Speed regulation mode, Torque regulation mode – Rockwell Automation 23P PowerFlex Digital DC Drive User Manual
Page 325
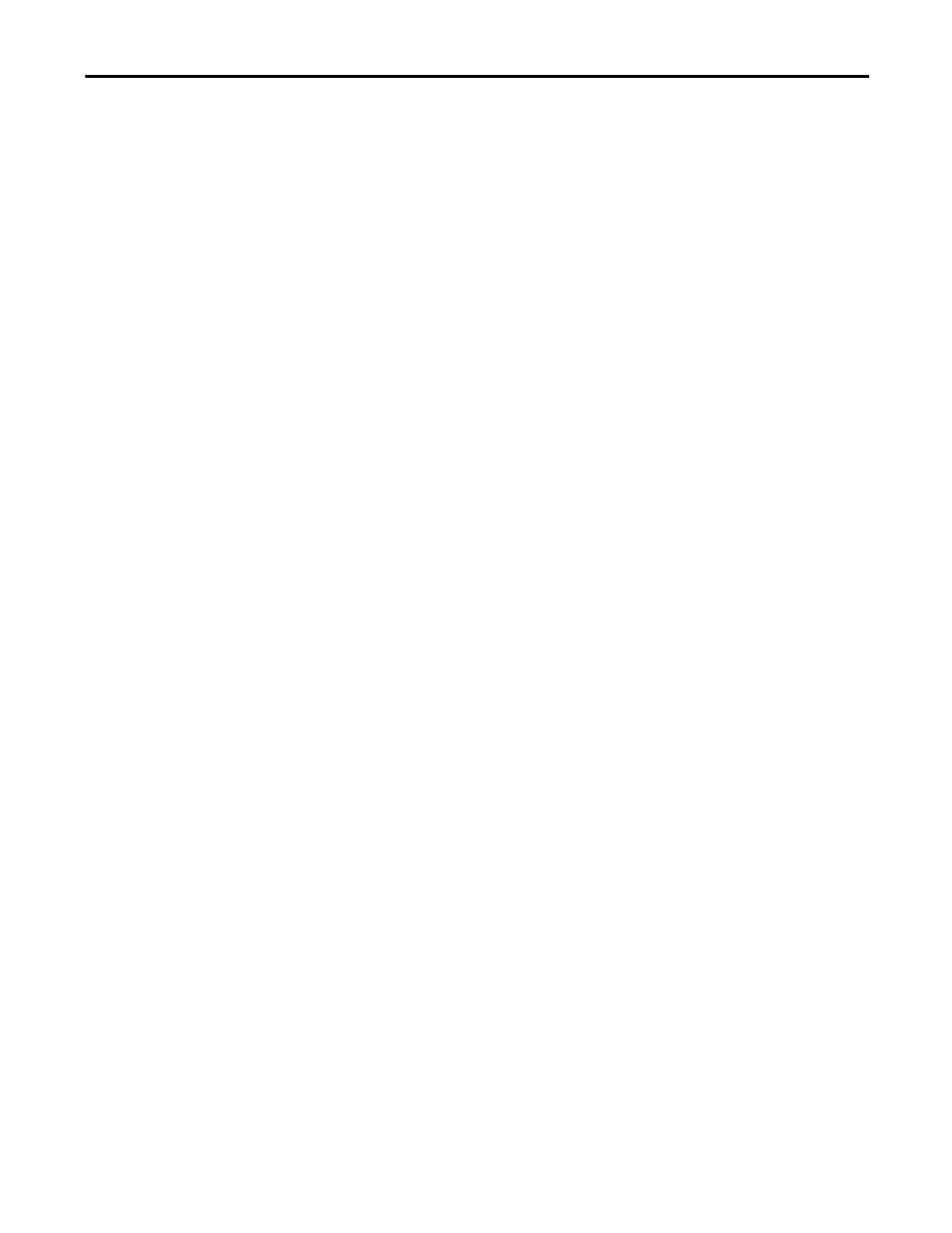
Rockwell Automation Publication 20P-UM001K-EN-P - July 2014
325
Application Notes
Appendix C
Speed Regulation Mode
When Par 241 [Spd Trq Mode Sel] is set to 1 “Speed Reg” the drive and motor
are operated in speed mode. The torque command changes as needed to maintain
the desired speed. This is the default setting. Operating as a speed regulator is the
most common and simplest mode to set up. Examples of speed regulated
applications are blowers, conveyors, feeders, pumps, saws, and tools.
In a speed regulated application, the speed regulator output generates the torque
reference. Note that under steady state conditions the speed feedback is steady
while the torque reference is a constantly adjusting signal. This is required to
maintain the desired speed. In a transient state, the torque reference changes
dramatically to compensate for a speed change. A short duration change in speed
is the result of increasing or decreasing the load very rapidly.
Note: Inertia compensation is summed with the output of the speed regulator.
Torque Regulation Mode
Par 241 [Spd Trq Mode Sel] is set to 2 “Torque Reg” for torque mode. In torque
regulation mode, the drive controls the desired motor torque. The motor speed is
the result of torque command and load present at the motor shaft. The reference
signal is equal to the value of Par 39 [Torque Ref ]. A torque regulated application
can be described as any process requiring some tension control. An example is a
winder or unwinder with material being “drawn” or pulled with a specific tension
required.
Note: If the material being wound/unwound breaks, the load will decrease
dramatically and the motor can potentially go into an overspeed condition.
Speed Limited Adjustable Torque (SLAT) Min Mode and SLAT Max
Mode
SLAT Min Mode (Par 241 [Spd Trq Mode Sel] set to 3) and SLAT Max Mode
(Par 241 [Spd Trq Mode Sel] set to 4) are for applications that require a smooth
transition from a torque mode to a speed mode of operation; for example: web
handling, center winders and center unwinds where the drive is normally
following a torque reference, but a break or slippage could occur. Direction of the
applied torque and direction of the material movement determine whether SLAT
Min or SLAT Max mode is used.