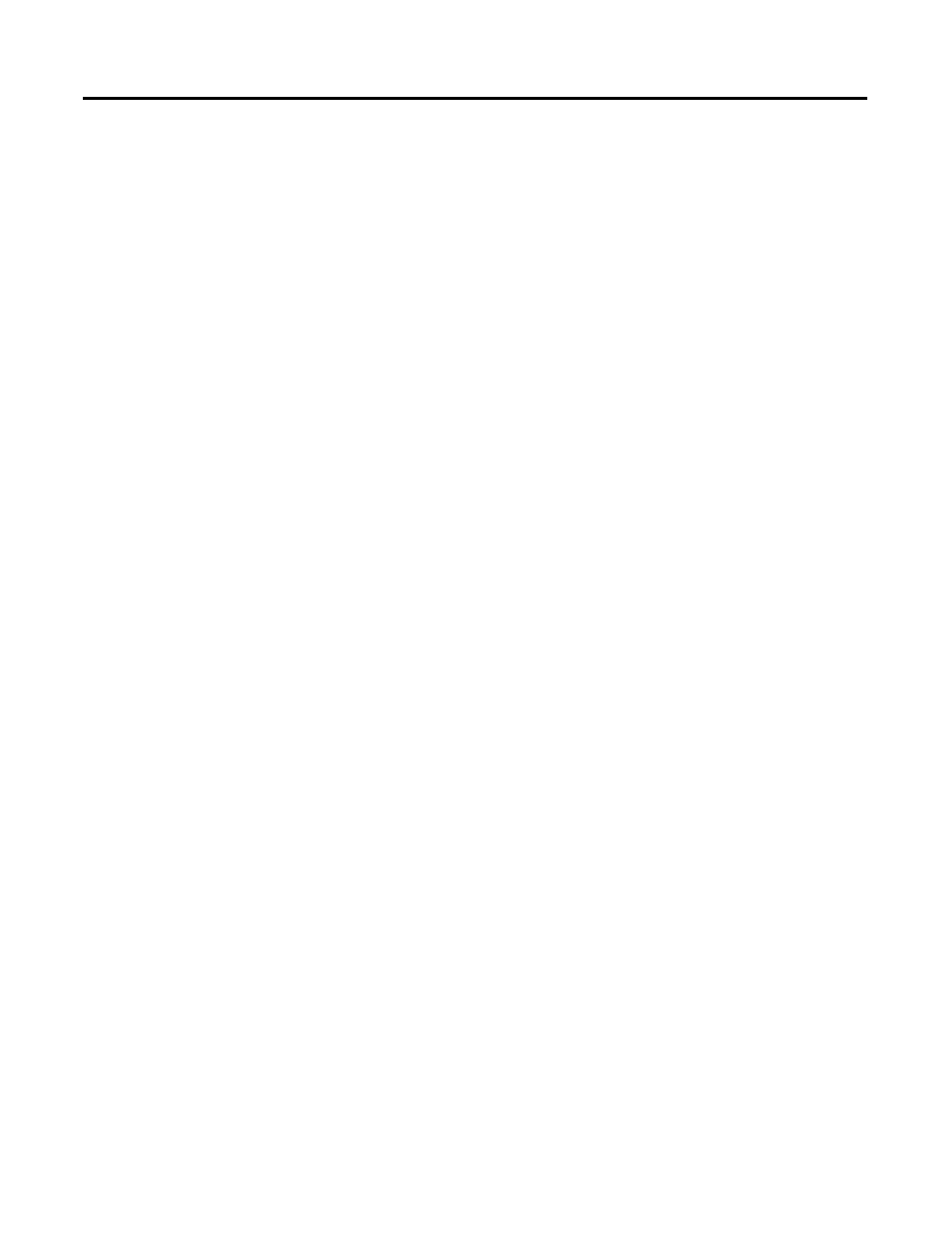
Publication 1757-UM006A-EN-P - May 2002
Integrating Fieldbus into Rockwell Automation Logix System 2-9
The fieldbus data quality of good, bad, and uncertain is mapped to
the appropriate ProcessLogix parameter of PVSTS, PVSTSFL.NORM,
PRSTSFL.BAD, or PVSTSFL.UNCER.
The fieldbus limit indications of no-limit, limited-low, limited-high,
and constant are mapped to the same four indications for
ProcessLogix. The fieldbus data substatus indicator maps only the
limited number of substatus conditions that have corresponding
ProcessLogix indications.
The handshaking provided by the substatus associated with Good
[cascade] status is not supported from an upstream Fieldbus device.
This means that control may not originate in the field and cascade
into the ProcessLogix Controller.
Fieldbus device Analog Output or PID integration
A user can functionally “wire” the output from a regulatory control
type function block contained in a Control Module in the
ProcessLogix Control Builder application to the input of an Analog
Output (AO) or Proportional, Integral, Derivative (PID) function block
in a fieldbus device residing on an H1 link. The Proportional, Integral,
Derivative (PID) function block is a typical ProcessLogix regulatory
control type function block. The Fieldbus Library Manager (FLM)
included in the R400 Control Builder makes this possible. The FLM
reads the manufacturer's DD for the fieldbus device and creates a
device template that is included in the Project tab of Control Builder.
The device template includes the device's fieldbus function blocks, so
it can be configured and integrated with control strategies through
Control Builder.